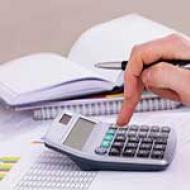
Из чего получается цемент. Из чего делают цемент
Самым распространенным скрепляющим материалом в строительстве является цемент, который изготавливается на основе магнезиальных или карбонатно-силикатных горных пород. Последняя разновидность занимает более 90% рынка и называется портландцементом. Процесс производства включает несколько этапов, ассортимент выпускаемых минеральных вяжущих материалов широкий, узнать по маркировке область применения порошка будет полезно каждому строителю.
Из чего делают цемент — основное сырье
Исходными материалами для производства служат твердые полезные ископаемые, вблизи которых и располагают цементные заводы. Используются при изготовлении клинкера — продукта совместного обжига горных пород — карбонатные камни и глины. Первая категория минеральных образований потребляется в большем количестве и представлена известняковыми разновидностями аморфной или кристаллической структуры, это:
- мел — мягкая горная порода белого цвета, состоит из карбоната кальция с примесью магния, оксидов металлов и зерен кварца;
- мергель — естественная смесь из 50-75% кальцитовых производных с 25-50% силикатных глинистых образований, хорошо подходит для производства ;
- ракушечник — это известняк из раковин морских животных, его метаморфизованная давлением при высокой температуре разновидность называется мрамором;
- доломит — помимо кальциевого карбоната СаСО3, имеет в составе магниевую составляющую: MgCO3.
Глинистые породы, привносящие в клинкер силикаты, это лесс, суглинки и глинистые сланцы. Для удешевления производства и придания цементу особых свойств в технологии используют легирующие добавки — глинозем, железо, кремний, отходы металлургических заводов.
Что такое цементный клинкер
Это продукт, полученный спеканием при температуре 1450°С двух горных пород: 75% известняка и 25% глины. Из обжиговой печи клинкер выходит в виде гранул Ø10-60 мм.
По химическому составу прокаленный щебень каждого из производителей может отличаться, приводится усредненный расклад в процентах:
- СаО — 67;
- SiO2 — 22;
- Al2O3 — 5;
- Fe2O3 — 3.
Щебень из печи — не единственный компонент в производстве портландцемента. Для замедления времени схватывания конечного продукта размол гранул до тонкодисперсного порошка производится с добавлением в клинкер до 6% сульфата кальция CaSO3, содержащегося в гипсе или гипсовом камне.
Измельчение ингредиентов осуществляется шаровыми мельницами с перекачиванием готового продукта в многотонные силосы пневматическим транспортом.
Изготовление цемента регламентируется государственными стандартами: ГОСТом 30515-2013 — общие техусловия, ГОСТами 10178-85 и 31108-2003 на строительные портландцементы. Для специальных видов разработаны отдельные нормативы.
Основные характеристики продукта
Показатели плотности цемента: насыпная — 900-1100 кг/м³, с уплотнением — 1400-1700. Значения истинного удельного веса достигают 3 т/м³. Существует несколько технических характеристик, по которым судят о качестве вяжущего порошка:
- Тонина помола — определяет : чем меньше частички, тем большую поверхность в один слой они покрывают. Контрольные замеры выполняют рассеиванием на сите с ячейкой 80 мкм.
- Водопотребность — количество влаги, необходимой для гидратации цемента и придания тесту пластичности. Излишняя вода в растворе приводит к образованию пор и трещин, снижению прочности.
- Морозостойкость — способность изделий на основе цементного порошка выдерживать многократные заморозки и оттаивания без разрушения. Необходимого показателя добиваются специальными добавками при замешивании раствора.
- Время схватывания — в зависимости от густоты замеса находится в диапазоне 0,7-10 часов. Показатель зависит и от количества гипса, добавляемого в клинкер при размоле.
- Прочность определяется по разрушению образца, изготовленного из цемента от каждой партии выпущенного раствора. Возраст кубиков устанавливается стандартом — 28 дней.
На все отгружаемые цементным заводом объемы заполняют паспорта качества, в которые вносят перечисленные характеристики. Потребители самостоятельно проводят входной контроль, чтобы подтвердить добросовестность поставщика.
Что такое марка цемента
Прочностной характеристикой портландцемента является его марка, которая устанавливается по результатам испытаний кубических образцов с гранью 10 см на сжатие. Состав раствора для заполнения форм: на 1 часть вяжущего порошка 3 меры чистого кварцевого песка.
После добавления воды масса перемешивается и остается твердеть на 28 дней. Заливается одновременно 6-10 металлоформ.
Из них произвольно отбирается 6 образцов и раздавливается под прессом. Среднее арифметическое давление рассчитывается по 4 кубикам, разрушившимся под наибольшей нагрузкой. Значения, измеренные в кг/см², укажут на марку цемента по ГОСТ 10178-85. Отображение напряжения в метрической системе единиц выполняется по ГОСТ 31108-2003 в МПа. Здесь распределение осуществляется по классу прочности цемента.
Получается, что для оценки прочностной характеристики одновременно пользуются старой и новой классификациями. Цифровой ряд марок: М200, М300, М400, М500, М600. Соответствующие значения класса твердости: В15; В22,5; В32,5; В42,5; В52,5.
Маркировка
Приведенные обозначения прочностных показателей портландцемента — это только небольшая часть зашифрованной в полной маркировке информации о свойствах изготовленного цемента.
