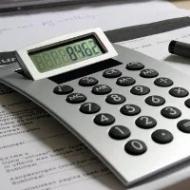
Accounting for finished products and semi-finished products of our own production. Accounting info Release of finished products using the Production Report for a shift
Earlier in my articles, I undeservedly ignored an important topic - reflecting the production of products from our own raw materials in 1C: Enterprise Accounting 8. But now we will consider this issue in detail: we will determine which document needs to reflect this operation, what transactions should be generated and how set up the write-off of materials according to specifications in 1C: Accounting.
So, to reflect the fact of production of finished products, you need to go to the “Production” tab and select the “Production reports per shift” item.
We create a new document, select a cost account (20.01 or 23, depending on whether the production is the main or auxiliary), then indicate the cost division (in our case it is simply called “Workshop”). You also need to select the warehouse where the products will be received.
We add new rows to the “Products” tabular section, select the product range, indicate the quantity and the planned price. Products are produced at planned prices, which will be adjusted when calculating the actual cost during the month-closing procedure.
The accounting account should be 43 (usually filled in automatically, you need to check the correctness of filling), in the “Nomenclature group” column, select the appropriate directory position. We leave the “Specification” column empty for now, we’ll talk about it a little later.
This document generates the posting Dt 43 Kt 20.01 in the event that the accounting policy does NOT indicate that it is necessary to take into account deviations of the actual cost from the planned one on account 40.
After conducting a production report for a shift, you can reflect the fact of sales of finished products to the buyer.
But another important stage of the production process is the disposal of materials. You can carry it out using the “Requirement-invoice” document, which is also located on the “Production” tab. But there is another option - indicate the list of materials used immediately in the document “Production report for the shift” on the “Materials” tab.
In this case, when posting the document, not only entries for the release of finished products will be generated, but also entries for the write-off of materials.
The "Materials" tab can be filled out manually each time, or you can create one or more specifications for each product, containing information about the name and quantity of materials required to produce a unit of product. To do this, in the “Nomenclature” directory, we find the desired product (or open it directly from the production report for the shift), click on “More..” and select the “Specifications” item.
We create a new specification and fill out the list of materials with quantities.
Now in the “Shift Production Report” document you can select a specification on the “Products” tab, and on the “Materials” tab click the “Fill” button. After this, the materials from the selected specification will automatically be included in the document, and the required quantity will be calculated based on the number of products produced. The program can create several specifications for each item. This may be true, for example, when interchangeable materials are used for production. Thus, the mechanism for writing off materials using specifications is quite convenient and can save a certain amount of time when working with production operations.
Accounting for semi-finished products of own production - postings their use and evaluation methods are relevant for those enterprises that have several stages in the production process and determine the cost of the resulting intermediate products. In this article we will talk about the features of accounting for semi-finished products and consider the corresponding transactions.
What is a semi-finished product?
There are various cost accounting methods. One of them is the cross-cutting method, which is used by material-intensive industries that produce large volumes of products, where raw materials alternately undergo several processing phases (processing stages). At the same time, at such enterprises, processing stages, along with types of finished products and cost items, are objects of accounting. There are two options for the cross-cutting method: unfinished and semi-finished. In the first option, costs are calculated by redistribution, but semi-finished products are accounted for only in quantitative terms, their cost is not calculated.
Enterprises using the semi-finished method of accounting record the amount and quantity of semi-finished products in accounting records, calculating their cost after each redistribution. Semi-finished products are accounted for separately, and their movement from processing stage to processing stage is documented by postings. This method is labor-intensive, but also provides some advantages:
- the ability to control the availability and safety of semi-finished products;
- the ability to monitor production costs at each stage (redistribution) in the manufacturing process;
- the ability to estimate profit/loss from the sale of semi-finished products (if there is such a need), since their cost is precisely known.
The definition of semi-finished products can be given depending on the industry in which the enterprise operates. In general, a semi-finished product of own production (hereinafter - PSP) is a product that has not undergone full processing, which will be brought to readiness in the following workshops of the enterprise or will be completed as part of the finished product (see, for example, the description of account 21 of the Chart of Accounts for the agro-industrial complex, approved by order of the Ministry of Agriculture of the Russian Federation dated June 13, 2001 No. 654). In terms of economic content, PSP are work in progress (clause 63 of the Regulations on accounting and financial reporting in the Russian Federation, approved by order of the Ministry of Finance of Russia dated July 29, 1998 No. 34n), but their feature is the presence of a certain degree of readiness and the ability to transfer to other structural divisions of the enterprise .
The use of PSP is typical for metallurgical, food, and chemical enterprises. Examples of PSPs include fruit purees, the concentrates of which are subsequently used to make juices; yarn that is used to make the material; blanks for the production of pipes, fittings that will be processed in other workshops, various parts for assembling any products: machine tools, children's toys, etc.
Accounting entries for accounting for semi-finished products
The chart of accounts of accounting, approved by order of the Ministry of Finance of the Russian Federation dated October 31, 2000 No. 94n, provides for a separate account 21 to reflect semi-finished products. If the accounting policy of the enterprise does not stipulate separate accounting for semi-finished products, then they are reflected as part of work in progress on account 20.
PSP is received at the warehouse by posting Dt 21 Kt 20 based on the invoice requirement (you can use form M-11 or develop it yourself). The transfer of PSP from the warehouse to further production is formalized by posting Dt 20 Kt 21 also on the basis of the invoice requirement.
