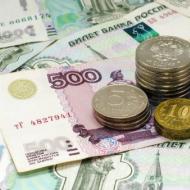
How to properly lay laminate flooring on a wooden floor. How to lay laminate flooring on a wooden floor with your own hands? How to lay laminate flooring on a wooden floor
For any decorative finishing coatings, the most optimal base is considered to be a base made of concrete, mineral screed with a strength of 15 MPa. A wood subfloor is less desirable. Some reputable manufacturers do not directly recommend installing laminate flooring on such flooring.
Permitted and prohibited bases for laminate flooring.
The reason is that wood is a very capricious material, which is influenced by seasonal, biological and other factors. The concerns of manufacturers are understandable: the geometric dimensions of the base periodically change due to changes in humidity, the planks can bend and warp. All this violates the integrity of the finish. Therefore, most often factories indicate that warranty obligations do not apply to products mounted on top of wood.
If you still plan to lay laminate flooring on a wooden floor, then the base must meet the following conditions:
- Integrity. The coating installation guidelines from reputable manufacturers indicate that the wood must be healthy, free from cracks, deterioration, loose areas, fallen areas and other similar defects. In difficult cases, it is possible to carry out a complete overhaul of the flooring and replace defective areas.
- Humidity - 8-12% (which corresponds to 40% Rh at a relative surface temperature of +20 ° C). When using the “warm floors” system, the boards should have an indicator of 5%, no more.
Do not underestimate the problem of water vapor diffusion, which leads to the formation of dampness inside the floor structure. That is why manufacturers of laminated and vinyl flooring recommend installing them on wooden structures with bottom ventilation. This arrangement of the floor “pie” will allow the wood to “breathe”, and therefore achieve a unique temperature and humidity balance. Even when using a waterproofing film and a substrate with zero vapor permeability.

Thus, it is allowed to lay laminate flooring with your own hands or by an experienced craftsman on a wooden floor, but provided that the base is of good quality or has been carefully prepared.
Preparing the base for installation
The best subfloor is considered to be stabilized old parquet or plank flooring. It is quite dense and dry, that is, it does not absorb water, is not afraid of seasonal changes in humidity and temperature, and any deformation changes are already a thing of the past. But at the same time, such a base is characterized by multiple irregularities, the presence of gaps between the planks and other defects.
Old wooden base.
Regardless of the age of the base flooring, the installer's first priority is to check the condition of the subfloors in all rooms where laminated parquet is planned to be installed. It is necessary to identify:
- Local irregularities;
- Rotten, moldy or blackened areas;
- Damaged planks;
- Areas with gaps between boards;
- Loosely attached or falling out elements;
Areas with damaged lamellas must be replaced; they cannot be covered with putty or a mixture of sawdust and PVA. Poorly fixed planks are repaired in two ways:

It is easy to close the gaps between the planks yourself using elastic wood putties or sealants. It is advisable to use colorless, non-pigmented formulations.
But you will have to tinker with the unevenness. When installing a laminate, each defect will appear in the form of a damaged section of the coating, so deep grooves and chips are filled with putty or a paste made from wood flour and PVA, which you can prepare yourself. And differences and bumps are leveled in the following ways:
Grinding
Small areas with curved slats can be treated with a plane, a hand angle grinder with an abrasive attachment, or regular sandpaper. If the surface is uneven over the entire area, then it is better to use a professional parquet sanding machine complete with a construction vacuum cleaner. All necessary units should be rented, but consumable components will have to be purchased separately.
Dry prefabricated screed
For differences of more than 5 mm, it is recommended to completely level the base using sheet materials for the floor: moisture-resistant plywood, chipboard, OSB, gypsum fiber board, etc. Slabs with a thickness of at least 16 mm are laid in 1-2 layers, along the perimeter they are rigidly pulled to the base with self-tapping screws, dowel-nails, and suitable hardware in increments of 30-40 cm. Before leveling, preventive treatment of the wooden flooring with antiseptic primers is allowed.
Dry screed is a great way to additionally insulate the floor. The most common options:
- place on the floor dense thermal insulation boards made of standard or extruded polystyrene foam (PSB-50, Penoplex Foundation), mineral wool with a density of 125 kg/m³. Sew plywood or chipboard on top of the insulation;
- form a frame from logs, lay a vapor barrier membrane, fill in the gaps or put insulating material - expanded clay, ecowool, stone wool, pine mats, etc. Place sheets of gypsum fiber board, chipboard, and SML on the slats and secure them.
Dry plywood screed over joists with insulation.
Self-leveling filling compounds
If the floor has differences of more than 10 mm? The sanding machine will remove too much layer, and the prefabricated screed is inapplicable in some cases. To minimally raise the floor level and get a perfectly flat surface, you need to use industrial bulk mixtures. Moreover, not all are suitable, namely elastic ones, on the label of which in the section “type of base” boards, plywood, chipboard are indicated.