В условиях одновременного использования стандартов с прежними обозначениями и от 2003 г. многие коды несут идентичные сведения.
Производители цементов стараются донести информацию о качестве и свойствах продукции, применяя термины обоих стандартов.
Что обозначает маркировка цемента по виду добавок
Помимо основных компонентов, в состав вяжущего минерального вещества вводятся присадки, позволяющие применять цемент в бетонах специального назначения. Информация об особых свойствах закладывается в маркировку продукции. Буквами шифруются порошок и добавки:
- ПЦ — портландцемент без улучшающих присадок;
- ШПЦ — при размоле клинкера добавлен шлак в количестве ≥20%, продукт называется шлакопортландцементом;
- ППЦ — , используется при бетонировании в обводненных условиях (пуццоланы — это продукты деятельности вулканов: пепел, туфы, пемза);
- СПЦ, ССПЦ, ССШПЦ — сульфатостойкие вяжущие, противокоррозионные;
- Б — быстротвердеющий порошок;
- БЦ — ; клинкер для его производства изготавливают из каолина и светлых сортов известняка;
- Г — быстросхватывающийся глиноземистый порошок, сырьевыми составляющими для обжига являются карбонатные породы и бокситы;
- ГФ — гидрофобный цемент для бетонных изделий в воде;
- ПЛ — пластифицированный, обеспечивает удобство укладки раствора даже при низких температурах;
- ВРЦ — влагонепроницаемый расширяющийся цемент, твердеет в любой среде.
В маркировке ГОСТ 10178-85 количество добавок обозначается буквой и числом процентов: Д0, Д5, Д20. В конце шифра указывается стандарт, по которому изготовлен продукт. Пример: ПЦ 400-Д20-Б-ПЛ ГОСТ 10178-85 — портландцемент прочностью 400 кг/см² с добавками в количестве 20%, быстротвердеющий, пластифицированный.
Расшифровка маркировки цемента по новым нормативам
Кодирование информации о продукции по ГОСТ 31108-2003 основано на разделении видов цемента на 5 групп, обозначаемых римскими цифрами. Первые 3 буквы взяты из названия порошка — ЦЕМ.
У каждого объединения есть признаки, указывающие на особенности изготовления:
- I — портландцемент бездобавочный, состоит на 95-100% из цементного клинкера;
- II — эта группа подразделяется на подклассы А с добавками 6-20% и В — 21-35%. Здесь же находятся пуццолановые цементы, содержащие <20% пуццолана, и композитные, в которых присадки суммарно не превышают того же значения;
- III — шлакопортландцемент при содержании шлаков 36-65%;
- IV — пуццолановый цемент с добавкой 21-35%;
- V — композиционный порошок, включающий в состав 11-30% шлака и в тех же пределах пуццолан.
У каждой из присадок в обозначении своя буква: И — известняк, З — зола уноса, МК — микрокремнезем, К — композитная добавка, Г — глиеж, Ш — шлак, П — пуццолан. После следует цифра класса прочности, за ней буквы: Н — нормальное время твердения, Б — быстрое схватывание. Пример: шлакопортландцемент ЦЕМ III/А 32,5Н ГОСТ 31108-2003. Расшифровывается так: прочность цемента 32,5 МПа, он нормально-твердеющий, содержит 36-65% шлака.
Марки цемента и их применение
Используются портландцементы в соответствии с маркировкой, которая прямо указывает на особые условия, если они имеются. Для строительных работ при выборе марки обращают внимание на показатель класса прочности или марки цемента.
Действия по обустройству в зависимости от твердости вяжущего порошка:
- М200 — цемент предназначен для штукатурных работ, изготовления ;
- М300 — соответствует монолиту М200, применяется для бетонирования подстилающих поверхностей под фундаменты, заливки оснований под малоэтажные строения;
- М400 — строительство железобетонных сооружений прочностью М300, дорожных покрытий, тротуарной плитки, опорных конструкций;
- М500 — все виды наружных бетонных работ, изготовление аэродромных плит и гидротехнических сооружений из монолита М400.
Составы растворов могут различаться и задаются под условия возводимого объекта. Рецептура смесей определяется проектом.
Цемент – вяжущая субстанция, которая имеет свойство твердеть в воде и на открытом воздухе. Разберемся, из чего делают цемент, правда, тут еще все заивист от . Он образуется путем измельчения клинкера, гипса и специальных добавок. Клинкер – это результат обжига сырьевой смеси, которая включает в себя известняк, глину и прочие материалы (доменный шлак, нефелиновый шлам, мергель). Ингредиенты берут в определенном соотношении, что обеспечивает образование силикатов кальция, алюмоферритной и алюминатной фаз.
Впервые патент на цемент был зарегистрирован в 1824 году, в Англии, Д. Аспиндом. Тогда автор патента смешивал пыль извести с глиной, обрабатывал смесь посредством высокой температуры. В результате получал серый клинкер. Далее материал размалывался и заливался водой.
Из чего состоит цемент сегодня? По-прежнему клинкер – это основной компонент, входящий в состав цемента. Именно от него зависят свойства и крепость строительного материала. Кроме того, в состав входят активные минеральные добавки (15%) в соответствии со стандартами производства. Они незначительно влияют на основные свойства и технические характеристики строительного материала. Если увеличить количество добавок до 20%, то свойства цемента будут несколько изменены, а называться он будет пуццолановым цементом.
