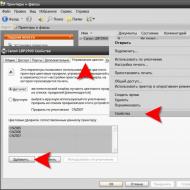
Optymalne cięcie blachy online. Programy do cięcia płyt wiórowych
Wykres rozkroju - to dokumentacja pokazująca, jakie elementy należy wyciąć z płyty wiórowej. Ale tak naprawdę można ciąć nie tylko płyty wiórowe, ale także dowolny materiał arkuszowy.
Za pomocą zagnieżdżania możesz zobaczyć, jak możesz ułożyć części na arkuszu. Na mapie znajdują się także informacje o pozostałościach, które powstaną w wyniku rozbioru.
W ostatecznym rozrachunku zaletą cięcia jest ukazanie ilości materiału, który będzie potrzebny do stworzenia mebla.
Płyty wiórowe można również ciąć w firmie, w której kupisz materiały, jednak naszym zadaniem jest stworzenie mebli skrzyniowych w domu przy minimalizacji kosztów, a wykonanie ich samodzielnie, nawet dla początkującego, nie będzie trudne.
Do stworzenia mapy posłużymy się programem Cutting 2 (cięcie). Możesz pobrać go bezpłatnie na koniec lekcji.
Interfejs programu wygląda następująco:
W polu „Materiały” należy podać parametry arkusza płyty wiórowej lub jeżeli posiadasz resztki, które planujesz wyciąć, to wielkość resztek. Jeśli chodzi o rozmiar płyty wiórowej, używam arkuszy producenta Swisspan, których wymiary wynoszą 2750 * 1830 mm (dla dużych arkuszy) i 2440 * 1830 mm (dla małych).
Należy również pamiętać, że w ustawieniach arkusza płyty wiórowej należy ustawić wartości „Cięcia arkusza”, ponieważ arkusze początkowo mają wióry.
Jeśli planujesz skleić obrzeże PCV lub chcesz obliczyć ile krawędzi papieru potrzeba do sklejenia, możesz to również ustawić w "Właściwościach".
Cześć przyjaciele.
W tym artykule porozmawiamy o jednej praktycznej stronie tworzenia mebli.
Po zaprojektowaniu dowolnego mebla otrzymujesz jego detale, czyli listę wszystkich części niezbędnych do jego montażu.
Kolejnym krokiem będzie zakup arkuszy płyt wiórowych i pocięcie ich na te właśnie zaprojektowane części.
Tutaj możesz mieć dwie opcje:
Albo zaniesiesz swoje detale tam, gdzie będziesz mieć płytę wiórową (i to w zasadzie to samo miejsce, w którym ją kupisz), a oni zrobią to za ciebie według twoich detali, potną arkusze materiału na niezbędne części.
Lub początkowo stworzysz schemat, zgodnie z którym materiał arkuszowy będzie przetwarzany.
Karty do cięcia - i istnieje schemat cięcia arkusza (na przykład tej samej płyty wiórowej) na niezbędne części.
Każda taka mapa zawsze pokazuje obecność pozostałości użytego materiału.
Te same części można ułożyć na arkuszu, aby w jednym przypadku rozmiar pozostałości był duży, a w drugim mniejszy.
Oczywiście zawsze potrzebne są duże resztki, ponieważ nadal można coś zrobić.
Dlatego w przypadku, gdy ktoś wykona za Ciebie tę dokumentację, wielkość twoich sald zależy tylko od niego.
A jeśli robisz to sam, to układasz części w taki sposób, aby uzyskać jak najwięcej resztek.
Oczywiście nikt nie robi tego ręcznie, gdyż jest to bardzo pracochłonne.
Do tych celów od dawna wymyślono bardzo dobre programy.
Rozważymy jednak prostszą opcję: jeden oryginalny arkusz płyty wiórowej i detale do niego.
Przed obliczeniem szczegółów w oryginalnym arkuszu możesz ustawić cięcie wzdłuż końców (w tym przypadku 7 milimetrów każdy).
Następnie, klikając ikonę „Kalkulator”, program automatycznie uporządkuje szczegóły zgodnie z określonym arkuszem.
Jak widać na rysunku, nawet jeśli niektóre detale nie zmieściły się w arkuszu, można je zobaczyć w oknie poniżej.
W tym oknie położenie dowolnych części można zmienić według własnego uznania, obrócić je wokół osi (o ile oczywiście we właściwościach określonych w ustawieniach części funkcja ta nie jest zablokowana). Jednym słowem zrobić wszystko, aby uzyskać jak największe salda.
Po ułożeniu szczegółów zgodnie z potrzebami możesz kliknąć widok tego arkusza.
W tym trybie pokazany jest układ wszystkich części, całkowita długość cięcia, powierzchnie części i pozostałości, jednym słowem wszystkie niezbędne informacje.
Następnie, klikając odpowiednią ikonę, wszystkie arkusze z wycięciem, a także listę wszystkich części można wydrukować na drukarce.
Będzie to Twoja mapa rozkroju (zaznaczone jest na niej również klejenie krawędzi mebli oraz szkice niestandardowych części (krzywoliniowych itp.)).
Zatem, jak widać, samodzielne wykonanie wzoru cięcia arkusza jest dość łatwe.
Myślę, że najzwyklejszy meblarz powinien sobie z tym poradzić, bo to wszystko w pewnym sensie świadczy o poziomie jego kwalifikacji.
Cóż, na tym „zaokrąglę”, do zobaczenia wkrótce.
Ten artykuł jest logicznym zakończeniem serii artykułów na temat samodzielnego projektowania i obliczania mebli do domu.
Tutaj opowiem o tym, jak wykonać ekonomiczne cięcie w domu, wskażę wszelkiego rodzaju niuanse i możliwe pułapki, na które należy się przygotować, decydując się na zlecenie cięcia płyt wiórowych w produkcji mebli.
FAQ lub często zadawane pytania
1 - Dlaczego sam tniesz?- Przede wszystkim samodzielne wycinanie elementów z płyty wiórowej to Twoja oszczędność.
Faktem jest, że większość firm meblowych docinających płyty wiórowe sprzedaje płyty na sztuki. Oznacza to, że jeśli potrzebne części nie mieszczą się na płycie wiórowej, a przynajmniej jedna część ląduje na drugiej płycie, musisz zapłacić za dwa pełne arkusze płyty wiórowej.
Zgadzam się, płacenie za dwa talerze nie jest zbyt opłacalne, jeśli w rzeczywistości okaże się, że tylko arkusz płyty wiórowej i kilka drobnych detali trafia do szafy lub kuchni.
Dlatego lepiej jest wykonać cięcie samodzielnie w domu, zgodnie z czym można zamówić docięcie w warsztacie meblowym.
2 - Co powinienem zrobić, jeśli mimo wszystko po cięciu płyty wiórowej zostaną duże pozostałości?- To proste - spójrz na swoje mieszkanie i dom na nowo. Możesz potrzebować małego stolika kawowego lub półek na książki.
Resztę wykorzystaj mądrze, pomyśl o nowych elementach dekoracyjnych i funkcjonalnych do wnętrza i dodaj je do swojego gniazdowania.
W ten sposób zakup części z płyty wiórowej zmieni się z oczywiście nieopłacalnego w bardzo ekonomiczny i przemyślany.
3 - Jaka jest budowa płyty wiórowej? Jak rozumieć ekspresję producentów mebli – zgodnie ze strukturą czy wbrew strukturze?- Zwróć uwagę na kolorystykę płyty wiórowej laminowanej, jeśli jest w niej wzór przypominający drzewo, to ma ona schematyczne przedstawienie tej właśnie „struktury”, czyli struktury kory drzewa, imitującej konkretny gatunek (buk, jesion, sosna, dąb, olcha, wiśnia i inne.)
Zgadzam się, fasady mebli wyglądają raczej głupio, na których rozproszony jest wzór (struktura) - na jednym wzdłuż, na drugim w poprzek, a potem znowu wzdłuż.
Dlatego przed zamówieniem płyty wiórowej do produkcji należy mieć pod ręką listę części napisaną według określonych zasad i kolejności.
Zwróćmy więc uwagę na to, jak wygląda płyta wiórowa laminowana z wzorem.
Widzimy, że konstrukcja przebiega wzdłuż długiego boku. A jeśli detale leżą równolegle do przedstawionych włókien, producenci mebli będą nazywać taki detal „wzdłuż konstrukcji”, jeśli są prostopadłe, to „w stosunku do konstrukcji”.
4 - Jak poprawnie określić wymiary na liście, aby części tego samego typu miały ten sam wzór konstrukcji?- Pierwszą i najważniejszą rzeczą jest określenie widocznych elementów, na których konstrukcja musi być usytuowana w tym samym kierunku.
Na przykład fasady, boki szafek, cokół przedni. Ale te części, które znajdują się wewnątrz szafki (półki wewnętrzne, boki szuflad i tym podobne) można losowo wyciąć z płyty wiórowej.
Określając wymiary warsztatu meblowego, lepiej wcześniej wyjaśnić, gdzie planujesz wyciąć płytę wiórową, jaki rozmiar części wskazać jako pierwszy.