Although many people believe that it is possible to pour the solution directly onto the wood, excess moisture can cause damage. Therefore, it is better to make a so-called floating screed on a separating layer of film or waterproofing membrane. It is recommended to lay the material over the entire surface of the floor, placing it on the walls and installing a damper tape. This will eliminate the risk of cracks. The thickness of the filling layer varies - from 20 to 70 mm.
Instead of film, you can use waterproofing compounds for wood: polymer primers, water repellents, etc. That is, any liquid product that is absorbed into wood without leaving an oil, bitumen or other film on the surface.
The procedure for working with bulk mixtures is described in detail in the instructions on the packaging of the material. The composition is mixed with water, thoroughly mixed until smooth, carefully distributed over the floor and rolled with a roller or brush to remove air bubbles. After 5-7 days, the base for the laminate is ready.
Laying technology
Our step-by-step instructions will help you cope with the last stage and avoid mistakes when installing the finishing coating.
For work you will need the following tools and materials:
- Laminate of suitable design with a margin of 1-4 m². Decide in advance whether to lay the covering along the walls or diagonally. In the first case, a reserve of 1-1.5 m² is sufficient, in the second, at least 3 m² will be required;
- Coniferous substrate, made of foamed polyethylene, cork, extruded polystyrene foam with a cross-section of up to 3 mm;
- Waterproofing film 150-300 microns or membrane, tape for fixing layers;
- Hydraulic level;
- Cutting hand or power tools for adjusting the lamellas to size;
- Kit for laying laminate flooring, including spacer wedges to create a temperature gap around the perimeter 8-10 mm wide, mounting bracket and tamping block made of wood or PVC;
- Square, pencil and tape measure.
Installation of the laminated coating is carried out in 5 steps:
Checking conditions
Can I start styling immediately after purchase? No. First, check all the packs to ensure they are from the same batch or identical year of manufacture. Otherwise, there may be a difference in tone, a mismatch in the decor or even the locking part. This is especially common when purchasing finishing materials on sale. You can, of course, return or exchange the product within 2 weeks from the date of purchase, but do not forget the receipt or invoice.
The optimal period for acclimatization of the floor covering.
Check the climate conditions. They must comply with the requirements of the instructions:
- Air temperature – from +16 to +25 ºС;
- Relative humidity - 40-70%;
- “Warm floors” - switched off 5-7 days before the start of work, in winter 3 days;
- The normal moisture content in flooring boards is 8-12%, if there is a heating system - no more than 5%.
The laminate must be brought in and, without unpacking, left in the room for 2 days.
Preparing the base
As noted above, the surface must be dry, smooth, solid and clean. Even the slightest defects must be eliminated in advance so that you do not have to disassemble the laminate or repair it later.
Laying waterproofing and underlayment
It is necessary to lay strips of film or membrane on the base with an overlap of 10-20 cm. It is recommended to glue the joints with tape. Then the substrate is laid end-to-end, the slabs or layers are secured to each other using adhesive tape.
Among the fairly wide variety of decorative floor coverings, there are not many options that can be laid on a wood base. Although, with strict adherence to the necessary rules, almost any material can be laid. But a laminated coating, created according to the floating principle, is an ideal solution for a wooden base. In this article we will talk about how to install laminate flooring on a wooden floor, as well as what options there are for laying laminate flooring.
How to lay laminate flooring on a wooden floor?
Laminated panels are only fastened to each other; there is no need to fasten them to static building frames, to the floor or wall. A floor created using the floating method sits comfortably on a sub-base and gives it the opportunity to expand and contract. The base also does not interfere with the laminate when it changes its geometry due to changes in temperature and humidity levels. The design features of laminated panels make it possible to do without adhesive. The glueless method is the most popular. It pleases both the wooden base and the owners of country houses with excellent spontaneous aeration, which is necessary for ventilation of parts of the wooden structure.
Despite its artificial composition, laminate does not differ much from timber during operation. Because its main part consists of MDF panels, chipboard, HDF and the same boards made by pressing wood processing waste. The basis of laminated panels is an important indicator that determines the scope of application.
When installing any high-quality laminate on a wooden base, it is worth considering certain features of this material:
- a material that is made of wood will lose its quality after some time, for this reason, before installing the laminate, carefully inspect the floor, as well as the condition of the supporting beams and joists
- timber is not highly resistant and stable, therefore, even a slight displacement of the panels will cause an increased load on the interlocking joints
- Old wood flooring often has an uneven surface, bumps or depressions. Before installing the laminate, it is necessary to get rid of all defects so that the panels do not separate or cracks form.
Before laying laminate flooring on a wooden floor, you need to level the surface. There are several ways to level a wooden surface:
- using sheets of plywood or particleboard (chipboard). To do this, you need to take a thick sheet of plywood and treat it with an antiseptic solution to prevent the proliferation of microorganisms. Next, adjust its size using a special saw, after which you can lay them on the base. Backing slats will help level the slope of the base, and self-tapping screws will secure the sheets
- scraping. This method is suitable for old floors that have minor flaws. Provided that the base imperfections range from 4 to 6 mm per square meter. meter, you need to conditionally divide the coating into several parts. Each of the resulting parts must be processed with an electric planer.