В рассыпанном состоянии составляет 900-1300 кг/куб м, уплотненном – до 2000 кг/куб. м. Рассчитывая емкость складов для хранения, вес цемента равняется 1200 кг/куб. м. Выпуск цемента без добавок регламентирует ГОСТ 10178-76, с добавками – ГОСТ 21-9-74.
Основные характеристики цемента
В зависимости от того, из чего сделан цемент, материал имеет разные свойства. К основным из них относятся:
1. Прочность
. Это параметр, который отвечает за разрушение материала под воздействием определенных условий. В зависимости от механической прочности, выделяют четыре типа цемента: 400, 500, 550 и 600.
2. . Определяется путем укладки цементного теста нормальной густоты на ровную поверхность – цемент должен равномерно изменять свой объем при высыхании. Иначе его нельзя будет применять в строительстве ввиду возможных разрушений покрытия в результате чрезмерного напряжения. Изменения объема проверяются путем кипячения застывших лепешек из цемента.
3. Зернистость помола
. Параметр оказывает влияние на скорость высыхания и прочность. Чем мельче помол, тем лучше и прочнее цемент, особенно на первом этапе затвердения. Зернистость помола определяется удельной поверхностью частиц, которые входят в состав 1 кг цемента, и колеблется в пределах 3000-3200 кг/куб. м.
4. Плотность
. Затраты воды для создания смеси. Это количество воды при затворении, необходимое для нормальной укладки и высыхания материала. Чтобы сократить ее расход и повысить пластичность цемента, применяют пластифицирующие органические и неорганические вещества. К примеру, сульфидно-дрожжевую бражку.
5. Стойкость к морозам
. Параметр позволяет определить способность выдерживать временное замораживание воды, вследствие которого ее объем увеличивается на 8-9%. Вода давит на стенки цементного (бетонного) покрытия, а это, в свою очередь, нарушает структуру раствора, постепенно разрушая его.
6. Сцепление с арматурой
.
7. Тепловыделение
– в процессе застывания цемента выделяется тепло. Если это происходит медленно и постепенно, то покрытие застывает равномерно, без появления трещин. Количество и скорость выделения тепла можно уменьшить путем использования специального минералогического состава, который добавляют в раствор.
Сегодня производится множество видов цемента. То, из чего состоит цемент, в большей степени влияет и на его свойства. В зависимости от сырьевой основы, выделяют такие виды цемента:
- известковый;
- мергелистый;
- глинистый цемент с добавками шлака и боксита. Его особенность – водонепроницаемость, морозоустойчивость, огнеустойчивость.
В основном при изготовлении цемента применяют глинистые и карбонатные соединения. Иногда – искусственное сырье (отходы, шлаки) или другие природные материалы (остатки глинозема).
Различают . Портландцемент быстро твердеет и может содержать в своем составе минеральные добавки от 10 до 15%. Клинкер и гипс (основные компоненты), входящие в его состав, обжигают при температуре 1500 градусов Цельсия. Портландцемент активно применяют для проведения современных строительных работ. Его главным свойством является способность превращаться в твердую каменную глыбу даже при взаимодействии с водой.
Кроме портландцемента и шлакопортландцемента, различают следующие виды цемента:
- гидравлический;
- напрягающий – имеет свойство быстро схватываться и высыхать;
- тампонажный – предназначен для бетонирования газовых и нефтескважин;
- декоративный (белый);
- сульфатостойкий - его отличительная особенность – низкая скорость затвердевания и повышенная морозоустойчивость.
Сферы использования
Очень часто цемент применяют в строительстве для создания бетона и армированных конструкций. Марка 400 используется для заливки фундамента и сооружения балок перекрытий в высотных зданиях.
Во все времена человек для своих нужд занимался строительством, начиная древними постройками и заканчивая современными техническими шедеврами. Для того чтобы здания и другие постройки оставались надежными, необходимо вещество, которое не даст распадаться составляющим частям по отдельности.
Цемент - это материал, который служит для связки строительных элементов. Его применение велико в современном мире. Он используется в различных сферах деятельности человека, и от него зависит дальнейшая судьба всех сооружений.
История возникновения
Стали использовать еще в древние времена. Сначала это была необожженная глина. Благодаря своей простоте получения и распространенности она применялась повсюду. Но из-за слабой вязкости и устойчивости глина уступила место термически обработанным материалам.
В Египте были получены первые качественные строительные вещества. Это известь и гипс. Они обладали способностью твердеть на воздухе, благодаря чему и получили широкое применение. Эти стройматериалы удовлетворяли требованиям, пока не начало развиваться мореплавание. Стало необходимо новое вещество, которое сопротивлялось бы действию воды.
В XVIII веке был изобретен материал -- романцемент. Это продукт, который мог твердеть как в воде, так и на воздухе. Но усиленное развитие промышленности требовало более качественных материалов и вяжущих свойств. В XIX веке было изобретено новое вещество для связывания. Оно получило название портландцемент. Этот материал используется и по сей день. С развитием человечества к вяжущим веществам предъявляются все новые требования. Для каждой отрасли используется своя марка, обладающая необходимыми свойствами.