W większości firm meblowych rozmiar części biegnącej wzdłuż konstrukcji, czyli wzdłuż wzoru, jako pierwszy wskazuje rozmiar części.
A teraz dokładnie przejrzyj poniższy schematyczny szkic - starałem się na nim jak najdokładniej zobrazować, jak będą wyglądać części przy rozmiarach wskazanych przez konstrukcję i względem konstrukcji.
5 - Jakie jest podłoże płyty wiórowej? Dlaczego przy samodzielnym wycinaniu elementów z płyty wiórowej należy podawać rozmiar płyty mniejszy niż rzeczywisty? - Rzeczywiście, znając standardowe wymiary arkusza płyty wiórowej, podczas tworzenia wykroju należy wziąć pod uwagę podłoże arkusza, co z pewnością zostanie wykonane w warsztacie przed docięciem części.
Zwykle na krawędziach płyty znajdują się odpryski, nierówności, a może nawet niewielkie obrzęki. Dlatego w tartakach „podstawowy arkusz płyty wiórowej” - przycina się 10-15 mm z każdej strony. Na tej podstawie należy również wykonać podstawę, to znaczy przyjąć ją jako odpowiedni rozmiar, na przykład nie 1830 x 2750 mm, ale 1810 x 2730 mm.
6 - Jaka jest szerokość cięcia i jaka jest równa?- Szerokość rzazu to szerokość cięcia piły. Piła zamontowana na pile ma grubość 4 mm, co oznacza, że pomiędzy częściami powstanie nacięcie o grubości tych samych 4 mm.
Oznacza to, że rzeczywisty rozmiar, na którym zostaną umieszczone dwie części 300 i 400 mm, nie wynosi 700 mm, ale 300 + 400 + 4 = 704 mm. Każde cięcie należy również wziąć pod uwagę podczas cięcia.
Cóż, to wszystko, teraz możesz przystąpić bezpośrednio do samodzielnego wycinania części z płyty wiórowej, co można wykonać na dwa sposoby - ręcznie, za pomocą linijki, ulotki, gumki, kalkulatora oraz za pomocą komputerowego programu do cięcia offline lub online.
Ręczne cięcie elementów z płyty wiórowej: Instrukcje krok po kroku
1 Narysuj na kartce papieru, najlepiej w skali, wymiary talerza. Pamiętaj, aby zmniejszyć go z każdej strony o 10 mm.
2 Posortuj listę według tego samego rodzaju wymaganych części. Na przykład boki szafek kuchennych mają te same wymiary - 500 x 712 mm.
Jest ich sporo, wypisz wszystkie takie szczegóły osobno. Na tej samej zasadzie kontynuujesz sortowanie: ta sama szerokość, ta sama struktura i tak dalej.
3 Rozłóż na arkuszu płyty wiórowej pierwsze duże części i te, które powinny mieć podobną strukturę. Nie zapomnij o szerokości brzeszczotu - 4 mm! Tutaj z pomocą przychodzi kalkulator.
4 Umieść resztę szczegółów. Możesz opracować kilka opcji, aż znajdziesz tę, która jest idealna, tak ekonomiczna i opłacalna, jak to tylko możliwe.
Wycinanie detali z płyty wiórowej za pomocą programów komputerowych online i offline
W Internecie, w domenie publicznej, istnieje wiele programów do cięcia płyt wiórowych, które oferują kilka opcji cięcia jednocześnie.
Takich programów można szukać na specjalistycznych forach meblowych lub po prostu wpisując w dowolnej wyszukiwarce zapytanie: „Program do cięcia płyt wiórowych za darmo”.
Wyszukiwanie zwróci trzy główne opcje:
1 Pobierz program do cięcia na swój komputer - najpopularniejszy i najwygodniejszy dla początkujących program do cięcia płyt wiórowych - Cięcie. Prosty interfejs, przejrzysty układ i wiele opcji piłowania blachy.
2 Twórz cięcie płyt wiórowych online - tutaj nie musisz ładować komputera programami, które mogą nie przydać się w przyszłości.
3 Cięcie i zamawianie piłowania płyt wiórowych online na stronie internetowej firmy meblarskiej to idealna opcja, jeśli warsztat produkcyjny jest dla Ciebie dogodny geograficznie.
W ten sposób „ubijesz dwie, a może więcej ptaków na jednym ogniu” – wybierz na stronie płytę wiórową, która jest dostępna w wymaganej ilości, wykonaj ekonomiczne cięcie, sprawdź koszt i od razu, siedząc w domu, zamów płytę wiórową cięty w warsztacie meblowym.
Powtórzę najważniejsze kwestie...
Podstawowe zasady cięcia płyt wiórowych
- Rozmiar arkusza płyty wiórowej laminowanej należy wpisać uwzględniając podłoże płyty.
- Szerokość cięcia piły wynosi 4 mm.
- Szczegóły cięcia należy wykonać z uwzględnieniem struktury.
Jeśli masz jakieś pytania - zadaj je tutaj, pod artykułem. Postaram się odpowiedzieć niezwłocznie.
Ponadto, jeśli są jakieś aktualne tematy meblowe, o których chcielibyście przeczytać, napiszcie o nich w komentarzach. Być może właśnie to będzie impulsem do napisania kolejnego artykułu.
Zawsze Twój, Timur Denisow.
Pobierz Cięcie
Cięcie 6.54.121 to ciekawy i niezbędny program z możliwością zbudowania mapy rozkroju dla różnych materiałów przemysłowych. Np. cięcie płyt wiórowych, szkła, tworzyw sztucznych, materiałów w rolkach i arkuszy.
Główne „żetony” programu:
- Prace w aplikacji rozpoczynają się od wprowadzenia pojęcia „Zamówienie”. Uważa się, że jest to zespół części o określonych parametrach wysokości i szerokości. Detale osadzone są w kształcie prostokąta.
- W zamówieniu możesz określić żądaną liczbę części. W tym przypadku program poda optymalną ilość arkuszy do zakupu.
- Istnieje możliwość przejrzenia historii zamówień, zmiany już zrealizowanego lub powtórzenia go z nowymi parametrami.
- Dla każdego pojedynczego elementu można ustawić symboliczną nazwę, liczbę tych elementów oraz obecność/brak krawędzi (szczególnie przy produkcji paneli meblowych).
- Oprócz arkuszy standardowych istnieje możliwość wprowadzenia arkuszy dodatkowych i docięcia ich obok arkuszy głównych.
- Możesz określić ilość „odpadów gospodarczych” do ich późniejszego wykorzystania. Jest to możliwe pod warunkiem dużej, masowej produkcji.
- Można określić ilość odpadów technologicznych, np. zużycie materiału na piłowanie.
- Przy rozliczeniu istnieje możliwość łączenia różnych zamówień z tego samego materiału. W ten sposób możesz zaoszczędzić na cięciu.
- W programie do swobodnego cięcia możesz pracować z dwoma rodzajami krawędzi.
- Cięcie odbywa się metodą gilotynową, czyli od krawędzi do krawędzi. Wszystkie cięcia są równe, ściśle pionowe lub poziome.
- Istnieją dwa sposoby zagnieżdżania w oprogramowaniu: minimalizacja odpadów (maksymalne wykorzystanie materiału) i maksymalizacja ciągłego przycinania (minimalna ilość odpadów plus maksymalne przycinanie biznesowe).
- Podczas cięcia materiału w rolce program na maszynie ma możliwość wyboru opcji umieszczenia elementów na taśmie. Wszystkie części będą prostokątne i o nieznanej wysokości.
- Istnieje możliwość wykorzystania programu do cięcia w trybie sieciowym.
- Nie ma bariery językowej, ponieważ program został wydany w języku rosyjskim.
- Interfejs jest prosty, w kojących kolorach, jak każdy inny program graficzny.
- Systemy operacyjne, dla których program jest odpowiedni: WindowsXP, WindowsVista, Windows7.
Program do cięcia arkuszy i rolek znajduje zastosowanie w różnych produkcjach technicznych i przemysłowych, zakładach, fabrykach, a także w małych przedsiębiorstwach. W warunkach domowych za pomocą tego programu można wykonać obliczenia dotyczące budowy ogrodu lub wanny, naprawy wnętrza lub licowania domu. Cięcie 6.54.121 zapewni wysoką jakość i szybkie obliczenie materiału. Najczęściej aplikacja służy do obliczania płyt wiórowych i szkła.
Skąd mogę bezpiecznie i za darmo pobrać program.
Pospiesz się, aby pobrać program za darmo z Softldol.com. Jest ona dostępna poprzez bezpośredni link bez rejestracji i płatnych wiadomości.