- installation of support beams or joists. When the base has a significant slope or creaks strongly, you need to fit and attach special slats made of timber, called joists, to the concrete base.
In addition, if a rotten board is discovered, it must be replaced. Secure loose boards using self-tapping screws. When the logs wobble, they need to be strengthened at the base. For this purpose, drill a hole and secure the logs using an anchor. When the foundation subsides, special support wedges must be placed under the joists. Any cracks and crevices, even the smallest ones, should be sealed with putty.
Upon completion of all repair work, you need to thoroughly clean the base from dirt and debris, then you can implement the second stage of installing the laminate.
Do-it-yourself laminate installation on a wooden floor
On the leveled and repaired base, you first need to lay a 3 mm thick foamed polypropylene or balsa wood backing. The backing sheets are placed end to end and connected to each other using wide tape or construction adhesive tape.
Laminate panels are laid from the window towards the door. Thus, the joints between the laminate plates will be the least noticeable. The first row is placed at a distance of 1 cm from the wall. To maintain this distance, you need to insert a wedge between the panel and the wall. This gap is called temperature; it is needed to compensate for the linear expansion of the coating.
The second panel is mounted in the end lock at an angle of 25 degrees. It's rare to not trim the last panel in a row. Most often the rooms are so large that they need to be cut off. The second row begins with this piece.
Upon completion of the installation of the second row, it is worth carrying out the operation of minimizing the joints. To do this, you need to tap the panels with a hammer through a wooden stand. This is done until the joint is reduced in size. Then you can move on to the third row.
When the entire laminate has been laid, you can begin installing the skirting boards, which serve as an additional fixation for the panels and give the finished appearance to the decorative coating.
There are certain types of laminate flooring. Having made your choice, you need to make calculations in order to go to the store for a certain number of panels. To choose the direction of installation, you need to make sure that the pattern and texture of the panels are compatible with the lighting of the rooms and their shape. Today, modern materials make it possible to lay decorative coating along the line of sunlight, across it, as well as to perform herringbone installation. However, the latter option is not applicable to all laminate models.
Conventional panels are not suitable for herringbone installation. The panel must contain special locks that allow you to lay the laminate in a herringbone pattern or squares. For example, the collection of Quick Step Noblesse panels contains materials of small size, with a specific locking connection, which makes it possible to interlock the panels at an angle of 90 degrees. The panels of the quick step collection are laid along the line of natural light, as well as against it. When installing panels against the flow of light, you can visually enlarge a small room, but the joints will be visible.
When window openings are located on one wall of the room, experts advise using the direct option of laying panels in the direction of the sun's rays, because when installed across, the joints of the panels will be obvious and spoil the entire appearance. Laying across the light is carried out when the room is narrow. With this arrangement of laminated panels, the room visually expands and gives more volume. This option is very suitable for corridors or other long rooms. The essence of direct installation is that the panels are laid parallel to the wall, starting from the doorway. Trimming costs are minimal - only 5-7%, which significantly saves the amount of raw materials.
Diagonal installation is the most difficult and costly. Pruning costs are about 17%. This option is implemented at an angle of 45 degrees. There are two types of installation, from the corner of the room and from the middle. The second option is the lowest waste and simpler. Due to the unusual and neat installation, the room visually expands. Diagonal laying is used with an open view of the floor, when there are no carpets and the room is not cluttered with furniture.
Today, beveled laminate is gaining popularity. This option belongs to a special series of laminated materials. The chamfered panels lying on the floor look like a plank floor created from a single board. This laminate is produced at an angle, creating a beveled plane of the board throughout its thickness. The structural element is created along the entire perimeter or on two opposite edges.
There are two types of chamfers:
- V-shaped
- U-shaped.
In the process of joining two panels, an almost imperceptible groove is formed, which resembles laid elite parquet or solid wood. These recesses are not felt to the touch, so dust will not accumulate in them. And the ends of the material are most often impregnated with wax, so no liquid will penetrate inside. The recesses make it possible to hide minor flaws. According to experts, these recesses do not allow the material to “walk,” which provides a tremendous advantage compared to standard series. Now you know how to lay laminate flooring with your own hands.
In the rather extensive list of floor coverings, there are not too many options that are compatible with a wood base. True, if you follow special rules, you can lay almost anything. But a laminated floor, constructed using the floating principle, is ideal for furnishing a house built over a structure made of beams, joists, and boards. However, compatibility does not save independent craftsmen from studying the nuances according to which laminate flooring is laid on a wooden floor, and from the need to remember the specifics of ever-moving wood.
Can laminate flooring be installed on wood floors?
Laminated panels are bonded only to each other; there is no need to attach them to static building structures, that is, to the floor or walls. Built using a floating design, the floor rests freely on the sub-base, allowing it to expand and contract. And it, in turn, does not prevent the laminate from changing its geometric parameters following temperature changes and humidity fluctuations.