If PSPs are sold externally, they appear in the form of finished products, so the sale operation is formalized by postings:
- Dt 62 Kt 90.1 for the amount of revenue;
- Dt 90.3 Kt 68 for the amount of VAT on revenue;
- Dt 90.2 Kt 21 for the amount of the cost of semi-finished products.
Methods for evaluating semi-finished products
Since semi-finished products are part of unfinished products, the methods for evaluating them are the same (subclauses 63-64 of the Accounting and Reporting Regulations):
- at the cost of raw materials and supplies;
- by direct cost items;
- at actual cost;
- at standard (planned) production costs.
With the first method, only the cost of raw materials and supplies falls in the cost account for semi-finished products. Let's look at an example.
Example 1
Neptune LLC produces parts for piston systems. These parts are used in our own production. This month, the production of parts of the “A” series required raw materials and supplies in the amount of 2,400,000 rubles. Workers' wages, including social contributions, amounted to 1,350,000 rubles, depreciation of equipment - 460,000 rubles. PSP are assessed by Neptune based on the cost of raw materials. The following entries were made in accounting:
Description |
Amount, thousand rubles |
||
|
|
||
The remaining costs are reflected in the cost of finished products |
|
69, 70, 02 |
|
|
|
20, subaccount “Production of semi-finished product “A”” |
|
Semi-finished products “A” are transferred to production |
20, subaccount “Production of products” |
21, subaccount “Semi-finished product “A”” |
With the second method of accounting, the cost of PSP includes only direct costs: raw materials, wages and social contributions, depreciation of equipment producing semi-finished products, and others. The company must list direct expenses in its accounting policies.
Example 2
Let's say Neptune LLC takes into account PSP using the second method. Then the data from Example 1 will be reflected in accounting as follows:
Description |
Amount, thousand rubles |
||
The cost of materials that went into the production of parts of the “A” series is reflected. |
20, subaccount “Production of semi-finished product “A”” |
||
Salary and social benefits are reflected. contributions, remaining costs in the cost of finished products |
20, subaccount “Production of semi-finished product “A”” |
||
Depreciation of equipment reflected |
20, subaccount “Production of semi-finished product “A”” |
||
Semi-finished products of series “A” were received into the warehouse |
21, subaccount “Semi-finished product “A”” |
20, subaccount “Production of semi-finished product “A”” |
When using the third method, the cost of PSP additionally includes indirect costs. Let's look at this with an example.
Example 3
Let's say Neptune LLC produces two types of PSP and accounts for them at actual costs. For semi-finished product “A”, let’s take the data from Example 1. Direct costs for the production of semi-finished product “B” amounted to 3,670 thousand rubles. (including the cost of raw materials and materials 1,860 thousand rubles). General business expenses (G&C) amounted to 1,640 thousand rubles. Neptune LLC distributes chemical and chemical products based on the cost of raw materials.
Total cost of raw materials: 2,400 + 1,860 = 4,260 thousand rubles.
Amount of OHR attributable to PSP “A”: 1,640 × (2,400 / 4,260) = 924 thousand rubles.
The amount of maintenance attributable to PSP “B”: 1,640 × (1,860 / 4,260) = 716 thousand rubles.
The data will be reflected in accounting as follows:
Description |
Amount, thousand rubles |
|||
The cost of direct costs for the manufacture of parts of series “A” is reflected |
20, subaccount “Production of semi-finished product “A”” |
02,10.1, 69, 70 |
||
The cost of direct costs for the manufacture of parts of series “B” is reflected |
|
02,10.1, 69, 70 |
||
The share of OHR attributable to PSP “A” is reflected |
20, subaccount “Production of semi-finished product “A”” |
|||
The share of OHR attributable to PSP “B” is reflected |
20, subaccount “Production of semi-finished product “B”” |
|||
Semi-finished products of series “A” were received into the warehouse |
21, subaccount “Semi-finished product “A”” |
20, subaccount “Production of semi-finished product “A”” |
||
Semi-finished products of series “B” were received into the warehouse |
21, subaccount “Semi-finished product “B”” |
20, subaccount “Production of semi-finished product “B”” |
||
If the method of reflection at actual cost is usually relevant for production with a small range of finished products, then the standard cost accounting method is used for mass and large-scale production.
It is necessary to separate purchased semi-finished products and PSP. The first are reflected on account 10, the second - using account 21 (semi-finished accounting method) or on account 20 (non-finished). The enterprise determines the method for assessing PSP depending on the specifics and scale of its production.
Accounting account 21 is the active account “Semi-finished products of own production”, used to record expenses associated with the production and processing of semi-finished products. Using standard postings and practical examples, we will consider the specifics of using account 21 and the features of reflecting transactions for accounting for semi-finished products of our own production
Semi-finished products of our own production are materials that have been processed at a completed technological stage. They can be used for subsequent processing at the same enterprise or can be sold to a counterparty for further processing.
At full-cycle enterprises, where raw materials go through several stages of processing or reprocessing, account 21 “Semi-finished products of own production” can be used to account for semi-finished products produced in each processing stage.
Semi-finished products of own production can be classified as work in progress (clause 63 of the Regulations on accounting and financial reporting No. 34n, approved by the Ministry of Finance on July 29, 1998). There are several methods of assessment:
According to the requirements of Article 319 of the Tax Code of the Russian Federation, the cost of semi-finished products of own production is determined based on the assessment of finished products. Therefore, in tax accounting only one assessment method is used:
- Direct costs of the enterprise.