Wersja: 6.54.121
Stan programu: Shareware
Rozmiar: 3,5 Mb
Deweloper: Andriej Kuzniecow
System: Windows 7, 8, XP, Vista
Język rosyjski: Tak
Pobierz za darmo Nesting 6.54
Najpierw użyłem Cięcia 2, potem Cięcia 3. Różnią się dość mocno. Ale wersja Cutting 2 bardziej mi się podobała. Trzecia wersja ma dodatkowe funkcje, które w zasadzie nie są tak naprawdę potrzebne w produkcji na małą skalę. Cięcie 2 nadal pomaga mi wstępnie obliczyć ilość materiału i długość linii cięcia w przypadku dużych zamówień, takich jak kuchnia. Do stworzenia ostatecznej mapy rozkroju korzystam z programu Nowy Rozkrój (Cut Optimiser lub New Cut Manager) od twórców programu PRO100. . Obie strony można przełączyć na język rosyjski i zapoznać się z opisami programów. A teraz opiszę prosty proces tworzenia map rozkroju. .
Każdy stworzony przez nas projekt otwieramy w PRO100. Kliknij zakładkę Σ.
W oknie, które zostanie otwarte, wyświetli się tabela, w której wskazane zostaną wszystkie elementy projektu wraz z ich charakterystyką. W dolnej części okna znajduje się zakładka Kopiuj wszystko.
Klikamy na to. Teraz możemy wstawić tabelę z naszymi elementami do listy części w Cięciu 2. Potrzebujemy jednak tylko elementów z materiału bazowego, powiedzmy płyty wiórowej 18 mm. Otwieramy zatem Excel i wstawiamy listę elementów PRO100. Teraz wybierz te linie, w których elementy nie mają 18 mm i usuń je. W rezultacie pozostaje tabela składająca się z 4 kolumn, z których w jednej we wszystkich komórkach znajduje się tylko liczba 18. Zaznacz i usuń tę kolumnę. Pozostałe elementy są wybierane i kopiowane. Uruchamiamy program Cięcie 2. Po prawej stronie znajduje się tabela części.
Jeśli nie jest pusta, kliknij ikonę X nad prawą tabelą i potwierdź wyczyszczenie listy. Teraz klikamy prawym przyciskiem myszy pierwszą pustą komórkę listy i z rozwijanego menu wybieramy linię Dodaj ze schowka.
Kliknij ikonę Wykonaj obliczenia.
Mapa cięcia jest gotowa. Można wydrukować i wykorzystać. Spotkały mnie jednak pewne niedogodności. Na przykład liczby są małe, linie cięcia nie są wystarczająco wyraźne.
Osoby, które wycinały dla mnie materiał, były niezadowolone z konieczności użycia szkła powiększającego. Ale do wstępnego obliczenia kosztu produktu program był idealny ze względu na opisane powyżej przeniesienie części z PRO100 do Cutting 2.
Program Nowego Rozkroju jest lepszym optymalizatorem.
Jednakże wszystkie wymiary części należy wprowadzić ręcznie.
Program oblicza kilka opcji cięcia na raz.
W zależności od tego, co jest dla Ciebie ważne, wybierasz opcję. Dla mnie bardziej odpowiednia jest opcja z mniejszą całkowitą długością linii cięcia, ale ktoś potrzebuje opcji z mniejszą ilością ozdób (śmieci).
Najpierw w ustawieniach określam opcję cięcia bez paska,
co pozwala na umieszczenie większej liczby części. Już po pierwszej próbie cięcia widzę ile wolnego miejsca zostało na ostatnim arkuszu. Jeśli więcej niż 30% nie jest zajęte przez detale, to w parametrach programu wskazuję opcję cięcia poziomego
i wykonaj końcowe obliczenia. Pozostały poziomy pas w popularnych kolorach materiału sprzedawca zachowuje, co obniża cenę mebla. Mapy gniazdowe tworzone przez Nowy Rozkroj są wystarczająco szczegółowe i przejrzyste, a wymiary są doskonale odwzorowane.
Wynik cięcia może być inny. Przykładowo wykonałeś optymalne cięcie z opcją bez paska i otrzymałeś 3 arkusze i 3 części. Jest to szczególnie ważne, jeśli sprzedawca nie sprzedaje tego koloru materiału w pasku, a jedynie w arkuszu. W takim przypadku zastosuj następującą opcję:
Podczas dodawania każdej części odznacz pole w tabeli Właściwości części w pozycji Struktura.
Następnie patrząc na swój projekt, przejrzyj detale i zwróć uwagę na strukturę w szczegółach, na której konstrukcja może być jedynie zgodna z projektem, tj. inne warianty konstrukcji tych części są niedopuszczalne. Jeśli ta metoda nie pomoże, zmniejsz wymiary ukrytych części, takich jak cokoły i listwy łączące, o 10 mm lub więcej. Ale nie przesadzaj.
Program ma jeszcze jedną ważną zaletę. Jeśli zaznaczyłeś krawędź po jednej stronie części, nie przesunie się ona z tej strony na drugą, gdy część zostanie obrócona przez optymalizator, co może się zdarzyć w innych programach. W przypadku, gdy krawędź końcowa jest papierowa, wymiary części pozostają takie same jak w projekcie, a jeśli krawędź PCV ma grubość 1-2 mm, nie zapomnij odjąć grubości krawędzi od rozmiaru sąsiednia strona z przyklejoną krawędzią.
Przykład zagnieżdżania map
Na początku filmu, aż do rozpoczęcia programu Nowy Rozkrój, nie zwracajcie uwagi. A potem wszystko w temacie. Mała usterka techniczna.
Jeśli Twój arkusz ma np. wymiary 2800 na 2070, a nacięcie wzdłuż boku wynosi 10 mm, zapominając, że do wycięcia potrzeba 4 mm, podajesz rozmiar części 2790 na 600 z krawędzią 2790. Jako w rezultacie krawędź przesunie się o 600. Zwróć uwagę na to. Raz nie sprawdziłem karty i oddałem do pracy. Po pierwsze, chłopaki ucierpieli, gdy przykleili krawędź po stronie 600, ponieważ. część opierała się o drzwi warsztatu, musiałem maszynę przesunąć. Nikt nie przypuszczał, że odległość maszyny od ściany wynosząca 2,5 m może być kiedykolwiek niewystarczająca. A po drugie, za przyklejenie krawędzi na dłuższym boku musiałem zapłacić, a w tym momencie na to nie liczyłem. Dlatego bądź ostrożny.
Zautomatyzowany system produkcyjny PractiCAM™ koncentruje się na produkcji wyrobów do systemów wentylacyjnych z blachy i walcówki, a także z półfabrykatów rurowych. PractiCAM™ współpracuje z maszynami plazmowymi i laserowymi sterowanymi numerycznie (CNC), a także z wykrawarkami, wykrawarkami spiralnymi i współrzędnościowymi. Program posiada dużą funkcjonalność związaną z cięciem blachy tj. koncentruje się nie tylko na produkcji kanałów wentylacyjnych, ale także elementów płaskich, szyldów, wiatrowskazów, elementów dachowych itp.