The design specificity of laminated boards makes it possible to do without adhesives that hermetically seal the butt seams. Although adhesive technology exists, it is used extremely rarely due to labor intensity, significant consumption of glue and the inability to disassemble and reassemble permanently joined panels in another place. Glueless, the most popular fastening method, pleases both the wooden base and the owners of country property with excellent spontaneous aeration necessary for ventilation of the components of the wooden structure. An excellently ventilated floor covered with laminate through the seams lasts longer and does not rot.
Despite the artificial origin of the laminated coating, its behavior during operation is not much different from the behavior of lumber. After all, its main element is made of MDF panels, chipboard, HDF and similar boards created by pressing wood products. The base of a laminate floor is an important characteristic that determines the scope of use of the material. In theory, laminate flooring is not recommended for installation in rooms where wet cleaning must be carried out regularly. It is allowed to arrange bedrooms, children's rooms, offices, and living rooms. However, flooring made with HDF is considered moisture resistant and can be laid on floors in hallways and even kitchens.
Note. For flooring in rooms with typical wet conditions, a laminated floor of class 33 on the wear resistance scale is suitable, but its cost rarely suits the owners of country houses.
Rules for preparing a wooden base for installation
There are general requirements for the characteristics of the surface being developed. According to the instructions of SNiP with the number 3.04.01-87 assigned to the normative collection, for laying laminated coverings:
- a leveled surface is required, the differences in relief of which do not exceed 2 mm within an area of 2 m²;
- allow a maximum slope of 4mm, evenly distributed over 2m in any direction.
You should not deviate from the instructions regulated by technical regulations, since failure to comply will damage the sensitive locking system. The grooves will become loose, the fragile thin ridges will break, the floor will not last long and will have to be re-laid.
You can, of course, partially change the elements if only a few boards are damaged, but the repair procedure will require a lot of effort. In such situations, the laminated panels are dismantled to the restoration site, then the broken elements are replaced and laid again in the reverse order. If the laminated planks are damaged multiple times, partial replacement is out of the question. At best, a few boards will be preserved, which can be used to arrange storage rooms, closets, and compact covered verandas.
Before laying laminate panels on a wooden subfloor, it is mandatory to inspect the base. The scope of work is determined, as a result of which the base, brought into full order, will be ready to install the covering on its reinforced “shoulders”.
Preparation actions depend on the degree of wear of the wooden structure:
- Old plank floor will have to be disassembled down to the support beam, because over the years of its long-term operation, sensitive natural organic matter could suffer from excess moisture or become infected with fungus. It is impossible to find out through the floorboards what the real condition is if the wooden floor is not the ceiling of a spacious basement. Those with a high underground are lucky. It will provide an opportunity to examine and repair ceiling parts without tedious dismantling. We carefully examine the entire list of structural elements. We cut out doubtful sections of beams and joists and replace them with new timber. The boards removed from the floor with a low subfloor, which inspire confidence in their reliability, are turned over with the unworn inside out, laid again, and the cracks filled with foam or repair compound. We replace old, worn-out boards without regret. We will “go through” the floorboards secured in the bottom using a scraping machine. All structural components of a long-established wooden floor must be carefully treated with antiseptic impregnation and fire retardant. Nowadays it is easy to buy a mastic that performs both functions that are significant for wood.
- New plank floor There is also no need to scrupulously diagnose it, since it was built not so long ago and is probably covered with compounds that protect against putrefactive bacteria and fire. Therefore, preparing to lay laminate flooring on a newly constructed wooden floor will not take much time and labor effort from the contractor. We check the fasteners, change or repair loose fasteners, “sink” nails or screws a couple of mm into the floorboards. We foam or fill the cracks with wood glue, mixed in half with sawdust, and scrape if necessary.
- Floor with structural defects needs to be improved. It is very difficult to determine in advance the range of actions in such cases, because the situation can have a lot of different reasons. For example, if the floorboards sag, the joist system will need to be strengthened by additionally installing timber or replacing the boards with thicker material. It is often more profitable and easier to lay another row of boards of similar thickness on top, laid “cross” to the previous layer. The latter measure is acceptable if the additional subfloor, together with the laminate and underlay, does not take away too many cm, which are very necessary for a limited space, from the ceiling height.
You can level the rough wood base with plywood, GVLV, OSB sheets or by placing pieces of roofing felt under the joists, as well as glassine rolled into several layers. You can purchase a “constructor set” from Knauf with a full set of fasteners, supports and plywood sheets. The method is chosen based on economic considerations and ease of implementation.
Laying technology for laminated boards
We invite you to watch the thematic video:
It is impossible to cover the wooden rough base with vapor or waterproofing, it will interfere with ventilation. Condensation harmful to wood will accumulate under the insulation. But if nothing can break the burning desire to isolate, it is better to use a diffusion membrane.