The accounting policy must include a list of direct expenses (letter of the Ministry of Finance No. 03-03-06/4/78 dated August 26, 2010). For example, the list of direct expenses includes: material costs, labor costs, social contributions, accrued depreciation.
When calculating the cost of finished products, semi-finished products of own production are included in the calculation in the form of a complex item or are included in detailed cost items.
Account 21 in accounting
Semi-finished products of own production are accounted for on account 21 in correspondence with account 20 - when semi-finished products are used in own production, and with account 90 - when semi-finished products are sold to a counterparty:
The debit of account 21 reflects the receipt of semi-finished products and their surpluses discovered during inventory. The account credit takes into account the consumption of semi-finished products during transfer for subsequent processing, their sale or identification of shortages in the warehouse.
On account 21, analytical accounting can be maintained by storage location, by name, type, grade, and so on.
Get 267 video lessons on 1C for free:
Typical postings for 21 accounts “Semi-finished products of own production”
The main entries for 21 accounts used in accounting are shown in the table below:
Account debit | Account credit | Operation description |
21 | 20 | Receipt of semi-finished products of own production |
21 | 23 | Receipt of semi-finished products manufactured by auxiliary production |
21 | 40 | Receipt of finished products for subsequent use as semi-finished products |
21 | 91.01 | Surplus semi-finished products identified during inventory were capitalized |
20 | 21 | Semi-finished products are sent to production for subsequent processing |
23 (25;26) | 21 | The cost of semi-finished products is included in the costs of auxiliary production (overall production costs; general business expenses) |
28 | 21 | Write-off of defective semi-finished products of own production |
91.02 | 21 | The cost of semi-finished products of own production, written off or sold, is reflected in other expenses |
94 | 21 | The identified shortage of semi-finished products is reflected |
Examples of transactions on 21 accounts
Example 1. The cost of semi-finished products includes only the cost of raw materials and materials
Let's say VESNA LLC produces parts that are used in its own production. In January 2017, 150 parts were manufactured. The costs included:
Semi-finished products are valued at the cost of raw materials and supplies. Generated postings:
Dt | CT | Amount, rub. | Wiring description | A document base |
20 | 10 | 1 200 000 | Requirement invoice | |
20 | 70 (69); 02 | 1 430 000 | Costs (wages, social contributions, depreciation) for the production of finished products are reflected | |
21 | 20 | 1 200 000 | Semi-finished products are received into the warehouse | Shift production report |
20 | 21 | 1 200 000 | Semi-finished products transferred to production | Requirement invoice |
Example 2: Semi-finished products are valued at direct costs
Let's look at the previous example: VESNA LLC produces parts that are used in its own production. In January 2017, 150 parts were manufactured. Costs include:
- Raw materials and materials - 1,200,000 rubles;
- Salary and social contributions - 980,000 rubles;
- Depreciation charges - 450,000 rubles.
Semi-finished products of own production are valued at direct costs: raw materials and materials; salary; social contributions; accrued depreciation and so on, according to accounting policies. Generated postings:
Dt | CT | Amount, rub. | Wiring description | A document base |
20 | 10 | 1 200 000 | The cost of raw materials and materials written off for the manufacture of parts is taken into account | Requirement invoice |
20 | 70 (69) | 980 000 | The amount of salary and social contributions is reflected | Payroll. |
20 | 02 | 450 000 | Accrued depreciation reflected | Depreciation calculation. |
21 | 20 | 2 630 000 | Receipt of semi-finished products of own production to the warehouse (1,200,000 + 980,000 + 450,000) | Shift production report |
Example 3. The cost of semi-finished products of own production additionally includes indirect costs
Let's assume that VESNA LLC produces part 1 and part 2, which are used in its own production.
The direct costs for production of the part1 include:
- Raw materials and materials - 1,200,000 rubles;
- Salary and social contributions - 980,000 rubles;
- Depreciation charges - 450,000 rubles.
Direct costs for the production of parts2 include:
- Raw materials and materials - 1,050,000 rubles;
- Salary and social contributions - 950,000 rubles;
- Depreciation charges - 380,000 rubles.
General business expenses (G&C) for the production of semi-finished products, parts 1 and parts 2, amounted to 870,000 rubles. According to the accounting policy, VESNA distributes general business expenses relative to the cost of raw materials.
Posting table:
Dt | CT | Amount, rub. | Wiring description | A document base |
20 | 02; 10; 69; 70 | 2 630 000 | The cost of direct costs for manufacturing the part1 is taken into account (450,000 + 1,200,000 + 980,000) | Requirement invoice |
20 | 02; 10; 69; 70 | 2 380 000 | The cost of direct costs for manufacturing the part2 is taken into account (1,050,000 + 950,000 + 380,000) | Payroll. Depreciation calculation |
2 250 000 | Total costs for raw materials and supplies (1,200,000 + 1,050,000) | Accounting information | ||
20 | 26 | 464 000 | The share of OCR coming to part 1 is reflected (870,000 * (1,200,000 / 2,250,000)) | |
20 | 26 | 406 000 | The share of OCR coming to part 1 is reflected (870,000 * (1,050,000 / 2,250,000)) | |
21 | 20 | 3 094 000 | Semi-finished products part 1 (2,630,000 + 464,000) were credited to the warehouse | Shift production report |
21 | 20 | 2 786 000 | Semi-finished products part 2 (2,380,000 + 406,000) were credited to the warehouse |
It is important to note that the standard cost accounting method is advisable to use in the mass production of semi-finished products.