Состав
Цемент - это основная составляющая строительной отрасли. Главными компонентами в ней являются глина и известняк. Они смешиваются между собой и подвергаются термической обработке. Затем получившаяся масса размалывается до состояния порошка. Серая мелкая смесь - это и есть цемент. Если его смешать с водой, то масса со временем станет, как камень. Главной особенностью является способность твердеть на воздухе и сопротивляться воздействию влаги.
Получение цементного раствора
Чтобы строительная масса была необходимого качества, в состав должно входить не менее 25% жидкости. Изменение соотношения в любую сторону приводит к снижению эксплуатационных свойств раствора, а также его качества. Схватывание происходит через 60 минут после добавления воды, а после 12 часов смесь теряет свою эластичность. Все зависит от температуры воздуха. Чем она выше, тем быстрее затвердеет масса.
Для получения раствора необходим песок, в который добавляется цемент. Получившаяся смесь тщательно перемешивается и заливается водой. В зависимости от производимых работ раствор может быть обычным или обогащенным. Первый состоит из пропорций 1:5, а второй - 1:2.
Виды и производство цемента
На данный момент изготавливается много разновидностей вяжущего материала. Каждому присуща своя степень твердости, которая указывается в марке.
К основным видам относятся:
- Портландцемент (силикатный). Это основоположник всех видов. Любая марка использует его как фундамент. Отличием является количество и состав добавок, которые придают цементу необходимые свойства. Сам порошок имеет серо-зеленый цвет. При добавлении жидкости он твердеет и прочнеет. Не используется отдельно в строительстве, а идет как основа для создания
- Пластифицированный состав снижает затраты, обладает способностью убирать подвижность раствора и отлично сопротивляется воздействию холода.
- Шлаковый цемент. Это результат дробления клинкера, и добавления активных присадок. Используется в строительстве для приготовления растворов и бетона.
- Глиноземистый. Обладает высокой активностью, скоростью схватывания (45 минут) и затвердевания (полное происходит уже через 10 часов). Также отличительным свойством является повышенная сопротивляемость влаге.
- Кислотоупорный. Образуется в результате смешивания кварцевого песка и кремнефтористого натрия. Для приготовления раствора добавляется натриевое Преимущество такого цемента - устойчивость к воздействию кислот. Недостаток - небольшой срок службы.
- Цветной. Образуется при смешивании портландцемента и пигментных веществ. Необычный окрас используется для декоративных работ.
Производство цемента состоит из 4 этапов:
- Добыча сырья и его приготовление.
- Обжиг и получение клинкера.
- Помол до состояния порошка.
- Добавка необходимых примесей.
Способы производства цемента
Есть 3 метода, которые зависят от подготовки сырья к термической обработке:
- Мокрый. При этом методе на всех этапах производства цемента присутствует необходимое количество жидкости. Применяется в ситуациях, когда основные составляющие не могут участвовать в технологическом процессе без использования воды. Это мел с повышенным содержанием влаги, пластичная глина или известняк.
- Сухой. Все этапы изготовления цемента проходят с материалами, содержащими минимальное количество воды.
- Комбинированный. Производство цемента включает в себя и мокрый, и сухой методы. Первоначальная цементная смесь изготавливается с водой, а затем ее максимально фильтруют на специальном оборудовании.
Бетон
Это строительный материал, который образуется при смешивании цемента, наполнителя, жидкости и необходимых добавок. Другими словами, он представляет собой затвердевшую смесь, в которую входят щебень, песок, вода и цемент. Бетон отличается от строительного раствора своим составом и размерами наполнителя.
Классификация
В зависимости от того, какой связывающий материал используется, бетон может быть:
- Цементный. Самый распространенный в строительстве вид. В основе используется портландцемент, а также его разновидности.
- Гипсовый. Обладает повышенной прочностью. В качестве вяжущего материала берется
- Полимерный. В основе лежат Подходит для работ на горизонтальных и вертикальных поверхностях. Является прекрасным материалом для отделочных и ландшафтных работ.
- Силикатный. Вяжущим материалом являются известь и кремнеземистые вещества. По своим свойствам очень похож на цементный и используется в производстве железобетонных конструкций.
В зависимости от назначения, бетон может быть:
- Обычный. Используется в промышленном и гражданском строительстве.
- Специальный. Нашел свое применение в гидротехнических сооружениях, а также при дорожных, изоляционных и декоративных работах.
- Специального назначения. стойкий к химическим, термическим и другим специфическим воздействиям.
Стоимость цемента
Изготовители выпускают продукцию, расфасованную по массе. Вес мешков цемента бывает 35, 42, 26, а также 50 кг. Выгоднее всего покупать последний вариант. Он наиболее оптимально подходит для загрузки и позволяет сэкономить на упаковке. В зависимости от объекта, на котором будут вестись ремонтные работы, используется цемент различных марок, имеющий свою собственную стоимость. При оплате учитывается каждый мешок цемента. Цена его фиксированная и может колебаться в зависимости от требований продавца.
Перед тем как начать рассчитывать денежные затраты, необходимо определиться с еще одним нюансом. Иногда можно увидеть объявление, в котором указана стоимость ниже стандартной. Не стоит попадаться на такую ловушку. В таких случаях дорогой цемент разбавляется более дешевым. Выигрывая несколько рублей, вы потеряете качество строительного материала.