Główne zalety systemu PractiCAM™:
![]() |
Wykonywanie kanałów powietrznych dowolnego typu, a także wszelkich innych elementów z blach i walcówek oraz półfabrykatów rurowych |
Biblioteki systemowe PractiCAM™ bardzo rozległy i niespotykany. Zawierają ponad 4000 złączek i ponad 1600 sparametryzowanych części płaskich. Pomimo tej różnorodności, biblioteki systemowe PractiCAM™ wciąż rośnie (za każdym razem, gdy pobierzesz nową wersję naszego programu, będą na Ciebie czekać nowe pozycje). Oprócz istniejących bibliotek, możemy stworzyć dla Ciebie dowolną liczbę różnych złączek, części płaskich i innych elementów. Wykonamy potrzebne Ci części i wyślemy je do Ciebie najszybciej jak to możliwe (z reguły opracowanie nowej części w zależności od jej skomplikowania trwa od jednego do trzech dni roboczych). |
|
![]() |
Kompatybilny z każdym sprzętem |
System PractiCAM™ obsługuje wiele modeli maszyn CNC plazmowych i laserowych. Może także współpracować z wybijakami, dziurkaczami, wybijakami, obcinakami do rur i czytnikami kodów kreskowych. Jeżeli Twojego modelu maszyny nie ma jeszcze w naszej bibliotece, to w najkrótszym możliwym terminie bezpłatnie napiszemy dla Ciebie postprocesor, który połączy nasz program z Twoim sprzętem. | |
![]() |
Natychmiastowe i dokładne szacunki kosztów |
Podczas pracy system PractiCAM™ na bieżąco tworzy dokładny szacunek kosztów wszystkich kosztów wytworzenia części. Pełne obliczenia uwzględniają koszt materiału, koszty pracy przy produkcji części, koszt wszystkich elementów złącznych (śruby, wkręty, opony, nity itp.), A także koszt różnych akcesoriów (ostrza, pręty , amortyzatory itp.). Jako przykład podano amerykańskie tabele SMACNA, ale możesz stworzyć własne standardowe tabele do rozliczania kosztów pracy w swoim przedsiębiorstwie, biorąc pod uwagę specyfikę Twojej produkcji. | |
![]() |
Eksport i import informacji w popularnych formatach .dxf, dwg i .csv do komunikacji z oprogramowaniem firm 1C, Microsoft, Autodesk |
Wszelkie informacje o zużytym metalu, materiałach eksploatacyjnych i komponentach znajdujących się w systemie Practicam™, można przekonwertować do pliku .csv, który jest obsługiwany przez 1C: Księgowość i Microsoft Excel. Dzięki temu możesz obliczyć koszt wszystkich swoich produktów za pomocą programów księgowych. System PractiCAM™ może pracować z plikami .dxf i .dwg, co pozwala na import rysunków z programów AutoCAD i Compass, a także eksport do tych programów planów rozmieszczenia, wzorów dopasowań i części płaskich. |
|
![]() |
Importuj zamówienia z programu 1C: Księgowość |
W programie 1C: Księgowość możesz tworzyć zamówienia na cięcie okuć, wskazując nazwy okuć, ich ilość, materiał, z którego powinny być wykonane, parametry technologiczne, nazwy naddatków itp., I wysyłać je do systemu PractiCAM™. Po otrzymaniu zamówienia system PractiCAM™ automatycznie wyszukuje określone łączniki w swoich bibliotekach, stosuje do nich określone parametry i układa wzory złączek na blachach. Po automatycznym ułożeniu generowane są polecenia sterujące dla Twojego sprzętu, a także różne raporty i etykiety. | |
![]() |
oszczędność metalu |
Istnieje możliwość wykorzystania pozostałej części blachy, odpowiedniej do wycięcia z niej dowolnych produktów i maksymalnego wykorzystania powierzchni blachy. W tym celu dodano moduł funkcjonalny „Magazyn”, który pozwala po ułożeniu głównych części roboczych na blachy automatycznie dodać części płaskie z wcześniej utworzonej listy w nieużywane miejsce. | |
![]() |
Możliwość automatycznego układania produktów za pomocą cięcia kombinowanego |
W PractiCAM™ Istnieją dwie możliwości automatycznego układania produktów w stosy: normalne układanie i układanie z kombinowanym cięciem dla produktów, które można łączyć wzdłuż jednego ze stron. | |
![]() |
W pełni zrusyfikowany |
Oprócz języka rosyjskiego, system PractiCAM™ przetłumaczone na język angielski, francuski, hiszpański, chiński i koreański. | |
![]() |
Różne rodzaje zasiłków |
Naddatki (złącza, zamki, złącza, szwy) i wycięcia zawarte w dużej liczbie w bibliotekach systemowych Practicam™, można stworzyć w dowolnym kształcie geometrycznym, w pełni sparametryzowanym i edytowalnym. Edytor graficzny zapewnia szerokie możliwości tworzenia i edycji naddatków i nacięć. | |
![]() |
Tworzenie raportu |
System PractiCAM™ udostępnia szeroką gamę standardowych szablonów raportów. Oprócz tego możesz tworzyć własne formularze raportowe w dowolnym dogodnym formacie i dowolnym układzie. Najważniejsze, że w raporcie możesz zgłosić dowolne informacje zawarte w systemie Practicam™. | |
![]() |
Utwórz etykiety |
Oznacz części w systemie PractiCAM™łatwe i wygodne. Dostępne są różne szablony etykiet, ale jeśli Ci nie odpowiadają, możesz stworzyć własny szablon. Dodaj dowolne informacje do swoich etykiet: logo swojej organizacji, kody kreskowe, obrazy części 3D, dowolne parametry części, które Cię interesują; edytuj te podpisy, używając dowolnego stylu i rozmiaru czcionki. Możesz wykonać etykietę dla dowolnego pasującego i płaskiego elementu. | |
![]() |
Przydatne specyfikacje |
Specyfikacje (SNiP) systemu PractiCAM™ umożliwiają ustawienie wszystkich funkcji standardów produkcyjnych podczas pracy z różnymi produktami, co pozwala na ujednolicenie produkcji, automatyzację wprowadzania produktów do produkcji i redukcję błędów wejściowych, zwiększając w ten sposób produktywność, a wraz z nią zysk. Możesz stworzyć własne zasady wytwarzania produktów, które będą wykorzystywane w Twoim przedsiębiorstwie. | |
![]() |
Dostępność bibliotek okuć do ścian podwójnych |
W systemie PractiCAM™ istnieją biblioteki podwójnych okuć ściennych. Stosuje się je w przypadkach, gdy konieczne jest zwiększenie poziomu izolacji cieplnej i akustycznej. W przypadku każdego mocowania do podwójnych ścian można przyciąć izolację tak, aby pasowała pomiędzy jego ścianami. | |
![]() |
Możliwość ręcznej i automatycznej segmentacji dla dużych produktów |
System PractiCAM™ pozwala na segmentację (rozbicie na osobne komponenty) produktów o dużych gabarytach, które nie mieszczą się na arkuszu blachy. Możesz samodzielnie ustawić zasady segmentacji dla każdego produktu lub powierzyć ten proces programowi. |
Korzyści z naszego wsparcia technicznego:
- Lepsze wsparcie produktu — na życzenie użytkowników rozwijamy i dodajemy nowe moduły oprogramowania, tworzymy nowe kształtki i parametryczne części płaskie (w ciągu 1-3 dni, w zależności od złożoności produktu), dodajemy nowe sposoby docinania kształtek do już istniejących .
- Bezpłatne szkolenie z obsługi programu.
- Regularna aktualizacja PractiCAM™— nowe wydanie pojawia się co najmniej 1 raz w ciągu 2 tygodni.
- Opracowywanie i dodawanie nowych etykiet i raportów, umieszczanie na nich informacji wymaganych przez użytkownika.
Obecnie trwają prace nad nową wersją programu PractiCAM™. Główną różnicą jest to, że teraz program jest podzielony na wiele modułów funkcjonalnych, które można włączać i wyłączać w różnych kombinacjach, zmniejszając lub zwiększając zestaw funkcji wykonywanych przez program. W zależności od ilości zawartych modułów kształtuje się cena programu. PractiCAM™ nadal można kupić w całości ze wszystkimi jego funkcjami, ale istnieje także możliwość zakupu jednego ze standardowych pakietów programów (z których każdy jest okrojoną wersją systemu PractiCAM™) lub pakiet standardowy z dodatkowymi opcjami.
Pakiety standardowe PractiCAM™:
PractiCAM™ dla części ogólnych.
- Korzystaj z bibliotek parametrycznych części płaskich (dwuwymiarowych), twórz części płaskie za pomocą edytora graficznego.
- Pracuj z graficznym modelem części, ustaw wymiary, materiał i grubość.
- Podczas tworzenia części użyj wielu warstw.
- Importuj pliki z rozszerzeniem .dxf, .dwg (systemy AutoCAD, Compass itp.).
- Zastosuj automatyczne układanie części na blachach przy użyciu różnych algorytmów, w tym cięcia kombinowanego.
- Ręcznie ułóż części na arkuszach metalu.
-
przy wyjściu).
PractiCAM™ do wentylacji.
Pakiet ten umożliwia użytkownikowi:
- Skorzystaj z bibliotek złączek (złączek).
- Pracuj z graficznym modelem 3D złączki, ustaw wymiary, naddatki, materiał i określ sposób docięcia kształtki.
- Pracuj z biblioteką akcesoriów do okuć, klap ustalających, usztywnień, cięgien, łopatek obrotowych.
- Używaj różnych wgłębień do znakowania, automatycznie generuj linie gięcia, twórz linie znakowania.
- Utwórz bibliotekę używanych materiałów ze wskazaniem grubości materiału i rodzaju (arkusz, rolka).
- Utwórz bibliotekę wykorzystanych naddatków (złącza, zamki, złącza).
- Zastosuj automatyczne układanie wzorów produktów na blachach przy użyciu różnych algorytmów, w tym cięcia kombinowanego.
- Ręcznie układaj wzory produktów na arkuszach blachy.
- Na podstawie wyników układania generuj i drukuj mapy układania.
- Na podstawie wyników układania automatycznie generuje sekwencję poleceń sterujących (CNC) dla plotera.
- Ustaw parametry frezu (wymiary stołu, położenie i orientacja stołu, rozmiar i kształt cięcia na wejściu i cięciu
przy wyjściu). - Określ sposób przesyłania poleceń sterujących do plotera (za pośrednictwem pliku lub portu COM).
- Automatycznie segmentuj (tnij na kawałki) wzory o dużych rozmiarach.
- Automatycznie dodawaj dodatki podczas segmentowania wzorców.
- Twórz i edytuj naddatki na szwy łączące podzielone na segmenty części wzorów.
- Twórz tabele, aby ponownie obliczyć parametry przekroju złączki i zastosować je podczas tworzenia złączy.
- Importuj/eksportuj pliki z rozszerzeniem .pmx (pliki programu PractiCAM™).
PractiCAM™ Klasyczny.
Pakiet ten łączy pakiety „Części ogólne PractiCAM™” i „PractiCAM™ Ventilation” i zapewnia wszystkie funkcje wymienione dla tych pakietów.
Listę dodatkowych opcji (możliwości programu) pakietów podano w tabeli.