Before laying, you will only need to lay the underlay; it is advisable to choose a natural material for this. For the sake of the safety of the wooden structure, it is worth forgetting about the high prices for cork and the bitumen-cork or bitumen-rubber pressed options created with its use. The thickness of this layer is selected based on the same parameter of the laminated panel. Typically, strips of 3mm underlay without overlaps are placed under an 8mm laminate. No permanent fastenings to the walls or to the base are needed, only gluing with tape in periodic dots or solid lines.
Note. The choice of direction for laying out laminated boards is influenced not so much by the preferences of the owners as by the direction of the existing floorboards. Laminate panels should lie across the boards. This means that the strips of substrate located under the coating need to be laid lengthwise.
Let’s assume that it has already been decided how we will lay the laminate panels, an elementary plan has been drawn out by hand in advance and a rational scheme has been selected. There is plenty of information about methods, rules and layout options on the website. Here are a couple of articles on the topic:
You can join the boards by gradually increasing the coverage of each piece separately or by joining pre-assembled rows. The preferred method is usually specified by the material manufacturer, and we examine the individual algorithm.
Actions of the installer when assembling a laminate floor piece by piece:
- Let's position ourselves in the starting corner, usually the corner farthest from the doorway, taking 4 panels with us. For two of them (1st and 3rd), planned for installation against the wall, you must first cut off the ridge. We do not touch the groove; it is always directed towards the stacker.
- Let us first outline the distance by which we will move the panels in adjacent rows in order to avoid cross intersections and thereby increase the reliability of the connections. The recommended offset for the offset is no less than 30 cm. We will shorten the second board by this amount.
- Using the method specified by the manufacturer, depending on the type of Click or Lock locking system, we join the 1st and 3rd panels, then attach a piece of the 2nd board to them, then the 4th uncut board.
- We move the assembled floor segment to the designated location, installing spacers approximately 1 cm thick between it and the adjacent walls. They will provide the clearance required for the laminate to move during thermal expansion.
- We extend the first row with the 5th board with a cut ridge, then extend the second strip of covering with the 6th.
- By analogy, we follow until the successful completion of laying the first two rows, not forgetting to cut off the ridge facing the wall. We cut the boards that complete both strips according to precisely measured distances. To snap the last ones into the rows of elements, we use a special mounting bracket.
- Next, we follow the course we have learned, only there is no need to trim the ridges anymore.
- We measure the panels of the last row at the place of installation and cut them taking into account the temperature indentation, attach them and snap them into place using a clamp.
Methods of bypassing pipes, methods of laying under radiators and arranging doorways correspond to standard rules for covering laminate floors.
Important point. In a large room, the temperature gap should be left not only along the walls. It is formed every 10 m, measured in width, and 8 m in length. The expansion joint is left in the opening along the axis of the closed door leaf. The gap after installation is closed with a profile made of plastic or aluminum.
Absolutely simple rules that explain how to economically lay a laminated flooring with your own hands will help you perfectly decorate your countryside and city property. And for those who did not intend to do the construction themselves, knowledge of the technology will help them competently monitor the actions of builders who are not always diligent.
Laminate is one of the most popular floor coverings today. It is used in both residential and commercial establishments. Laying laminate flooring on a wooden floor is done when it is necessary to hide the defects of the old plank covering, as well as when you want to simply update the interior.
According to experts, it is better to completely dismantle the old wooden floor, after which, to level the rough base, apply a concrete screed under the laminate. But since this process will require additional costs that may exceed the cost of the laminate, it is possible to lay the product directly on a wooden base, as well as using plywood or OSB as a substrate. Let's look at the first and second methods of installing laminate flooring on a wooden floor with all the details.
Tools and materials for working with flooring
1. Drill, jigsaw and screwdriver. Power tools allow you to increase the speed of installation, facilitating manual labor. 2. Hammer and mallet. Laying laminate flooring on a wooden floor simply cannot be done without them: hammer in the nails, knock down the laminate, tap the boards. 3. Level and roulette. 4. Fiberboard or plywood. Used to level floors.5. Nails or screws. Necessary for attaching a wooden “screed”. 6. Underlay for laminate. Purchased depending on the room.
Getting ready to lay laminate flooring
Before laying laminate flooring, you need to remember that the material must be left for some time in the room where it is intended to be used. This is done so that it adapts to the humidity characteristics of the room and does not warp later. This is especially important if you are planning to lay laminate flooring on a wooden floor. The fact is that wood is a rather capricious material. Indoors, the laminate is left sealed for approximately 48 hours. According to experts, it is best to place it in the middle of the room. The room where the laminate is “maintained” must have a temperature of at least 18 degrees and a humidity of no more than 75%.The feasibility of laying laminate flooring on a wooden floor
The answer to the question whether it is possible to lay laminate flooring on a wooden floor most often depends on the strength of the base. Most consumers who prefer laminate-based floor finishing doubt the possibility of installing slats on wooden floors and are thinking about dismantling the wooden covering. Of course, removing a wooden base takes a lot of time, and besides, this work is not only labor-intensive, but also dirty. However, it should be remembered that in some cases dismantling cannot be avoided. Thus, laying slats on wooden floors that are rotting or affected by fungi is unacceptable. Covering the damaged surface will not be able to stop the process of wood rotting, and after some time the laminate will also be affected by rotting.An alternative to expensive dismantling work can be local replacement of the areas most affected by rotting, followed by the use of waterproofing materials. In this case, it is advisable to use moisture-resistant plywood sheets as a substrate.