The correctness and timeliness of determining the cost of manufactured products is one of the key factors that creates competitive advantages of any production. Production accounting, implemented in programs based on 1C:Enterprise, not only allows you to quickly obtain complete information about the cost of manufactured products, but also calculate the profitability of the production itself. This data can serve as the basis for making management decisions, planning, attracting investments, etc.
Stages of production in 1C 8
The production of any type of product can be divided into several conditional cycles:
- Purchase and receipt of materials;
- Transfer of materials to production;
- Output;
- Calculation of the cost of finished products.
Today we will tell you in detail how in 1C production as a process is taken into account, as well as how all its stages are reflected. Our tool will be the most popular program of the 1C company - “1C: Enterprise Accounting 3.0”, and as an example we will use light industry, more precisely, the production of leather goods.
Creating a product range in 1C
Production accounting begins with determining the range of goods produced. To do this, in the 1C system, go to the “Directories” menu, then in the “Goods and Services” section, click on the “Nomenclature” indicator. When you click the “Create” button, the “Nomenclature (creation)” window pops up, in which you must alternately fill in the fields characterizing the name of the product, its full and short name, article number and unit of measurement. In the future, this will greatly simplify the accounting of our products. In our example, this is a black bag made of genuine leather.
After entering the nomenclature for at least one type of material into the system, the system activates the “Specification” tab.
In the most common sense, a specification is a document that states requirements. The specification of a manufactured product is an approved list of materials and accessories for tailoring a unit of product. In our example, the specification includes the following list of materials:
- Natural black leather/40 cm;
- Threads black/20 m;
- Long zipper/30 cm/1 piece;
- Short zipper/15 cm/1 pc.
Purchase and posting of materials in 1C
Production accounting in 1C must begin with determining cost estimates. Next, the purchasing department concludes a number of contracts for the purchase of necessary materials. Production accounting in 1C allows you to register all contracts, as well as invoices and invoices from suppliers in connection with specific contracts. To do this, in the “Purchases” section, select the “Invoice from supplier” or “Invoices received” tab.
After paying the invoice, accounting in 1C allows you to accept materials into the warehouse without re-entering the purchased list of goods into the system. 1C automatically posts to the debit of account 10 “Materials” from the credit of account 60 “Suppliers and contractors”.
Transfer of materials to production in the 1C system
The materials we need have appeared in the warehouse. Now 1C allows the generation of an electronic document “Demand-invoice”. Why do we need it? This document allows you to write off materials from the warehouse for production. We can find it in the “Production” menu. Next, using the “Create” button, enter information on the necessary materials, their quantity, and the write-off account.
Posting this document in 1C will formulate the posting of the write-off of materials (account credit 10) to production (account debit 20). An invoice requirement can be generated for one type of material or for all materials necessary for production. Please note that accounting in 1C allows you to write off for production only those materials that were previously credited to the warehouse, which creates additional control, both in terms of accounting for materials in the warehouse and the actual write-off for production. In turn, the correct choice of nomenclature will allow you to avoid writing off materials that are not directly related to this type of product. That is, if an organization, for example, produces two or more types of products, control using the “nomenclature” mode will avoid inaccuracies in accounting.
To sew a handbag, you need to write off the following materials for production:
- Genuine Leather;
- Threads;
- Accessories;
- Lining material.
These expenses form the variable costs of our production.
To reflect fixed production costs, it is necessary to uncheck the “Cost accounts” checkbox on the “Materials” tab in the “Request-invoice” document. This operation will allow you to create a new tab “Cost Account”. Since in our example the organization is engaged only in sewing handbags, all other costs associated with maintaining management personnel can be immediately written off to production.
Accounting for the release of finished products in 1C
Based on the results of the shift, a document “Production Report for the Shift” is created in the “Production” menu.
This document reflects the number of bags sewn per shift. To do this, click the “Create” button in the menu, then in the “Nomenclature” directory, select the type of genuine leather bags sewn per shift, set the quantity and the estimated planned cost (since the actual cost is calculated at the end of the month, after all routine operations). Please note that the document “Production report for a shift” can also be generated based on the “Requirement-invoice”.
Important! In this document, you need to select account 43 “Finished products”, and also link the specification of a specific type of bags, since they may differ in color, with other production costs being the same.
In the “Materials” tab, clicking the “Fill” button will allow 1C to automatically transfer from the specification all the necessary materials to the production of a unit of product, while the quantitative characteristics can be edited. At the same time, materials for production will be written off: leather, threads, accessories, lining material. This operation is accompanied by posting Debit 20 of the Main Production account/Credit 10 of the Materials account. Accounting in 1C allows you to simultaneously, when posting this document, generate a posting for the release of products from production: Debit to account 43 “Finished products” / Credit to account 20 “Main production”.
Calculation of the cost of finished products in 1C
The documents “Request-invoice” and “Production report for the shift” generate identical transactions for writing off materials for production (Dt-20 inc. Kt-10 inc.). In order not to write off the same materials twice for production, you need to post one of the specified documents - “Production report for the shift”, since in addition to writing off materials, it generates a posting for the release of products from production.