Jeśli chcesz dowiedzieć się więcej o PractiCAM™, możemy przeprowadzić demonstrację programu za pomocą Skype lub TeamViewer, całkowicie bezpłatnie, w dogodnym dla Ciebie terminie, jednocześnie odpowiadając na wszystkie Twoje pytania. Dodatkowo specjalnie dla sterownika Twojej maszyny na Twoje zlecenie możemy napisać postprocesor i aktywować dla Ciebie PractiCAM™ na 1 miesiąc całkowicie bezpłatnie, abyś mógł ocenić wszystkie jego możliwości bezpośrednio w pracy. Wystarczy, że do nas zadzwonisz, napiszesz wiadomość na nasz e-mail lub zostawisz swoje dane kontaktowe wypełniając poniższy formularz.
Ekonomiczne cięcie liniowe materiałów (cięcie listew) ma znaczenie w wielu gałęziach przemysłu oraz w budownictwie. Jest to cięcie kłód i desek w obróbce drewna, cięcie prętów, prętów zbrojeniowych, kątowników, ceowników, rur, dwuteowników na półfabrykaty...
W produkcji konstrukcji metalowych i budowie maszyn, poprzecznym cięciu rolek z papierem i tkaniną w przemyśle celulozowo-lekkim.
Pomimo pozornej prostoty rozwiązanie problemów cięcia liniowego nie jest bardzo łatwe, ale warte zachodu. Wprowadzenie naukowego podejścia do cięcia materiałów formowanych pozwala na obniżenie ich kosztów, czasem nawet o ponad 10%! Przeczytaj artykuł do końca i upewnij się, że te słowa są prawidłowe.
Rozważana tematyka dotyczy problemów programowania liniowego. Aby rozwiązać takie problemy, naukowcy w ciągu ostatnich 70 lat opracowali kilka różnych metod.
Metoda wskaźników L.V. Kantorowicz i V.A. Zalgallera z pewnymi umiejętnościami pozwala skutecznie wykonywać cięcie liniowe „ręcznie” bez użycia technologii komputerowej. Ciekawskim czytelnikom polecam zapoznanie się z tą metodą poprzez lekturę książki wyżej wymienionych autorów „Racjonalne Cięcie Materiałów Przemysłowych”.
Metoda simpleksowa oparta na pomysłach L.V. Kantorowicza, zostało szczegółowo opisane i opracowane przez szereg naukowców z USA w połowie XX wieku. Dodatek MS Excel „Wyszukaj rozwiązanie” (Solver) wykorzystuje ten algorytm. To właśnie dzięki tej metodzieprzewyższaćw tym artykule rozwiążemy problem cięcia liniowego.
Później pojawiły się i zostały opracowane algorytmy genetyczne, chciwe i kolonii mrówek. Ograniczymy się jednak do ich zestawienia i przejdziemy do rzeczy, bez wchodzenia w gąszcz teorii (chociaż tam, „w dziczy”, jest to bardzo ciekawe).
Włączmy Excela i na prostym przykładzie cięcia metalowych prętów na części zapoznamy się z jednym ze sposobów rozwiązania praktycznych problemów cięcia liniowego. Matematycy często nazywają ten problem „problemem cięcia”.
Nie wymyśliłem początkowych danych dla przykładu, ale wziąłem je z artykułu Pokrowskiego M.A. „Minimalizacja nieuniknionych strat materiałów w produkcji przemysłowej przy cięciu ich na półfabrykaty” opublikowany w nr 5 (maj 2015) elektronicznego czasopisma naukowo-technicznego „Biuletyn Inżynieryjny” wydawanego przez FGBOU VPO „MSTU im. NE Baumana (link:angielski. bmstu. pl/ doktor/775784. HTML).
Celem jaki sobie postawiłem było porównanie wyników rozwiązania problemu.
Przykład rozwiązania problemu cięcia liniowego w programie MS Excel.
Umówmy się, że:
1. Półfabrykaty to surowiec w postaci sztabek, pasków, prętów itp. tej samej długości.
2. Detale to elementy, które należy uzyskać poprzez pocięcie oryginalnych półfabrykatów na kawałki.
3. Szerokość piły, cięcia, pocierania przyjmuje się jako równą zeru.
Zadanie:
Aby zrealizować jedno z zamówień, dział zaopatrzenia musi wyciąć trzy standardowe rozmiary części na nożycach kombinowanych z identycznych półfabrykatów o długości 1500 mm:
151 sztuk o długości 330 mm
206 sztuk o długości 270 mm
163 sztuki o długości 190 mm
Konieczne jest znalezienie optymalnego planu cięcia, który wykorzystuje minimalną ilość materiału i odpowiednio daje minimalną ilość odpadów.
Wstępne dane:
1. Długość oryginalnych półfabrykatów LH w milimetrach piszemy w połączonej komórce
D3E3F3: 1500
2. Przydzielamy numery I wszystkie standardowe rozmiary części, zaczynając od najdłuższego, a kończąc na najkrótszym w komórkach
D4; E 4; F4: 1; 2; 3
3. Długości części LDI w milimetrach zapisujemy
D5; E5; F5: 330; 270; 190
4. Liczba szczegółów NDI w kawałkach włożonych
D6; E6; F6: 151; 206; 163
5. Przechodzimy do bardzo ważnego etapu - wypełnienia opcji cięcia.
Trzeba pamiętać i rozumieć 2 zasady wykonywania tej pracy.
1. Długości odpadów muszą być mniejsze niż najmniejsza część ( 0< lo j < LDmin ).
2. „Wkładanie” części w obrabiany przedmiot zaczynamy od największych części i o największej ich liczbie, konsekwentnie przesuwając się w kierunku malejącym.
Jeśli w opcji cięcia nie ma rozmiaru części, to komórkę zostawiamy pustą, nie wpisujemy zera, aby ułatwić wizualne postrzeganie tabeli.
Opcja cięcia nr 1:
Próba wycięcia 5 części nr 1 z jednego wykroju jest niemożliwa, dlatego piszemy w komórce
Nie ma również możliwości dodania części nr 2 lub części nr 3 do gniazda, dlatego komórki pozostawiamy puste
Opcja cięcia nr 2:
Zmniejszamy liczbę części nr 1 o 1 z poprzedniej wersji i zapisujemy
Próbujemy dodać 2 części nr 2 - nie działa, więc dodajemy
Pozostaje możliwość uzupełnienia wycinania detalem nr 3. Wchodzimy w
Trzymając się wyrażonych zasad, analogicznie uzupełniamy wszystkie 18 możliwych opcji cięcia w tym przypadku.
Po samodzielnym sporządzeniu kilku tabel opcji cięcia zrozumiesz logikę działań i poświęcisz kilka minut na tę pracę.
Jeśli podczas cięcia nie zostanie spełniona pierwsza zasada, wówczas komórka z długością odjazdu zostanie automatycznie pomalowana na czerwono. Formatowanie warunkowe zastosowane do komórek G7…G24 z pewnością pomoże Ci w tej pracy.
W komórkach H7...H24 nic nie pisz! Służą do wyświetlenia wyniku rozwiązania!
Przygotowanie rozwiązania:
* W komórkach G7...G24 długości odpadów (nacięć) pozostałych po cięciu obliczane są według wzoru
lo j = L H -Σ (LDI * NDja )
6. Liczba części każdego standardowego rozmiaru, wykonanych według wszystkich zastosowanych opcji zagnieżdżenia, zostanie obliczona w komórkach D26, E26 i F26 zgodnie ze wzorem
NDIoblicz = Σ (NDja * NHJ )
Liczba części na planie rozkroju znajdującym się na końcu rozwiązania musi w pełni odpowiadać podanej liczbie części!
7. Wymagana liczba detali do wykonania optymalnego planu cięcia zostanie określona w połączonej komórce D27E27F27 za pomocą wzoru
N oblicz =ΣN HJ
8. Całkowita długość wszystkich półfabrykatów wymaganych do wykonania liniowego zagnieżdżenia wszystkich części zostanie obliczona w połączonej komórce D28E28F28 za pomocą wzoru
LH Σ = L H*Nz obliczeń
9. Całkowita długość wszystkich odpadów powstałych w wyniku realizacji znalezionego planu rozbiórki zostanie obliczona w połączonej komórce D29E29F29 przy użyciu wzoru
LO Σ = Σ (LOJ * NHJ )
10. Proporcja odpadów powstałych w wyniku optymalnego planu rozkroju liniowego do całkowitej ilości użytego materiału zostanie obliczona w połączonej komórce D30E30F30 przy użyciu wzoru
o.o = Lo Σ /Lз Σ
Rozwiązanie:
Przygotowanie jest zakończone, określa się 18 opcji najbardziej optymalnego cięcia jednego przedmiotu na części i wprowadza się wszystkie niezbędne formuły. Teraz musimy rozwiązać główny problem: ustalić optymalny plan rozkroju - ile półfabrykatów i według jakich opcji cięcia wyciąć aby w końcu uzyskać wszystkie niezbędne części w odpowiedniej ilości przy minimalnej ilości odpadów.