Assessing the condition of a wooden floor
Laminated panels can be laid on wood floors only after a full range of measures has been taken to properly prepare the surface. Wood is a good base for laminate, but its condition must be suitable for the finishing work. Often, before installing laminate flooring, it is necessary to repair the wooden base. The most common defects are creaking floors as a result of drying out and surface deformation. In addition, repair work may be required if it is necessary to strengthen loose wooden floorboards of the base. Sometimes you have to use additional fasteners. You can identify the main irregularities using a building level. This method will allow you to correctly assess the volume of activities to level the base.Features of a wooden floor
The base for the laminate must be smooth, strong and rigid. These conditions must be observed so that the locking system is not damaged during operation. For example, if we lay laminate flooring on a wooden floor without preliminary preparation, this is not recommended, since the plank covering may have significant differences in height, individual boards may sag, which is considered unacceptable. Owners of apartments or houses where the old floor is made of wood often have a question about how to lay laminate flooring on a wooden floor and whether it can be done. It is possible to lay laminate flooring on such a base, the main thing is to carry out the correct preparatory work. Wooden bases are found quite often in rooms for various purposes. To prepare it for subsequent use, it is necessary to study it and, if there are any defects, eliminate them.The first thing to remember is that wood is an unstable material; it is characterized by processes such as drying out and desiccation. During such movement, gaps may form between the boards, which will increase the load on the laminate locking system. Second: it is necessary to examine not only the surface of the wooden floor, but also its structure - beams, joists. If any defects are found, they must be eliminated, as they can further harm the floor covering. Next, we will consider the main methods of preparing a wooden base, since the preparatory processes are the main ones in the work. If you simply throw them away, then the whole arrangement will come to naught.
Preparing a wooden base for laying laminate flooring without plywood
In order to lay laminate directly on a wooden floor, you must ensure that the surface is in satisfactory condition:Sometimes it is necessary to repair and strengthen the logs themselves, which “walk” under load - for this, beams or bricks are installed under the logs. Floorboards can creak due to friction against each other. To eliminate the grinding between them, graphite or talc is poured into the gap. Existing gaps are filled with putty. Next, to fully ensure that the wood is in good condition, you need to remove the old layer of paint with your own hands. The appearance of the tree should be close to the natural shade throughout the entire plane. If in some places on the floor the boards look dubious, it is recommended to test them for strength with an awl. The second way to identify rotten or rotten floorboards is to tapping the floor surface with a hammer. In this case, tapping on intact healthy wood will be heard loudly and clearly. While the muffled sound will be a serious reason for replacing old wooden elements with new ones. Even though rotten boards are still strong, you still need to replace them yourself, as the rot can spread to healthy parts over time. Treatment with an antiseptic composition and waterproofing of the wooden base will prevent their occurrence in the future. If grooves in the form of grooves are found on the floorboards, it is necessary to apply a bioprotective composition to the wood flooring, since their presence indicates contamination of the material with wood borers. An uneven wooden floor must be leveled; differences in its surface can be 1.5-2 mm/1m2. The way to determine how uneven the flooring is is to use a building level. In the absence of the specified measuring device, you can use a two-meter bar and a spirit level. If the height difference is not critical, an uneven floor can be leveled using a grinding machine, or with your own hands using a plane. The second method is too long scraping technology copes with the task at hand faster and more efficiently. The main thing is that before leveling the floor for subsequent laying of the laminate, do not forget to recess the heads of the nails located above the surface deeper, which can cause the grinding equipment to fail. If your old wood floor is too uneven and sanding cannot solve the leveling problem, there is another way to make it as level as possible - by pouring. Pouring a wooden base for laying laminate is done by using a self-leveling screed, but not a self-leveling mixture, which is not used for wood. To level a wooden floor, compounds with fiberglass are used, due to which the materials firmly adhere to each other. Unlike standard solutions, fiberglass mixture is thicker and hardens faster. But before pouring, waterproofing in the form of a dense polyethylene film is laid on the wooden base. Waterproofing is arranged along the floor in such a way that its edges can be fixed to the walls around the perimeter of the room. The pieces of film are laid overlapping each other, with an allowance of 15-20 cm, the joints are glued with construction tape.