Calculation of the actual cost of finished products is carried out in 1C by carrying out a routine operation to close the month. To do this, in the “Operations” menu, you need to select the “Routine Operations” section. By clicking the “Create” button, a list of regulatory operations is generated: “depreciation of the cost of fixed assets”, “calculation of taxes”, etc. We choose to create an electronic document “Closing accounts 20, 23, 25, 26”. Let us recall that the debit of account 20 “Main production” reflects the costs attributed to production, and the credit accounts for finished products from production. The difference between the debit and credit of account 20 is the actual cost of the goods we produce.
Accounting for work in progress in 1C
Thanks to 1C, production accounting is significantly simplified and allows you to control the production process at each of its stages. However, please note that the end of the month and the conduct of routine operations do not always coincide with the production process, and at the end of the reporting period there may be work in progress. To solve this issue, accounting in 1C has been supplemented with the module “Inventory of work in progress”. The importance of this operation is due to the fact that accounting for work in progress is directly related to the financial results of the organization for the reporting period. In addition to fulfilling accounting requirements, periodic inventory of work in progress makes it possible to assess the quality of manufactured products, compliance with its nomenclature, and the presence of defects or surplus in production.
In order to correctly register work in progress accounting in 1C, you need to select the “WIP Inventory” section in the “Production” menu. The document is intended for recording balances by cost departments, as well as cost accounts. By clicking the “Create” button, we generate the electronic document “Inventory of work in progress (creation)”. Next, we sequentially fill in the document details: number, date, balance amount by item groups, etc.
When determining the cost of finished products, it may include the cost of the previous month's work in progress. It is important to remember that work in progress is products that have not passed all stages (phases) of production on a certain date. When accounting for work in progress, account 21 “Semi-finished products of own production” is also used.
Accounting for semi-finished products of own production in 1C
The use of account 21 “Semi-finished products of own production” in accounting is necessary for organizations that have established the production of semi-finished products as a separate production cycle; other companies keep records of semi-finished products as part of work in progress. The debit of this account in correspondence with account 20 “Main production” reflects the amount of actual costs for the production of semi-finished products, and the credit writes off the cost of used semi-finished products to the same production accounts.
The production of semi-finished products is documented in the “Shift Production Report” document, created in the “Production” / “Product Output” menu. The fields are sequentially filled in: write-off account (usually 20/1 “Main production”), the production unit that produced the semi-finished product, quantity, planned cost, accounting account 21 “Semi-finished products of own production”. Carrying out this document is the basis for accounting for semi-finished products in the warehouse.
Closing cost accounts in 1C
Closing cost accounts (20/21/25/26/29) is carried out by carrying out the routine operation “Closing the month”. If everything is relatively clear with direct costs (these are materials, wages of workers producing a specific type of product), then with overhead (indirect) costs everything is much more complicated. To correctly distribute indirect costs, the accountant needs to carefully work out and reflect in the “Accounting Policies” section the cost distribution method. As a rule, this distribution is proportional to either the output of finished goods or wages.
If the cost accounting method is incorrectly or incompletely reflected, the 1C system provides information indicating a specific error in the accounting policy, as well as a proposal for eliminating it.
Indirect costs are written off to account 20 “Main production” or immediately attributed to account 90 “Sales”. The closure of accounts for accounting for indirect expenses is carried out before the closure of account 20 “Main production”.
If the accounting for indirect costs is correctly set up, the amounts in accounts 25/26/29 will be distributed between the item groups of manufactured goods in proportion to the chosen method. In our example, the organization only sews a handbag, and therefore, all amounts of indirect costs are written off only for the production of this product. Account 20 “Main production” is closed with account 40 “Finished products”.
In conclusion, I would like to note once again that the accounting capabilities implemented in the 1C: Accounting program cover all stages of production and provide ample opportunities for control, analysis and tracking of their progress. Naturally, production accounting in the program we have considered is universal, and therefore somewhat “superficial” in nature. The most complete possibilities for automating accounting at a manufacturing enterprise are offered in such solutions as “1C: UNF”, “1C: Integrated Automation”, as well as for the largest industries – “1C: ERP”.
The production process can be divided into several intermediate stages (processing stages, stages). The completion of each of these stages is the release of a semi-finished product, which can be transferred for further processing or sold.
Cost accounting for each production stage can be carried out in two ways: unfinished or semi-finished. Selected option (Clause 7 PBU 1/2008).
Non-finished method of accounting
Under the unfinished method, the product produced as a result of a separate stage of the production process is not accounted for as a semi-finished product in a separate account. Its transfer for further processing is reflected only in physical terms (i.e. in kg, pcs., etc.). In this case, do not calculate the cost of the finished product. With this option, consider the costs as part of work in progress along with other costs (i.e., on account 20).
Direct costs that are directly related to production are reflected in the debit of account 20 in correspondence with the expense accounts. In this case, do the wiring:
Debit 20 Credit 10 (02, 05, 23, 29, 69, 70...)
First, record general production costs on account 25, and then at the end of the month write them off to account 20. At the same time, make the following entries:
Debit 25 Credit 10 (02, 05, 23, 69, 70...)
Debit 20 Credit 25
Consider general business expenses as part of production costs (i.e., on account 20) if they are not immediately included in the cost of products sold (i.e., are not written off to account 90 “Sales”). For more information, see . In this case, make the following entries:
Debit 20 Credit 26
All costs collected on account 20, as finished products are released, are written off from the credit of the account to the debit of the corresponding accounts (accounts 40 and 43). For more information, see How to reflect the release of finished products in accounting . The balance on account 20 will show the value of work in progress. For more information on accounting for work in progress, see How to determine the value of work in progress .