Возьмем один 50 килограммовый мешок цемента. Цена марки М400Д0 составит 220 рублей. Стоимость других может изменяться, но в среднем это:
- М400Д20 - 240 рублей.
- М500Д0 - 280 рублей.
- М500Д20 - 240 рублей.
Если нужно использовать только пару мешков цемента, то их наиболее выгодно покупать в ближайшем магазине по продаже строительных материалов. А если нужно большое количество, то следует обратиться на завод-изготовитель.
Расход цемента
Перед выполнением любых строительных работ возникает вопрос о том, сколько цемента необходимо и какой консистенции должен быть раствор. В идеальном случае должна сохраняться прочность и не превышаться пропорциональность составляющих.
Когда предстоит ответственная и серьезная работа, смешивать цемент и песок «на глаз» недопустимо. Если не жалеть вяжущий материал, то при больших объемах он обойдется в огромные суммы денег.
Так сколько цемента необходимо для производимых работ? Ответить помогут строительные нормативы (СНиП). Здесь учитываются все причины, влияющие на изготовление смеси. Ориентируясь на марку состава и учитывая все факторы, можно четко узнать норму расхода цемента на 1 кубический метр раствора.
Главная особенность, которую не учитывают многие застройщики, - это то, что цемент распределяется в пустотах между частицами песка. Помните, что состав обладает активностью. При долгом хранении в помещении марка 500 через несколько месяцев станет 400. Поэтому при покупке всегда следует просить сертификат с датой выпуска.
Без использования цемента не обходится ни одно капитальное строительство или восстановительные строительные работы. Материал используют как при изготовлении различных типов фундамента, так и для возведения стен. Однако, не все знают, из чего делают цемент, и каким образом.
Открытие материала
Изготовление цемента осуществляют во многих странах мира, в том числе и в России. Несколько крупных заводов обеспечивают различные отрасли промышленности этим нужным сырьем для материальных отраслей. Изобретателем, согласно данных Википедии, считается англичанин Джозеф Аспдин. Он в первой четверти XIX века запатентовал порошок серого цвета, дав ему название «портландцемент» в честь расположенного неподалеку города Портленд.
Способы производства вяжущих веществ были изобретены где-то в 3-4 тысячелетии до нашей эры, но впервые патент на его изобретение был получен в 1824 году
Данное неорганическое вещество имеет искусственное происхождение. Оно используется как самостоятельно, так и в составе разнообразных растворов:
- кладочные;
- бетонные;
- штукатурные.
Основное отличие от иных вяжущих веществ, типа алебастров или известей, заключается в том, что материал приобретает высокую твердость при наличии значительного количества влаги.
Действующие нормативы
Производство цемента регламентировано действующим законодательством. Технические условия на выпускаемую продукцию должны согласовываться с ГОСТ № 10178, установленным в 1985 году. Согласно нему в составе принимается определенное количество минеральных добавок.
Более ранним стандартом является ГОСТ № 10178-76, но его действие прекращено с внедрением нового ГОСТа, хотя разница между ними не является существенной. Заметны различия лишь в отдельных позициях, которые не оказывают значительного влияния на конечный продукт.
Также используется производителями стандарт ГОСТ 15825-1980. Он в большей степени регламентирует цветовую дифференциацию продукта.
Производители постоянно работают над усовершенствованием своего продукта. В ход идут эксперименты как с физико-химическим составом материала, так и с выбором пропорций разных составляющих.
Из чего состоит цемент
Выясним, из чего состоит цемент. Традиционными компонентами для него являются гипс, клинкер и набор связующих добавок. Степень измельчения клинкера является важным фактором.
Клинкер
Он является базовым компонентом и формирует главные итоговые характеристики будущей цельной плиты. Образуется материал после обжига сырьевой массы с определенной температурой до получения гранулированных комочков диаметром 1-5 см. для термообработки задействуют спецпечи. Данный этап, из всех этапов производства, как делают цемент, является наиболее энергозатратным и трудоемким.
Известняк с глиной
Добывают в открытых карьерах. Затем они проходят предварительный этап обработки и отправляются в мельницу для формирования из них шламов. Полученный материал проходит сырьевые мельницы и отправляется в шламбассейны.
Мелкий шлам отправляют в печь, которая вращается вокруг собственной оси. Такие узлы могут иметь длину до 200 м и диаметр несколько метров, как на уральском заводе Lafarge в Челябинске. Топливом для них служит природный газ, ведь необходимо создать рабочую температуру в 1450°С.
Сырье во время термообработки частично спекается, формируя клинкер. Печи располагают горизонтально с наклоном до 40, чтобы дать возможность перемещаться массе внутри.
Масса состоит из диоксида кальция и кремнезема. Эти химические элементы оказывают влияние на долговечность будущих изделий и прочность скрепления строительных материалов с вяжущим составом.
Изготовление цемента продолжается в холодильнике, где у состава понижают температуру. На следующей стадии происходит дробление и передача в бункер для перемалывания в пыль.
В современном производстве цемента и его составляющих предусмотрены способы экологической защиты, к которым относятся электрофильтры. Они блокируют выход пыли эффективнее традиционных способов в 10-30 раз.
Пропорция глины и известняка в составе клинкера составляет 1 к 3. Такие вещества входят в цементы различных компаний. Зерно готового продукта составляет в пределах 1-100 мкм диаметра.