1. W menu głównym wybierz „Serwis” – „Wyszukaj rozwiązanie…”.
2. W wyświetlonym oknie o tej samej nazwie „Wyszukaj rozwiązanie” dokonujemy ustawień.
2.1. Całkowitą długość odpadu przypisujemy funkcji celu Lo Σ i wprowadź łącze w oknie komórki docelowej.
2.2. Ustaw przełącznik „Równe:” w pozycji „Wartość minimalna”.
2.3. Określ komórki ze zmiennymi Nz j w oknie Zmiana komórek.
2.4. Ograniczenia wprowadzamy w oknie o tej samej nazwie. Jako warunki wskazujemy na potrzebę równości danego Nd I i rozliczenie Nd oblicz liczba części, a także zmienne Nz j- szacowana liczba półfabrykatów według opcji wycinania - narzucamy ograniczenie: muszą to być liczby całkowite.
3. Naciskamy przycisk „Parametry” i w wyskakującym oknie „Parametry wyszukiwania rozwiązania” dokonujemy ustawień zgodnie z poniższym zrzutem ekranu. Zamknij okno przyciskiem OK.
4. W oknie „Wyszukaj rozwiązanie” kliknij przycisk „Uruchom” i poczekaj, aż Excel znajdzie rozwiązanie. To może zająć kilka minut.
5. Po zapisaniu znalezionego rozwiązania przyciskiem OK wyniki zostaną wyświetlone w komórkach H7...H24 arkusza Excel.
Poniższy rysunek przedstawia znaleziony optymalny liniowy plan cięcia.
Jaki jest wynik?
Cięcie liniowe w wykrojach Excel dla zadań takich jak omówione w tym artykule wykonuje się metodą opisaną powyżej w 10-15 minut! „Ręcznie”, nie znając metody wskaźników Kantorowicza, nie znajdziesz rozwiązania w takim czasie.
Uruchamiając kilkakrotnie opcję "Szukaj rozwiązania" z różnymi parametrami wyszukiwania, udało nam się znaleźć 5 różnych planów ścinania półfabrykatów. Wszystkie 5 planów wymaga tej samej liczby półfabrykatów - 93 i daje tylko 2,21% odpadu!!! Plany te są o prawie 6% lepsze od planu obliczonego przez Pokrowskiego i o ponad 10% oszczędniejsze od planu „Tradycyjnego” (link do oryginalnego źródła w pierwszej części artykułu). Bardzo godny wynik udało się osiągnąć szybko i bez użycia drogich programów.
Należy zaznaczyć, że dodatek Excel Solver („Wyszukaj rozwiązanie”), który przy rozwiązywaniu problemów programowania liniowego wykorzystuje metodę simpleks, może pracować z nie więcej niż 200 zmiennymi. W odniesieniu do rozważanego przez nas problemu cięcia liniowego oznacza to, że liczba cięć nie może przekraczać 200 wariantów. Do prostych zadań to wystarczy. W przypadku bardziej skomplikowanych zadań warto spróbować zastosować „mieszankę” algorytmu „zachłannego” i metody Simplex Solver, wybierając z pełnej listy sadzonek nie więcej niż 200 najbardziej ekonomicznych. Wtedy wyposażamy się w cierpliwość i osiągamy rezultaty. Możesz spróbować rozbić złożony problem na kilka prostych, ale „poziom optymalności” znalezionego rozwiązania będzie najprawdopodobniej niższy.
Być może rozważaną opcją rozwiązania problemów związanych z wycinaniem liniowym nie jest „akrobacja”, ale zdecydowanie jest to krok naprzód w porównaniu do „tradycyjnego” podejścia w wielu branżach.
Użycie dodatku MS Excel "Wyszukaj rozwiązanie" (Solver) było już omawiane na blogu w jednym artykule. Myślę, że to wspaniałe narzędzie jest godne szczególnej uwagi i pomoże nie raz z wdziękiem i szybko rozwiązać szereg nowych, nietrywialnych problemów.
P.S. Linki do najlepszego darmowego oprogramowania do cięcia liniowego, jakie znalazłem w sieci:
http://stroymaterial-buy.ru/raschet/70-raskroy-lineynih-izdeliy.html
http://forum-okna.ru/index.php?app=core&module=attach§ion=attach &attach_id=7508
http://forum.dwg.ru/attachment.php?attachmentid=114501&d=13823277 74
http://www.planetcalc.ru/917/
Programy z dwóch ostatnich linków implementują zachłanną heurystykę i wykonują liniowe zagnieżdżanie w zadaniu z artykułu, wykorzystując aż 103 spacje. Stosowanie algorytmów zachłannych jest uzasadnione w przypadkach, gdy konieczne jest skrócenie całkowitego czasu operacji cięcia przy zbyt dużej liczbie opcji cięcia w bardziej optymalnych planach.
Pod artykułem w bloku „Recenzje” możecie, drodzy czytelnicy, wpisać swoje uwagi.
Można również wycinać arkusze ręcznie, ale wymaga to dużo czasu i specjalnych umiejętności. O wiele łatwiej jest to zrobić, korzystając z programów towarzyszących. Pomogą zoptymalizować mapę zagnieżdżeń, zaoferują inne opcje układu i pozwolą na jej samodzielną edycję. W tym artykule wybraliśmy dla Ciebie kilku przedstawicieli, którzy wykonują świetną robotę.
Astra Nesting umożliwia pracę z zamówieniami poprzez import ich półfabrykatów z katalogu. W wersji próbnej dostępnych jest tylko kilka szablonów, ale ich lista powiększy się po zakupie licencji na program. Użytkownik ręcznie tworzy arkusz i dodaje szczegóły do projektu, po czym oprogramowanie automatycznie tworzy zoptymalizowaną mapę rozkroju. Otwiera się w edytorze, gdzie jest dostępny do edycji.
Astra S-Nesting
Kolejny przedstawiciel różni się od poprzedniego tym, że oferuje jedynie podstawowy zestaw funkcji i narzędzi. Ponadto można dodawać tylko wstępnie przygotowane części określonych formatów. Mapa zagnieżdżeń pojawi się dopiero po zakupie pełnej wersji Astry S-Nesting. Ponadto istnieje kilka rodzajów raportów, które są generowane automatycznie i można je natychmiast wydrukować.
Plaz5
Plaz5 to przestarzałe oprogramowanie, od dawna nie wspierane przez dewelopera, ale nie przeszkadza to w wykonywaniu swoich zadań z wysoką jakością. Program jest dość łatwy w obsłudze, nie wymaga żadnej specjalnej wiedzy ani umiejętności. Mapa zagnieżdżenia powstaje dość szybko, a użytkownik musi jedynie określić parametry części, arkuszy i zaprojektować mapę.
ORION
Ostatnim na naszej liście będzie ORION. Program realizowany jest w formie kilku tabel, w których wprowadzane są niezbędne informacje, a następnie tworzona jest najbardziej zoptymalizowana mapa rozkroju. Z dodatkowych funkcji istnieje jedynie możliwość dodania krawędzi. ORION jest dystrybuowany za opłatą, a wersję próbną można pobrać na oficjalnej stronie twórców.
Cięcie materiału arkuszowego jest procesem dość skomplikowanym i czasochłonnym, ale dzieje się tak, jeśli nie używasz specjalnego oprogramowania. Dzięki programom, które sprawdziliśmy w tym artykule, proces tworzenia mapy cięcia nie zajmie dużo czasu, a od użytkownika wymaga się minimalnego wysiłku.
Program przeznaczony jest do kompleksowego rozwiązywania problemów cięcia materiałów arkuszowych. Łączy w sobie możliwości systemu przygotowania programów sterujących z funkcjami organizacji procesu produkcyjnego. Zastosowane w programie podejście do rozwiązania podsumowuje doświadczenia szeregu przedsiębiorstw obsługujących maszyny do cięcia termicznego.
Wykorzystanie bazy danych
Program integruje tradycyjne oprogramowanie obróbcze Techtran z bazą danych. Bazie danych powierzono nie tylko zadanie zarządzania różnymi danymi, ale także zarządzanie pracą systemu jako całości, gdyż obiektami bazy danych są także programy do cięcia blachy. W pierwszej kolejności do bazy danych wprowadzane są szczegóły, które można zaimportować z innego systemu, zbudować przy pomocy narzędzi Techtran lub stworzyć w oparciu o makra.
Tworzenie części w oparciu o makra
W trakcie pracy z programem w warunkach produkcyjnych stopniowo wyodrębnia się szereg typowych części, różniących się wielkością oraz obecnością lub brakiem niektórych elementów pomocniczych. Wygodnie jest przechowywać takie typowe części w bibliotece w postaci sparametryzowanej i wykorzystywać je podczas tworzenia części rzeczywistych poprzez ustawienie rzeczywistych wartości parametrów. Program umożliwia wykorzystanie sparametryzowanych części podczas tworzenia części w bazie danych. Parametry szczegółowe wprowadza się w oknie dialogowym. Użytkownicy mają możliwość opracowania makr opisujących geometrię i, jeśli to konieczne, obróbkę typowych części. Możliwe jest również zdefiniowanie opisów parametrów w celu dostosowania okna dialogowego i wejścia sterującego.
Korekta nieprawidłowej geometrii przy imporcie plików DXF.