The advantages of the semi-finished method are that it is less labor-intensive. However, using it, the organization will not be able to control the costs of producing semi-finished products. This means constant control over the cost of finished products. In addition, if an organization decides to sell semi-finished products of its own production, difficulties will arise in determining their cost.
Semi-finished accounting method
The semi-finished method assumes that the produced semi-finished products are taken into account in quantitative and total terms, and their cost is calculated. In this case, accounting for semi-finished products is kept separately in a separate account. Despite the fact that this method is more labor-intensive, it has its advantages. Using it, it is possible to control the costs of production of finished products at each stage of production. In addition, if an organization decides to sell a semi-finished product, knowing its cost, it will be able to realistically assess the financial result of this operation.
In accounting, reflect the costs of producing semi-finished products on account 20 “Main production”, to which open a separate sub-account “Production of semi-finished products”.
Direct costs that are directly related to the production of semi-finished products are reflected in the debit of this account in correspondence with the expense accounts. In this case, do the wiring:
Debit 20 subaccount “Production of semi-finished products” Credit 10 (02, 05, 69, 70...)
- direct costs for the production of semi-finished products are taken into account.
General production costs are first recorded on account 25, and then at the end of the month write it off to account 20 . In this case, make the following entries:
Debit 25 Credit 10 (02, 05, 69, 70...)
- general production expenses are reflected;
Debit 20 subaccount “Production of semi-finished products” Credit 25
- general production costs are taken into account as part of the costs of producing semi-finished products.
General business expenses should be taken into account as part of the costs of producing semi-finished products (i.e., on account 20) if they are not immediately included in the cost of products sold (i.e., not written off on account 90 “Sales”). For more information, see How to write off general production and general business expenses . In this case, make the following entries:
Debit 26 Credit 10 (02, 05, 69, 70...)
- general business expenses are reflected;
Debit 20 subaccount “Production of semi-finished products” Credit 26
- general business expenses are taken into account as part of the costs for the production of semi-finished products.
This order follows from the Instructions for the chart of accounts (accounts 20, 25, 26).
Receipt from production
Receipts from the production of finished semi-finished products are accounted for in a separate account 21 “Semi-finished products of own production”. To capitalize semi-finished products, determine their cost. To calculate it use methods that are used to value work in progress :
- at the cost of raw materials and materials used in the manufacture of semi-finished products;
- by the amount of direct costs;
- at actual or standard cost.
The use of these methods is explained by the fact that semi-finished products are part of work in progress.
This procedure follows from paragraph 64 of the Regulations on Accounting and Reporting.
Document the receipt of finished semi-finished products from production by posting:
- semi-finished products of our own production were capitalized.
Do it on the basis of the invoice requirement in form No. M-11, which is drawn up when semi-finished products are received into the warehouse.
This procedure follows from the Instructions for the chart of accounts (accounts 21, 20) and paragraph 57 of the Methodological Instructions, approved by Order of the Ministry of Finance of Russia dated December 28, 2001 No. 119n.
Transfer for processing
Semi-finished products of our own production can be transferred for further processing or sold. Depending on these options, the procedure for reflecting the disposal of semi-finished products in accounting differs.
If semi-finished products are transferred to production for further use, make the following posting:
Debit 20 Credit 21
- semi-finished products were transferred to production.
Write-off methods
Determine the cost at which semi-finished products are written off from account 21 in one of the following ways:
- at the cost of each unit of inventory ;
- FIFO ;
- at average cost .
Method for estimating the value of write-off semi-finished productsfix in the accounting policy for accounting purposes .
Release of semi-finished products into production draw up the same primary documents as all other materials .
Such rules are established by paragraphs 73, 82 of the Methodological Instructions, approved by Order of the Ministry of Finance of Russia dated December 28, 2001 No. 119n, paragraph 16 of PBU 5/01 and the Instructions for the Chart of Accounts.
Sales of semi-finished products
Semi-finished products of own production intended for sale are finished products. Therefore, arrange their implementation in a similar order. For more information, see:
- What documents should I use to formalize the shipment of finished products (performance of work, provision of services) ;
- How to record sales of finished products in accounting .
When selling semi-finished products, make the following entries:
Debit 62 Credit 90-1
- revenue from the sale of semi-finished products of own production is reflected;
Debit 90-2 Credit 21
- the cost of semi-finished products sold is written off;
Debit 90-3 Credit 68 subaccount “VAT calculations”
- VAT is charged on the sale of semi-finished products (if such a sale is subject to VAT).
The procedure for accounting for expenses for the production of semi-finished products when calculating taxes depends on the taxation system that the organization uses.
BASIC
When calculating income tax, the costs of production of semi-finished products used in the manufacture of products include it as an expense in general .
If an organization uses cash method, then the proceeds from sales will be reduced by all expenses for which the conditions for their recognition in the tax base are met (clause 3 of Article 273 of the Tax Code of the Russian Federation). For example, expenses for the purchase of raw materials and materials used in the production of semi-finished products can be written off as expenses only if three conditions are simultaneously met: payment, release into production and use in it at the end of the month (subclause 1, clause 3, article 273, clause 5 Article 254 of the Tax Code of the Russian Federation).