Также к востребованным материалам относятся: доменный шлак, мергель, мел, лесс, сланец и пр.
Гипс
Состав цемента на 3-7% состоит из гипса. С его помощью производители варьируют сроки хранения сырья. Он отвечает за качество «отвердения». Исследование сырья показывают, что для цемента может применяться чистый материал или гипсовый камень, имеющий разнообразные примеси.
Добавки
Примеси, внедряемые производителями, способны усиливать характеристики продукта или придавать ему новые свойства. Популярными являются вещества, обеспечивающие такие свойства:
- повышающие сопротивляемость низкотемпературным режимам;
- для расширения диапазона применения готового продукта;
- минимизирующие влагопоглощение;
- обеспечивают пластичность.
Свойства позволяют делить продукт на определенные группы, подбирая оптимальный для каждого конкретного случая. Они определяют специфику эксплуатации. Минеральные добавки входят в состав цемента на 10-15%.
Также к востребованным материалам относятся: доменный шлак, мергель, мел, лесс, сланец и пр.:
- мел относится к осадочным породам, легко растирающимся и измельчающимся;
- мергель - также осадочная порода, которая находится ниже известняка, ближе к глинистым пластам, иногда имеет рыхлую фактуру и зависит от массовой доли глинистых составляющих (материал используется для работы с огнеупорными средами, например, печи или камины);
- известняки предпочтительней выбирать пористые, так как их состав и свойства имеют небольшой порог прочности и в них исключены кремневые образования;
- к востребованным глинистым пародам относятся лессовидные суглинки, лесс, суглинок, глинистый сланец.
На каждом производстве имеется собственная лаборатория. Там ведется регулярный учет качества выпускаемой продукции. Специалисты контролируют дозы входящих компонентов и добавок. Также на территории проводятся испытания прочности. Результаты тестирования подтверждаются соответствующими документами.
Определяя, из чего состоит цемент, необходимо указать его ориентировочный химический состав:
- две трети в нем занимает оксид кальция СаО до 67%;
- менее четверти содержится диоксида кремния SiO 2 до 22%;
- двадцатая часть оксидов алюминия Al 2 О 3 5%;
- порядка 3% оксида железа Fe 2 O 3 ;
- иные компоненты.
Марка указывается после буквы «М» на лицевой части упаковки и обозначает, сколько килограммов выдержит квадратный сантиметр поверхности.
ВИДЕО: Химический состав цемента
Различные технологии изготовления цемента
Существует несколько используемых технологий изготовления. Отличие между ними заключается в основном в процессе подготовки сырья. Применяют такие методики:
- сухая;
- мокрая;
- комбинированная.
Сухая технология
Является наиболее прогрессивной, так как делают цемент по ней, совмещая несколько процессов. Это позволяет снизить себестоимость производства. Сушку и помол при таком варианте проводят в шаровой мельнице. В нее проникают горячие газы, поток которых направлен к заготовкам. В результате шихта получается в виде измельченной пыли.
Мокрая
Для мокрой технологии задействуют мел без извести. Перемешивание элементов осуществляется в спецбарабане. Там же проводится помол. Внутрь барабана пропускают определенное количество воды, от чего технология называется «мокрой».
Комбинированная
В комбинированной методике применены различные способы. Например, в отдельных случаях происходит мокрая обработка, а затем заготовленную массу доводят до полувлажного состояния с 18-20% влаги. Далее осуществляется гранулирование.
Для бытовых условий понадобится печь с высокотемпературным нагревом. Также не обойтись без подготовленных мельниц, создающих необходимую фактуру. Необходимо учесть, что потребуется затратить много энергии на переработку материала.
Технология приготовления цемента
Измельчаем 1 часть подготовленной глины и три части известняка. Тщательно перемешиваем состав и перекладываем в барабанную печь. Температурный режим в ней ставим на 1450°С. В итоге у нас оказывается клинкер в виде крупных комьев. Домешиваем 5-6% гипса к составу. Хранить приготовленный цемент своими руками необходимо подальше от влажных мест.
ВИДЕО: Процесс производства цемента на примере одной компании
Слово цемент знакомо каждому. Даже те, кто никогда не занимался строительством, знают, что цемент нужен для раствора при кирпичной кладке, что он является основным компонентом железобетонных изделий. Однако мало кому известно, из чего делают цемент.
Особенности
Цемент распространен повсеместно. Он применяется не только при возведении всевозможных строений. Без него не обойтись при проведении реставрационных и ремонтных работ. Пока еще замены цементу не существует. Этим оправдывается его востребованность.
Основой строительного материала являются вяжущие неорганические составляющие. Цемент необходим при производстве панельных плит. Из него делают штукатурные и кладочные растворы. В составе бетонов цементу отводится одно из главных мест.
По сути, цемент – это мелкодисперсный порошок. Основная особенность порошковой массы заключается в том, что при взаимодействии с водой она постепенно начинает твердеть. Процесс взаимодействия двух компонентов (цемента и воды) завершается образованием сплошного массива, по твердости схожего с природным камнем.
Прочная структура образуется при избыточной влажности. Происходит реакция как на открытом воздухе, так и в воде. Цемент после отвердевания сохраняет прочность длительное время.