W systemie zaimplementowano możliwość dostosowania dokładności koniugacji konturów przy imporcie plików DXF. Dokładność parowania to odległość, w obrębie której dopuszczalne jest niedopasowanie oryginalnych segmentów, która jest eliminowana podczas przekształcania ich w kontury. Dokładność parowania wpływa na to, czy blisko siebie położone segmenty zostaną połączone w jeden kontur, czy nie. Jeżeli punkty graniczne segmentów nie pokrywają się, ale odległość między nimi mieści się w granicach dokładności kojarzenia, segmenty te są łączone (łączone w jeden kontur). Segmenty kojarzone są poprzez kontynuację, obcięcie lub przesunięcie punktów końcowych – w zależności od względnego położenia segmentów:
a) Obcięcie segmentów.
b) Rozszerzenie segmentu.
c) Przesunięcie segmentu Segmenty „krótkie” (o długości mniejszej niż dokładność dopasowania) są eliminowane.
Po usunięciu „krótkiego” segmentu, sąsiednie segmenty są łączone w pary. Segmenty (lub części segmentów), które nakładają się na siebie w zakresie dokładności wiązania, są łączone. Szczegóły są wygodnie przeglądane jednocześnie z listą wszystkich szczegółów. Do zarządzania częściami i innymi obiektami bazy danych w Techtran oferowany jest pojedynczy mechanizm wizualny wykorzystujący dwa panele. Takie podejście pozwala na wykonywanie akcji na obiektach bazy danych z listy (tworzenie, usuwanie, edytowanie i przeglądanie parametrów) i jednocześnie przeglądanie graficznej reprezentacji elementów listy (części, arkuszy, układów arkuszy itp.) na sąsiednich płyta. Ponadto obecność dwóch paneli ułatwia pracę z obiektami, które po kolei zawierają inne obiekty. Na przykład gniazdo arkuszy zawiera szczegóły. Aby uporządkować przeglądanie części związanych z różnymi układami arkuszy, w jednym panelu można wyświetlić listę układów arkuszy, a w drugim - listę części umieszczonych na konkretnym arkuszu.
Zadanie cięcia
Program organizuje interakcję różnych obiektów biorących udział w procesie cięcia materiału arkuszowego. Z części, które należy wykonać, tworzone jest zadanie cięcia. Następnie arkusze do produkcji części są uwzględniane w zadaniu cięcia. Program zapewnia możliwość automatycznego i ręcznego umieszczania szczegółów pracy w celu zagnieżdżenia na arkuszach. Jednocześnie program monitoruje ilość nieplasowanych części i możliwość wyprodukowania części z wybranego arkusza.
Automatyczne rozmieszczenie części na arkuszu
W trybie automatycznego układania program optymalnie układa szczegóły zlecenia na arkuszach. Wymagane dodatkowe arkusze można automatycznie pobrać z magazynu. Program umożliwia także automatyczne umieszczenie wybranych części na konkretnym arkuszu. Jednocześnie zachowane są określone odległości od krawędzi arkusza i pomiędzy częściami. Strategia automatycznego układania zapewnia bardzo wysokie wykorzystanie materiału. Użytkownik ma możliwość wyboru optymalnego stosunku jakości rozmieszczenia części do czasu obliczeń. Automatyczne zagnieżdżanie określa sposób zagęszczania części na arkuszu, który nie jest całkowicie wypełniony. Ma to wpływ na formę i proporcje odpadów gospodarczych, biorąc pod uwagę specyfikę ich dalszego wykorzystania. Sterowanie doborem części do wypełnienia otworów pozwala na użycie mniejszych lub większych części do umieszczenia w pustych przestrzeniach wewnątrz części lub w ogóle do niewypełniania otworów.
Ręczne umieszczanie części na arkuszu
Istnieje tryb ręczny umieszczania części na arkuszu. W tym trybie część jest wybierana z listy nieumieszczonych części zadania cięcia i umieszczana na arkuszu, a następnie przenoszona w wolne miejsce za pomocą edytora graficznego. Istnieją również środki precyzyjnej kontroli względnego położenia obiektów. Połączenie automatycznego i ręcznego umieszczania części umożliwia wykorzystanie zalet każdego trybu w celu uzyskania najbardziej wydajnej pracy.
Kontrola ruchu części
W trybie ręcznego rozmieszczania program przejmuje szereg przydatnych funkcji. Należą do nich różne sposoby przemieszczania części przy zachowaniu wymaganych odległości pomiędzy częściami oraz pomiędzy częściami a krawędzią arkusza, a także możliwość umieszczania części blisko siebie.
Ścisła kontrola ruchu części. Włączenie tej funkcji pozwala na przesuwanie części po arkuszu na ekranie monitora, jak prawdziwych obiektów, dla których inne części i krawędź arkusza stanowią przeszkodę nie do pokonania.
Predykcyjna kontrola ruchu części. Dzięki kontroli zapobiegawczej ruch części nie ogranicza się do wolnego obszaru arkusza. Jeżeli jednak wejdzie w strefę nakładania się z innymi obiektami, diagnozowana jest nieprawidłowa lokalizacja poprzez zmianę koloru przesuwanej części.
Przesuwanie części do oporu. Funkcja ta umożliwia dociśnięcie części blisko samej krawędzi wolnego obszaru arkusza. Innymi słowy, podczas tej operacji część porusza się w określonym kierunku, aż dotknie części lub krawędzi arkusza.
Kopiowanie części znajdujących się blisko siebie.
Podczas kopiowania części w tym trybie odległość, na jaką część może zostać przesunięta w określonym kierunku, jest określana automatycznie, tak aby części znajdowały się blisko siebie.
Łączenie boków części pozwala na takie zorientowanie części, aby połączyć je z wybranymi bokami.
Wyrównaj części w linii prostej. Ta funkcja jest przydatna podczas układania części do obróbki przelotowej.
Programowanie przetwarzania
Po ułożeniu części na arkuszu programowana jest obróbka. W najprostszym przypadku wystarczy po kolei wskazać kontury obrabianych części. Program buduje trajektorię narzędzia z uwzględnieniem niezbędnych korekt, generuje dosunięcia, odsunięcia i ruchy pomocnicze narzędzia, polecenia włączenia i wyłączenia frezu, posuwu, korekty itp.
Podejście i odejście. Istnieje możliwość różnych ustawień dosunięcia do obrabianego konturu (po prostej, po łuku, po normalnej, po stycznej itp.), wyboru punktu dosunięcia (automatycznego lub jawnego) oraz trybów pracy krajalnicy na różnych etapach obróbki.
Zworki. Na konturze części można wyróżnić nieprzepuszczalne sekcje - zworki. Konstruując trajektorię program automatycznie generuje w tych miejscach polecenia włączenia i wyłączenia frezu oraz osadza odcinki dojazdu i odjazdu.
mosty pomiędzy częściami pozwala na obróbkę wielu części bez wyłączania palnika. Ustalanie punktów przejścia trajektorii z jednej części na drugą odbywa się po rozmieszczeniu części i jest brane pod uwagę przy konstruowaniu ostatecznej trajektorii frezu.
pętle zapewniają wysokiej jakości obróbkę narożników części i można je przypisać do dowolnego narożnika.
Przypisane przetwarzanie. Aby uprościć pracę, obróbkę części można zaprogramować już na etapie wstępnym, tak aby nie powtarzać tych samych czynności i wielokrotnie włączać elementy do gniazda.
Przetwarzanie ręczne Yu. Dla niestandardowych przypadków istnieje możliwość zbudowania trajektorii i ustawienia poleceń technologicznych w jawnej formie.
podprogramy zapewniają strukturę powstałego programu sterującego i zmniejszają objętość wygenerowanego tekstu.
Obróbka części za pomocą kombinowanego cięcia. Pary części ułożonych na arkuszu w odległości odpowiadającej szerokości cięcia można obrobić w jednym cięciu bez wyłączania plotera. Przy obróbce poszczególnych części wystarczy określić kontur części, która będzie obrabiana w pierwszej kolejności.
Wstępne dziurkowanie. Podczas obróbki grubych arkuszy może być konieczne najpierw wybicie otworów w arkuszu, a następnie wykonanie głównej obróbki. Do wstępnej obróbki blachy można zastosować oddzielny nóż lub wiertło. Program umożliwia wykonanie obróbki ze wstępnym wybiciem otworów. Możliwe jest ustawienie różnych metod przekłuwania wstępnego.
Pozycjonowanie nad materiałem. W niektórych przypadkach przy przechodzeniu od konturu do konturu konieczne jest przesuwanie frezu, omijając części i odpady oddzielone od arkusza. Funkcja ta jest niezbędna przy cięciu gumy piankowej. Czasami przy cięciu termicznym wymagane jest zabezpieczenie palnika przed kolizją z wyciętymi częściami i złomem. Program przewiduje możliwość takiego pozycjonowania z uwzględnieniem określonej odległości od detalu oraz od krawędzi arkusza.