If an organization sells semi-finished products, recognize the proceeds from the sale as income from sales (Article 249 of the Tax Code of the Russian Federation). Revenue is recognized upon receipt of payment for shipped semi-finished products (Clause 2 of Article 273 of the Tax Code of the Russian Federation). The advance payment (advance payment) received from the buyer should also be taken into account as part of income at the time of receipt (clause 2 of Article 273, subclause 1 of clause 1 of Article 251 of the Tax Code of the Russian Federation). This rule applies despite the fact that at the time of receiving the advance, the semi-finished products have not yet actually been transferred to the buyer (clause 8 of the information letter of the Presidium of the Supreme Arbitration Court of the Russian Federation dated December 22, 2005 No. 98).
If the organization uses the accrual method, indirect costs For the production of semi-finished products, write off the full amount in the period to which they relate (according to the rules of Article 272 of the Tax Code of the Russian Federation). A direct costs needs to be distributed. That part of them that relates to work in progress balances , finished products in warehouse or shipped (but not sold) products, the organization's operating expenses will not increase. This is provided for in paragraph 2 of Article 318 of the Tax Code of the Russian Federation.
The cost of semi-finished products that were not transferred for further processing at the end of the month, counted as part of work in progress for direct expenses (clause 4 of article 254 and article 319 of the Tax Code of the Russian Federation). Also calculate the cost of semi-finished products if the organization plans to sell them. In this case, determine their cost based on the direct costs of producing semi-finished products (clause 4 of article 254, article 319 of the Tax Code of the Russian Federation, letter of the Department of Tax Administration of Russia for Moscow dated October 23, 2003 No. 26-12/59541). When calculating income tax, take into account the cost of semi-finished products at the time of their sale (i.e., at the moment of transfer of ownership of them to the buyer) (clause 1 of Article 272 and subclause 2 of clause 1 of Article 268 of the Tax Code of the Russian Federation).
An example of reflection in accounting and taxation of costs for the production of semi-finished products
LLC "Production Company "Master"" is engaged in the production of snack products - crackers. The process of making crackers consists of two stages. At the first stage, in workshop No. 1, unspecified crackers are produced, which are accounted for as semi-finished products. Then they are transferred to workshop No. 2 for final production.
In June, production costs in workshop No. 1 amounted to:
- the cost of materials transferred to production is 400,000 rubles;
- cost of materials used - 370,000 rubles;
- amount of accrued salary - 240,000 rubles;
- the amount of accrued contributions for compulsory pension (social, medical) insurance and contributions for insurance against accidents and occupational diseases - 62,880 rubles;
- other expenses (general production and general economic) - 550,000 rubles.
In Master's accounting, semi-finished products are valued based on the amount of direct costs. Therefore, to determine their cost, the accountant allocated direct costs between semi-finished products produced and work in progress balances. The organization's accounting policy establishes that direct costs are distributed in proportion to the cost of materials attributable to finished products and work in progress.
The cost of unspecified crackers produced in workshop No. 1 was calculated by the accountant as follows:
- first determined the amount of direct costs (except for materials) - 302,880 rubles. (RUB 240,000 + RUB 62,880);
- then determined the share of these direct costs attributable to the produced semi-finished products - 280,164 rubles. (RUB 302,880 : RUB 400,000 × RUB 370,000).
The total amount of direct costs attributable to manufactured semi-finished products amounted to 650,164 rubles. (RUB 280,164 + RUB 370,000).
The accountant reflected the receipt of finished semi-finished products from workshop No. 1 as follows:
Debit 21 Credit 20 subaccount “Production of semi-finished products”
- 650,164 rub. - semi-finished products of our own production were capitalized.
In accordance with the accounting policy, the transfer of semi-finished products to production is carried out at average cost. In June, unspecified crackers in the amount of 487,623 rubles were transferred to workshop No. 2. At the same time, the accountant made the following entry:
Debit 20 Credit 21
- 487,623 rub. - semi-finished products were transferred for the production of finished products.
In tax accounting, the accountant did not take into account the transfer of semi-finished products, since the costs of their production will be taken into account only when selling finished products in the production of which these semi-finished products were used.
If an organization sells semi-finished products of its own production at retail and in the municipality in which the organization is registered, retail trade is transferred to the payment of UTII, this operation does not fall under this special tax regime (subclauses 6 and 7 of clause 2 of Article 346.26 of the Tax Code of the Russian Federation). This is explained by the fact that the obligation to pay UTII when selling goods at retail depends, among other things, on the type of property being sold. The sale of products of own production does not fall under UTII (paragraph 12 of article 346.27 of the Tax Code of the Russian Federation).
An exception to this rule is the sale of semi-finished products of own production through public catering facilities (cafes, restaurants, canteens, snack bars, bars). This type of service falls under UTII (Article 346.27 of the Tax Code of the Russian Federation, letters of the Ministry of Finance of Russia dated August 15, 2006 No. 03-11-04/3/376, dated August 23, 2006 No. 03-11-02-185, dated November 1, 2006 No. 03-11-04/3/482). In this case, the sale of semi-finished products is not subject to income tax and VAT (clause 4 of Article 346.26 of the Tax Code of the Russian Federation). As an object of taxation when calculating the single tax, take into accountimputed income (clause 1 of article 346.29 of the Tax Code of the Russian Federation). In addition, organize separate accounting of property, liabilities and business transactions in relation to the activities of the organization subject to UTII and the activities of the organization on the general taxation system for the purpose of calculating income tax And VAT(clause 9 of article 274, clause 7 of article 346.26 of the Tax Code of the Russian Federation).
simplified tax system
The procedure for accounting for income and expenses associated with the production and sale of semi-finished products depends on the object of taxation chosen by the simplified organization.