Leveling a wooden floor with plywood under laminate
The technology of leveling a wooden floor using plywood or OSB is a low-cost, but at the same time, effective way to make the base base ideal for laying laminate flooring. To find out which substrate will be better for laminate - OSB or plywood, it is necessary to compare the technical characteristics of both products. Sheets of plywood and OSB boards are materials of similar quality: the products are easy to process, have a durable structure and relatively high moisture resistance. At the same time, OSB boards are cheaper than plywood, but the appearance of the products does not allow them to be used for the construction of a finished floor.Despite this, OSB is slowly displacing plywood products from the construction market, because the behavior of plywood during operation is difficult to guess, which cannot be said about OSB boards, which do not have the property of delaminating under atmospheric and mechanical influence. In addition, the modulus of elasticity during bending, compression and tension of OSB boards is an order of magnitude higher than that of plywood. Based on the above, we can conclude that OSB boards are the most suitable products that will not only level an uneven floor, but also extend its service life.
Rules for laying OSB boards on a wooden base
Basic rules for laying OSB boards on a wooden floor: as a substrate for laminate, it is necessary to use materials with certain parameters. For example, for a laminate with a thickness of 7 mm, you should not buy slabs more than 2 mm thick; for a thicker finish coating of 8-9 mm, the optimal substrate thickness is 3 mm. A thicker backing will sag slightly when pressed, causing the laminate's interlocking joints to become deformed. Installation of OSB boards on a wooden base is carried out by screwing them with screws or nailing them with rods of a certain length. The distance between fasteners is calculated by multiplying the existing slab thickness by 2.5. It is necessary to leave 5 mm technological gaps between the plates, which are subsequently filled with polyurethane foam. It is mandatory to install waterproofing under the substrate to prevent the formation of condensation that destroys the structure of the wood. The uneven transition at the junction of the plates is leveled with epoxy putty.Choosing a substrate for laminate
There are several types of materials used for laying laminate flooring. Cork backing- valued for its composition: it consists exclusively of natural materials, no chemical components. Does not rot, does not spread mold. Does not deform and retains its original appearance throughout its entire service life. Bitumen substrate- when laying laminate flooring on wooden floors in an apartment, you can also use thick paper in combination with bitumen: this material protects the laminate from moisture and is perfect for uneven floors.Installing laminate flooring on a wooden floor
Here we come to the most important point, which requires attention and composure: every action will affect the final result, so be careful and strictly follow all the instructions described below. Installing laminate flooring on a wooden floor with your own hands can be done in several ways:click system
The work process begins from any corner opposite the entrance door: along the entire perimeter, along the walls, wedges (pieces of plywood) 1 cm thick are installed. This is necessary to create a wall gap so that the laminate can freely expand and contract later. 1. The very first panel is placed in a corner and pressed against the installed wedges. 2. We continue the row with the second panel, which joins the first at an angle of 20-30 degrees: pressing the ends tightly, using gentle pressure, click the lock and lower the laminate board.3. We lay out the row until we hit the wall/door. The last panel is trimmed to fit the remaining gap. 4. The next row begins with the cut piece, this is how the checkerboard effect is created. 5. Along the length, the laminate is also snapped into an acute 30-degree angle.
Lock system
This method will answer the question of how to lay laminate flooring vertically and diagonally on a wooden floor. 1. The work process begins from the corner opposite the door. 2. The second panel is brought horizontally to the first panel (to the short end), inserted into the groove and hammered with a mallet. 3. Along the long end we match the already pre-assembled row to the existing panels.4. Try to use a mallet or hammer with blocks, this reduces the risk of damaging the laminate.
Glued laminate
Another way that can answer the question of how to lay the flooring yourself, without special tools and skills. There are no special notes on installation with glue, but there are some points that are worth knowing in advance. The adhesive at the joints of the panels best isolates the base of the laminate from moisture, thereby extending the service life of the floor covering.Before you can walk on such a floor, you must wait 10-12 hours at room temperature, without creating drafts. It is no longer possible to reuse such a surface: during dismantling, most of the panels will be damaged.
Maintenance and care of laminate flooring
1. Avoid getting excessive moisture at the joints of the panels. 2. Place something soft under the sharp corners of the legs of sofas and other interior items. 3. Monitor the humidity in the room: with sudden changes in temperature and increased dryness, the laminate may come apart, cracks will form, which will be problematic to eliminate, and you will have to disassemble the floor.Technology for laying laminate flooring on wooden floors
The simplicity of laying the material allows you to install lamellas on almost any base, including wood. To perform installation as efficiently as possible, it is very important to know the basics of technology, which reveals the secret of how to install it with your own hands quickly and correctly.
The feasibility of laying laminate flooring on a wooden floor
The answer to the question whether it is possible, most often depends on the strength of the base. Most consumers who prefer laminate-based floor finishing doubt the possibility of installation and think about dismantling the wooden covering.
Of course, removing a wooden base takes a lot of time, and besides, this work is not only labor-intensive, but also dirty. However, it should be remembered that in some cases dismantling cannot be avoided. Thus, laying slats on wooden floors that are rotting or affected by fungi is unacceptable. Covering the damaged surface will not be able to stop the process of wood rotting, and after some time the laminate will also be affected by rotting.