Свойства
Физические характеристики цемента зависят от нескольких факторов.
Наиболее значимыми являются:
- виды добавок;
- степень помола;
- состав.
Тонкость помола цемента влияет на прочность и время, необходимое для затвердевания. Мелкий помол обеспечивает большую прочность и более быстрое застывание.
Чем мельче частицы порошка, тем прочнее получается бетон, тем быстрее он схватывается. От степени помола зависит и стоимость материала.
Для определения тонкости помола используют специальное сито с мельчайшими ячейками до 80 мкм. При приготовлении раствора из цемента слишком мелкого помола требуется больше воды. Устраняется этот недостаток путем смешивания частиц разного размера: крупных и мелких. Крупными считаются пылинки в 80 мкм, а мелкими – в 40 мкм.
Цементу присущи следующие свойства:
- прочность;
- коррозионная стойкость;
- морозоустойчивость;
- водопотребность;
- время схватывания (застывания).
Прочность
Этот показатель зависит от марки. Определяют прочностные свойства посредством проведения испытаний на сжатие. Опытную болванку выдерживают под нагрузкой в течение лунного месяца – 28 суток. После испытаний образца цементу присваивается соответствующее обозначение. Измеряется прочность в МПа.
Для бытового использования пригоден цемент марок 300 – 600. Для изделий, требующих особой прочности, применяются более высокие марки– 700 или даже 1000.
Коррозионная стойкость
Железобетонные изделия под воздействием воды и других жидких сред начинают коррозировать. Устраняется негативное воздействие несколькими способами. Например, можно изменить состав, ввести в порошковую смесь гидроактивные материалы. Наличие специфических веществ препятствует возникновению пагубных химических реакций.
Коррозионная стойкость увеличивается при использовании полимерных добавок. В результате микропористость снижается, повышается долговечность изделий.
Наибольшей коррозионной защитой обладает пуццолановый цемент. Поэтому он используется для строительства сооружений, эксплуатируемых в условиях повышенной влажности.
Морозоустойчивость
Одним из основных показателей качества цементы считается способность неоднократного замораживания и оттаивания бетонного изделия.
В цементном камне имеются микропоры, в которых находится вода. При замерзании вода может увеличиться в объеме на 8%.
Многократное замерзание и последующее размораживание с годами приводит к разрушению структуры камня, к появлению трещин.
В строительстве цемент без добавок не применяется. В разные марки добавляются компоненты, придающие цементу способность сопротивляться перепадам температуры.
В процессе изготовления бетона в него включаются добавки, вовлекающие воздух. Мельчайшие пузырьки воздуха распределяются равномерно внутри бетонного тела, чем решают проблему, связанную с замерзанием воды и ее расширением.
Водопотребность
Это выраженное в процентах количество воды, которое требуется для получения цементного раствора оптимальной консистенции.
В растворе номинальной густоты воды столько, сколько способен удержать в себе цемент. К примеру, в портландцементе эта величина находится в пределах 22-28 процентов.
Из цемента с низкой водопотребностью бетон получается более качественный , чем из того, у которого этот показатель высок. В первом случае изделия получаются устойчивыми к температурным перепадам. Во втором – бетон обладает повышенной пористостью и вовсе не пригоден для строительства. Такой цемент используют для производства железобетонных ограждений или дренажных сооружений.
Время схватывания
Это временной отрезок, приходящийся на изменение физических свойств цементного раствора от состояния пластичности до образования камня.
Идеальным считается раствор, застывающий не слишком быстро, но и не очень медленно. Время схватывания регулируется наличием в составе материала определенного количества гипса. Больший объем гипса обеспечивает скоростное схватывание. В то время как снижение его содержания способствует более продолжительному застыванию раствора.
Не так кардинально, как гипс, влияют на схватывание и другие факторы. В частности, значение имеет объем воды в растворе и температура окружающего воздуха в рабочей зоне.
По стандарту в нормальных условиях портландцемент начинает схватываться спустя три четверти часа. Процесс затвердевания должен закончиться через 10 часов.
Состав
Изготавливают цемент на специализированных предприятиях. Цементные заводы строят в непосредственной близости к местам добывания исходных материалов.
Сырье для его производства получают из естественных горных пород:
- ископаемых карбонатного типа;
- глинистых материалов.
Карбонаты имеют аморфную или кристаллическую структуру, от которой зависит эффективность взаимодействия материала с другими составляющими в процессе обжига.
К карбонатным породам относятся:
- мергель (мергелистый известняк);
- известняки, в том числе ракушечники;
- породы доломитового типа.
Глинистые материалы – это осадочные горные породы. Обладая минеральной основой, они наделены пластичностью, а при избыточном увлажнении способны увеличиваться в объеме. Глинистые материалы используются при сухом методе изготовления.
К глинистым породам относятся:
- глина;
- суглинки;
- сланцы на основе глины;
- лесс.
Кроме сырья, при производстве цемента используют корректирующие добавки.
Их получают из ископаемых, в состав которых входят:
- апатиты;
- глинозем;
- плавиковый шпат;
- кремнезем.
Вводимые по определенной технологии добавки улучшают качество описываемого материала.
Состав цемента зависит от требуемых характеристик, которые определяет присвоенная материалу марка.