If an organization pays a single tax on income, expenses for the production of semi-finished products do not reduce the tax base (clause 1 of Article 346.18 of the Tax Code of the Russian Federation).
If an organization sells these semi-finished products, income from their sale will be taken into account when calculating the single tax (Clause 1, Article 346.15, Article 249 of the Tax Code of the Russian Federation). Recognize it in the period in which semi-finished products will be paid for. The date of receipt of income is the day the debt to the organization is repaid (the day money is received in a bank account or cash register, receipt of property, etc.). If a bill of exchange is received as payment, recognize income when it is paid or transferred endorsement to a third party. This is stated in paragraph 1 of Article 346.17 of the Tax Code of the Russian Federation.
If an organization pays a single tax on the difference between income and expenses, the costs of producing semi-finished products take into account in general regardless of which cost accounting method the organization uses (semi-finished or unfinished) (Article 346.16, 346.17 of the Tax Code of the Russian Federation).
If in the municipality in which the organization is registered, retail trade has been transferred to the payment of UTII, when selling semi-finished products of its own production at retail, this tax does not need to be paid (subclauses 6 and 7 of paragraph 2 of Article 346.26 of the Tax Code of the Russian Federation). This is explained by the fact that the obligation to pay UTII when selling goods at retail depends, among other things, on the type of property being sold. The sale of products of own production does not fall under UTII (paragraph 12 of article 346.27 of the Tax Code of the Russian Federation). An exception to this rule is the sale of semi-finished products of own production through public catering facilities (cafes, restaurants, canteens, snack bars, bars). This type of service subject to other conditions falls under UTII (Article 346.27 of the Tax Code of the Russian Federation, letters of the Ministry of Finance of Russia dated August 15, 2006 No. 03-11-04/3/376, dated August 23, 2006 No. 03-11-02-185, dated November 1, 2006 No. 03-11-04/3/482). In this case, the sale of semi-finished products is not subject to a single tax under simplification (clause 4 of Article 346.12 of the Tax Code of the Russian Federation). As an object of taxation when calculating UTII, take into account imputed income(clause 1 of article 346.29 of the Tax Code of the Russian Federation). Besides, organize separate accounting of property, liabilities and business transactions in relation to the activities of an organization subject to UTII and the activities of an organization on a simplified basis (clause 7 of Article 346.26 of the Tax Code of the Russian Federation).
UTII
The object of UTII taxation is imputed income for a specific type of activity of the organization (clauses 1 and 2 of Article 346.29 of the Tax Code of the Russian Federation). Therefore, expenses associated with the production of semi-finished products do not affect the determination of the tax base for UTII.
If an organization sells semi-finished products of its own production at retail, this operation does not fall under this special tax regime (subclauses 6 and 7, clause 2, article 346.26 of the Tax Code of the Russian Federation). This is explained by the fact that the obligation to pay UTII when selling goods at retail depends, among other things, on the type of property being sold. The sale of products of own production is not subject to UTII (paragraph 12, article 346.27 of the Tax Code of the Russian Federation). This means that in this case the organization must pay taxes in accordance with or (clause 7 of article 346.26 of the Tax Code of the Russian Federation). An exception to this rule is the sale of semi-finished products of own production through public catering facilities (cafes, restaurants, canteens, snack bars, bars). This type of service subject to other conditions falls under UTII (Article 346.27 of the Tax Code of the Russian Federation, letters of the Ministry of Finance of Russia dated August 15, 2006 No. 03-11-04/3/376, dated August 23, 2006 No. 03-11-02-185, dated November 1, 2006 No. 03-11-04/3/482).
OSNO and UTII
If an organization combines the general taxation system and UTII for semi-finished products used in activities transferred to UTII and activities on the general taxation system, it is necessary to organize separate accounting forincome tax And VAT (clause 9 of article 274, clause 4, 4.1 of article 170 of the Tax Code of the Russian Federation).
The cost of semi-finished products that relate to activities on the general taxation system will increase . The cost of semi-finished products spent in activities on UTII is not taken into account when taxing (clause 1 of Article 346.29 of the Tax Code of the Russian Federation).
The procedure for accounting for input VAT on the costs of producing semi-finished products also depends on the activity in which these semi-finished products are used. If semi-finished products are used in activities on the general taxation system, VAT can be deducted when compliance with the general conditions established by Article 171 of the Tax Code of the Russian Federation. If semi-finished products were used in activities on UTII, then VAT must be taken into account in their cost (clause 4 of article 170 of the Tax Code of the Russian Federation).
On the application of VAT deduction on the costs of production of semi-finished products, the purposes of which are initially unknown, seeHow to deduct input VAT when separately accounting for taxable and non-taxable transactions .
As a rule, it is always possible to determine which type of activity the costs of producing semi-finished products relate to. However, there may be situations where expenses relate simultaneously to two types of activities. In this case, distribute them in proportion to income (for income tax purposes) or in proportion to the share of transactions exempt from VAT (for VAT calculation purposes) (clause 9 of article 274, clause 4, 4.1 of article 170 of the Tax Code of the Russian Federation).