An alternative to expensive dismantling work can be local replacement of the areas most affected by rotting, followed by the use of waterproofing materials. In this case, it is advisable to use moisture-resistant plywood sheets as a substrate.
Also read materials:
Preparing a wooden floor for laying laminate
The wooden base must be correctly visually assessed, which will allow us to develop a plan for its high-quality preparation for the installation of lamellas.
Condition assessment
Laminated panels can be laid on wood floors only after a full range of measures has been taken to properly prepare the surface. Wood is a good base for laminate, but its condition must be suitable for the finishing work.
Often, before installing laminate flooring, it is necessary to repair the wooden base. The most common defects are creaking floors as a result of drying out and surface deformation. In addition, repair work may be required if it is necessary to strengthen loose wooden floorboards of the base. Sometimes you have to use additional fasteners. You can identify the main irregularities using a building level. This method will allow you to correctly assess the volume of activities to level the base.
Leveling technology
Minor unevenness in depth can be eliminated with a plane or grinder. Significantly protruding and very loose floorboards should be strengthened using self-tapping screws, but not nails, which will prevent the process of loosening and creaking of the base. More significant differences are eliminated using sheet plywood. It should be remembered that differences in height of one centimeter for every three meters of area are practically unnoticeable.
For local or complete replacement of wooden coverings, only high-quality and dry wood should be used, which will help protect the surface from deformation and curvature. It is advisable to cover the wooden base with sheet plywood or chipboards. If the surface is relatively flat, it is possible to cover it with a standard, but thick and sufficiently durable substrate.
Repair work
Repair of a wooden base is necessary if it has significant damage or is already too old and dilapidated. The wood chosen to replace removed floorboards should be kept indoors for several days.
Differences in height of more than five millimeters are eliminated with the help of additional plywood pads, the use of which can replace labor-intensive work on arranging a concrete screed. A gap of one centimeter should be maintained between the sheets of substrate.
Preparing woodHow to lay laminate flooring (video)
The most expensive repair work involves the dismantling of all floorboards and full or partial replacement of the joists.
Installation features
The quality and service life of the laminate floor finish will ultimately depend on how correctly the substrate material and its thickness are selected.
Selecting a substrate
Typical problems that accompany the use of low-quality underlayment are the appearance of divergent seams, breakage of locking joints, the appearance of unevenness and “walking” laminated planks.
There are several types that are used when laying coatings on wooden floors.
- Bitumen substrate is a moisture-resistant base. This is the best option for insufficiently level foundations in rooms with high humidity levels.
- It is the most expensive version of the material and has high performance qualities. It is characterized by resistance to deformation changes, fungal and mold damage.
- Substrate based on polyurethane foam presented in several versions, differing in thickness and density. This is the most budget option. It is recommended to purchase a thicker substrate with increased rigidity or lay a double layer of material.
Using a substrate
A high-quality laminated substrate should be purchased with a slight excess in quantity or volume. This rule is due to an increase in material consumption as a result of the need to trim the substrate due to the configuration features of the room being finished.
It is very important to remember the main rule: for a higher-quality base, you can use a less expensive substrate.
Installing laminate flooring on a wooden base
Currently, two methods are most in demand, according to which the lamellas are placed on the floor surface.
- Direct laying involves the arrangement of lamellas in a direction parallel to the light incident from the window or perpendicular to the window opening. This option helps to level the joints, but may require an increase in the consumption of laminated planks by five percent.
- Diagonal laying involves arranging the lamellas while maintaining an angle to the wall of thirty-five degrees. Material consumption may increase by 15%. This option helps to visually enlarge the space and is more suitable for small rooms.
Laminates with the “Click” system
The newest and easiest to install version of the locking system. Laying is carried out starting from the far corner with the installation of spacer wedges in increments of one centimeter. The joining of the planks is done by attaching the end of the second element at an angle of twenty-five degrees to the first, then the panels must be snapped into place by lightly pressing the element to be attached.
Laminates with the “Lock” system
Laying should begin from the corner farthest from the doorway. The laminate strips are joined horizontally with grooves aligned, which can be lightly tapped with a special rubber mallet. Tapping the lamellas should be done carefully, but until complete fixation is achieved.
Glued laminates
Glued laminates have recently lost much of their former popularity. The installation process of such finishing material for floors is the most labor-intensive, which is due to the need to treat the end parts of the planks with an adhesive composition and then connect all the elements together. Poor quality processing of the end parts makes the connection less durable and unstable to moisture. Dismantling the coating will lead to the complete destruction of all elements, which will make them unsuitable for reuse.
Laying laminate flooring on a wooden floor (video)
Even a very high-quality laminated flooring laid in accordance with all rules will not last long if the requirements for operation and maintenance are not followed. It is very important not only to maintain the humidity and temperature in the room, but also to protect the laminate from traumatic factors, as well as to carry out timely and proper cleaning of such flooring.