Automatyczne przetwarzanie
Tryb automatycznego przetwarzania pozwala maksymalnie uprościć programowanie obróbki dużej liczby części. Sam program przypisuje kolejność omijania części na arkuszu i wykonuje obróbkę. Różne strategie unikania części zapewniają spełnienie wymaganych warunków obróbki.
Krawędzie tnące do spawania
Krawędzie tnące do spawania można wykonywać na maszynach do cięcia termicznego wyposażonych w bloki trzypalnikowe. Program zapewnia możliwość obróbki części zarówno ze stałymi, jak i zmiennymi fazowaniami. Stałe fazowanie charakteryzuje się stałością kątów przednich i tylnych oraz wysokości na całej długości. Faza zmienna charakteryzuje się równomierną zmianą kąta i wysokości na całej długości. Program automatycznie osadza w torze obcinacza specjalne sekcje – okna wejściowe w miejscach załączenia obcinaków bocznych oraz pętle cofania obcinaków, które zapewniają prawidłową orientację obcinaków bocznych i dotrzymanie niezbędnych warunków obróbki. Położenie okien wejściowych można zmienić za pomocą edytora graficznego.
Układ arkusza
Znakowanie na arkuszu można wykonać proszkiem lub rdzeniem. Kontury tyczenia można przechowywać w bazie danych wraz z częścią. W takim przypadku znaczniki są umieszczane na arkuszu wraz ze szczegółami. Aby zaprogramować działanie bloku znakującego wystarczy określić kontury znakujące w żądanej kolejności. Program dokona wszystkich niezbędnych przełączeń i zbuduje trajektorię.
Obróbka wielopodporowa
Na maszynach wyposażonych w wiele zacisków można wycinać wiele części jednocześnie. Program zapewnia automatyczne i ręczne rozmieszczanie części, biorąc pod uwagę możliwości takiego sprzętu. Podczas programowania przetwarzania wymagane okablowanie zacisków odbywa się automatycznie.
Wykorzystanie odpadów biznesowych
Z niewykorzystanej części arkusza powstają odpady biznesowe, które można umieścić w bazie danych w celu późniejszego wykorzystania.
Dokumentacja
Program generuje następujące dokumenty wyjściowe:
- wykres cięcia arkuszy
- specyfikacja cięcia blachy
- specyfikacja zadania cięcia.
Z reguły o konkretnym rodzaju dokumentów wyjściowych decydują tradycje przedsiębiorstwa. Generator raportów zawarty w Techtranie posiada elastyczny mechanizm dostosowywania formatu dokumentów i ilości informacji wyjściowych.
Automatyczne generowanie tekstu
W procesie konstruowania obiektów geometrycznych i projektowania wycinania arkuszy tekst programu powstaje w języku Tekhtran. Program uwzględnia całą sekwencję wykonywanych czynności i można go wykorzystać w dalszej pracy. Pozwala to elastycznie łączyć wygodę trybu dialogowego z zaletami tekstowej reprezentacji programu, do których zaliczają się:
- Wykorzystanie wcześniej napisanych programów i makr, ich szybka modyfikacja
- Parametryzacja części ogólnych
- Korzystanie z instrukcji warunkowych, pętli, wyrażeń arytmetycznych i funkcji
- Możliwość debugowania i naprawiania błędów
Narzędzia do tworzenia i debugowania programów
System zawiera zestaw narzędzi do pracy z programem w języku Tekhtran:
Polecenia wykonania(wykonaj instrukcję, przejdź do makra, uruchom program do końca, do kursora itp.) pozwalają na wykonanie i debugowanie programu w Tekhtran. Za pomocą tych poleceń można wykonać program w całości lub w częściach, zatrzymując proces w celu analizy wyników wykonania poszczególnych instrukcji.
Kontrola wykonania umożliwiają podgląd wartości zmiennych, wykorzystanie okna graficznego do wizualnej kontroli obiektów programu oraz przeglądanie informacji diagnostycznych generowanych podczas wykonywania programu.
Uzyskanie programu sterującego
Postprocesor wchodzący w skład Techtran umożliwia generowanie programów sterujących dla różnych maszyn CNC zgodnie z programem obróbki części i danymi sprzętowymi zawartymi w systemie. Wykorzystując program części uzyskany dla jednej maszyny, możliwe jest uzyskanie NC dla dowolnej innej maszyny z listy wyposażenia.
Dostosowanie do konkretnego sprzętu CNC
Techtran zapewnia możliwość dostosowania do konkretnego sprzętu CNC. Aby opisać sprzęt, należy wypełnić paszport maszyny i utworzyć moduł maszyny w specjalnym języku Techpost. Taki mechanizm pozwala użytkownikom samodzielnie uwzględniać cechy tworzenia UE, opracowując własne moduły w oparciu o istniejące.
Funkcje wersji 7:
Tryb automatycznego umieszczania za pomocą hodografu umożliwia:
- Umieść części na arkuszach i odpadach biznesowych o dowolnej formie
- Umieszczaj części dodatkowo na arkuszach, na których już znajdują się części, zwiększając wykorzystanie materiału
Kontrola przetwarzania
- Kontrola nadcięcia części podczas obróbki
- Monitorowanie ścieżki narzędzia poza arkuszem
- Sprawdzanie niedokończonych części
Zaawansowany mechanizm automatycznego generowania konturów odpadów biznesowych
Zwiększenie liczby konturów przy generowaniu odpadów biznesowych w trybie automatycznym
Łączenie sąsiadujących kawałków arkuszy odpadów biznesowych
![]() |
przetwarzanie wsadowe
Zaimplementowano przetwarzanie wsadowe – tryb pracy, w którym na układach arkuszy automatycznie wykonywanych jest szereg działań. Zadaniem przetwarzania wsadowego jest wykonanie sekwencji długotrwałych operacji, zaoszczędzenie użytkownikowi konieczności wielokrotnego otwierania obiektów bazy danych, a tym samym zmniejszenie ilości rutynowej pracy i zwiększenie wydajności.
W trybie przetwarzania wsadowego można wykonać następujące czynności:
- sprawdzenie prawidłowego położenia części na arkuszu
- automatyczna obróbka części
- sprawdzanie odebranej trajektorii pod kątem żłobków
- uzyskiwanie konturów odpadów biznesowych, map zagnieżdżeń, programów sterujących, statystyk przetwarzania, specyfikacji zagnieżdżenia arkuszy
- eksport części i ścieżek narzędzi
Obliczanie kosztów cięcia części
Kalkulacja pozwala określić koszt pracy za okres sprawozdawczy. Raport przedstawia koszt cięcia wyliczony na podstawie specjalnych tabel wypełnianych przez użytkownika. Można dostosować formuły obliczeniowe. Ocena kosztu rozwiązania uwzględnia:
- koszt ciętych arkuszy;
- koszt odpadów biznesowych;
- wartość złomu;
- koszt żużla;
- koszt w oparciu o:
- całkowity czas przetwarzania (obejmuje amortyzację sprzętu i wynagrodzenia personelu);
- liczba stempli (obejmuje zużycie dysz, gazów, energii);
- ścieżka/czas cięcia (uwzględnia zużycie dysz, gazów, energii).
- droga/czas pracy na biegu jałowym (uwzględnia zużycie gazów, energii).
Koszt liczony jest odrębnie dla każdego cięcia blachy.
Koszty można podsumować w celu uzyskania specyfikacji zadania cięcia.
Koszt można rozłożyć na części proporcjonalnie do ich powierzchni i obwodu.
Wzory obliczeniowe można dostosować indywidualnie do specyficznych wymagań przedsiębiorstwa.
Biblioteka kanałów
Opracowano bibliotekę elementów kanałów powietrznych składającą się z kształtek kanałów powietrznych (opcjonalnie).
|
Korzystanie z biblioteki umożliwia:
- otrzymać części o wymaganych właściwościach
- za pomocą okna podglądu wybierz optymalną kombinację tych parametrów, które nie są stałe (na przykład położenie linii cięcia przekroju walcowego).
- uwzględnić w detalu dodatkowe elementy łączące - fałdy.
- uwzględnić grubość blachy, aby skompensować odkształcenia jej powierzchni zewnętrznej i wewnętrznej powstałe w procesie gięcia.
- w razie potrzeby podziel część na kilka fragmentów
- wybierz elementy i przypisz parametry geometryczne i technologiczne w trybie dialogowym
- automatycznie generuje przeciągnięcia, biorąc pod uwagę promień zgięcia
- szybko przeglądaj i zmieniaj opcje wdrażania
- przeglądaj modele 3D powstałych połączeń
Korzystanie z biblioteki elementów kanałów umożliwi:
- skrócić czas projektowania rozwiercania
- wziąć pod uwagę cechy technologiczne połączeń elementów
- uzyskaj wysoką dokładność konstrukcji przeciągnięcia
- kontrolować geometrię budowanych przeciągów na etapie projektowania
Importowanie plików dstv (nc).
Import pozwoli Ci przenieść nie tylko geometrię części i jej oznaczenie, ale także liczbę części wymaganych do cięcia, wskazując grubość materiału. Programy obsługujące format DSTV(NC) - Tekla Structures, Advance Steel, StruCAD.
![]() |