Самый популярный портландцемент состоит из:
- 60% извести;
- 25% кремниевого диоксида;
- 10% оксидов железа и гипса;
- 5% алюминия (глинозема).
В различных марках процентное соотношение исходных материалов отличается, как и сам состав. К примеру, шлакопортландцемент имеет в своем составе шлак. Количественные пропорции могут меняться и с особенностями выбранной технологии изготовления строительного материала.
Для любых марок цемента и при любых способах его получения неизменными составляющим остаются известняк и глина. Причем известняка всегда втрое больше глины. Такое соотношение способствует получению качественного клинкера, из которого и делают цемент.
В промышленности для выпуска цемента используют следующие компоненты:
- клинкер;
- гипс;
- специальные добавки.
Клинкер – самая весомая составляющая цемента. Он определяет прочностные качества конечного материала. Клинкер вступает в процесс производства в виде гранул. Диаметр гранул варьируется в пределах 10-60 мм. Термообработка составляющей производится при температуре около полутора тысяч градусов.
Количество гипса определяется установленным периодом твердения. В базовом варианте гипс в виде порошка входит в цемент в объеме 6%.
Добавки позволяют усиливать конкретные характеристики. С их помощью цемент получает дополнительные свойства, что существенно расширяет его возможности.
Производственные этапы изготовления цемента
Сначала производится смешивание известняка с глиной в соотношении 3/1. Затем смесь подвергается обжигу при высокой температуре. В результате образуется исходный материал для получения цемента. Называется он клинкер. Гранулированный клинкер отправляют на измельчение в шаровые мельницы.
Существует три способа получения цемента.
В зависимости от технологии изготовления он может быть:
- мокрый;
- сухой;
- комбинированный.
Различия состоят в методах подготовки исходного сырья.
В соответствии с мокрой технологией используется не известь, а мел. Его смешивание с глиной и другими ингредиентами происходит с добавлением воды. В результате получается шихта влажностью от 30 до 50 процентов. Шихта преобразуется в шарики клинкера во время обжига.
По сухой технологии укорачивается процесс изготовления, так как две операции (сушка и измельчение) объединяются в одну. Получаемая шихта становится порошкообразной.
На разных предприятиях комбинированный способ используют по-разному. В одних случаях сначала получают сухую шихту, а затем увлажняют ее. В других используют не мокрый, а полусухой способ с низкой влажностью, не превышающей 18%. Обжиг выполняется в обоих случаях.
Виды
Существует немало разных вариаций цемента. Наиболее известным является портландцемент.
Довольно популярны и другие варианты материала:
- шлаковые;
- пуццолановые;
- глиноземистые;
- расширяющиеся.
Портландцемент выпускается нескольких марок: 400, 500, 550, 600. Строительные растворы делают из цемента М400.
Более высокие марки востребованы при изготовлении конструкций железобетонных, а также при создании высокопрочных бетонных изделий.
Белый портландцемент характерен тонким помолом. В состав входит маложелезистый клинкер, гипс и доломитовые добавки. Отличается высокой прочностью и устойчивостью к атмосферным осадкам. Изделия из белого портландцемента имеют эстетичный вид. Используется при изготовлении наливных полов, декоративных элементов, а также при строительстве дорог. Является основой для цветных цементов.
Портландцемент сульфатостойкий используется при изготовлении свай , опор для мостов, гидравлических сооружений, везде, где происходит многократное увлажнение и высыхание конструкций, где сооружения подвергаются замораживанию и размораживанию.
Основное предназначение шлаковых цементов – создание бетонных изделий для сооружений, расположенных под землею и под водою.
Пуццолановые цементы нужны при сооружении плотин, речных гидротехнических сооружений, различных подземных коммуникаций, так как они наделены устойчивостью к воздействию пресной воды.
Глиноземистые не боятся морских вод, поэтому они входят в состав железобетонных изделий, соприкасающихся с минерализованными водами. Могут использоваться при срочном тампонировании скважин, в том числе нефтяных; при бетонировании в зимнее время; для закрепления трещин в горных породах.
Прелесть расширяющихся цементов в том, что при схватывании они не усаживаются, а, напротив, расширяются в объеме. Увеличение объема – от 0,2 до 2 процентов.
Как сделать самостоятельно?
Приготовить цемент в домашних условиях можно, если имеется возможность достичь высокой температуры для обжига. Пожалуй, самое большее, что может получиться кустарным способом – цемент марки М 200. Потребуется мел и каолин в соотношении 3 к 1. К обожженной и измельченной субстанции нужно добавить порядка 5% гипсового порошка – и цемент готов.
Для домашнего производства потребуются соответствующие знания, подходящее сырье, специальное оборудование и точное выполнение технологического процесса.
Даже когда найдется все необходимое, вряд ли стоит заниматься производством цемента собственными силами. Прежде чем приступать к работе, ответьте себе на вопрос о целесообразности процесса. Вряд ли ваш труд и произведенные затраты окупятся. Скорее всего, выгоднее просто купить мешок готового цемента.
Выбирая цемент для тех или иных нужд, помните, что существует немало разновидностей. Правильно сделанный выбор на начальном этапе работ даст гарантию долговечности постройки. Не стоит всегда отдавать выбор более высоким и дорогим маркам. Прочность изделия от этого не повысится, а затраты не оправдаются.
Процесс получения цемента смотрите в видео ниже.