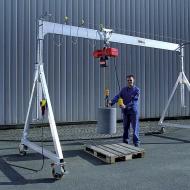
DIY crane. Secrets and nuances How to make a faucet with your own hands drawings
Almost any construction site cannot be done without special equipment, especially a construction crane. It becomes an indispensable assistant when it is necessary to lift heavy loads to different heights. Most people associate this technique with huge sizes, but there are many types of cranes that…
Almost any construction site cannot be done without special equipment, especially a construction crane. It becomes an indispensable assistant when it is necessary to lift heavy loads to different heights.
Most people associate this technology with huge size, but there are many types of faucets that are ergonomic and compact.
You can even do some options yourself, saving personal savings during construction. In this article we will look at how to assemble a homemade Pioneer crane for building a house.
Mini construction crane: scope of application
Mini cranes are in great demand. They are used during construction and repair work. Modern manufacturers offer innovative solutions in the manufacture of their products.
These devices are different:
- maneuverability;
- wide range of applications;
- functionality;
- ease of use.
Thanks to the presence of various attachments, various manipulations can be carried out with this technique.
Mini cranes, both purchased and assembled at home, are capable of working in the most difficult to reach places: in cramped courtyards, dense urban construction, uneven sites, inside buildings and on roofs. Compact dimensions allow special equipment to even pass through single or double doors.
They are often used for fine, almost jewelry work. Manufacturers of modern technology conducted an experiment with a matchbox that had to be moved from one place to another. At the same time, the device did not crush or crush a cardboard box of such a tiny size.
The presence of a control panel for the units allows users to control the work process while standing next to the equipment near the load, but only purchased units assembled in production have such advantages.
You are unlikely to be able to make such a device yourself. But you can try to build something similar. Of course, a mini crane assembled by yourself will not be very functional, but it will be able to lift loads of a certain mass to a specified height.
Simple mini-faucet with your own hands
If you make a mini crane with your own hands, it will be able to lift loads weighing up to 250 kg. This will greatly simplify the construction process on site. It can handle lifting logs, concrete mortar, and roofing materials. With it, you can do construction yourself without involving a large number of workers.
The main thing when making a mini crane is to prepare a drawing, the necessary tools and parts. The weight of this structure can reach 300 kg. It depends on what materials you will use during assembly. Despite its impressive weight, the mini crane will be distinguished by its compact size and high performance.
Assembling a mini crane with your own hands consists of the following steps:
- Using a gearbox, a cargo winch is attached to a worm base.
- Construction supports are the basis for screw outrigger systems.
- In addition to the basic structure, drums for winches will be required to assemble the unit. Making them on your own is quite problematic. Therefore, it is recommended to purchase ready-made products.
- Rotors from an electric motor can be used as a basis.
Attention: When assembling a mini crane yourself, special attention must be paid to the ratio of the sizes of the elements and the dimensions of the future device.
To make the device convenient to use, its platform can be equipped with wheels. This is where the old transport cart comes to the rescue.
Features of mini cranes assembled by yourself include:
- The optimal boom height is 5 meters. To make it yourself, you will need to use a pipe with a diameter of 8 cm.
- A profile of 2 corners is mounted on the base and a rotating mechanism is created to rotate the boom. An automobile hub from a truck is suitable as a turning mechanism.
- To build a counterweight, you don’t need any special materials. Ordinary bricks can serve as them.
Types of manual taps
All construction cranes are classified into:
- self-propelled;
- stationary;
- tower;
- special purpose.
This equipment is equipped with a boom extension mechanism, a cargo trolley, and a rotating support.
By type of movement they are divided into:
- stationary;
- adjustable;
- self-elevating;
- mobile.
According to the type of control, these devices are electrically driven and manual (mechanical).
Lift
Modern lifts are divided by type into:
- Foot. They are capable of lifting heavy loads weighing up to 2 tons to a height of 8 meters.
- Telescopic. Their advantages include: light weight and compactness. These devices are capable of lifting loads to a working height of up to 150 kg.
They, in turn, are divided into:
- self-propelled;
- non-self-propelled.
When choosing a lift, it is worth considering several factors: their dimensions, load capacity, scope of application.
To make a lift yourself, prepare materials and a preliminary drawing. To build it we will need:
- a winch, which can be made from a drum and a cable;
- pipes;
- electric drive
The advantages of construction hoists include:
- maneuverability;
- high load capacity;
- safety;
- ease of use.
Scissor crane
The scissor crane is a simple and easy-to-use design. Due to their versatility and functionality, these devices are used in installation and construction work. They can also often be found in supermarkets and warehouses.
A scissor crane lifts tons of loads every day. This technique, in addition to the construction industry, is regularly used in the maintenance of advertising billboards, facade signs, and elevators.
Their main advantages include:
- performance;
- high load capacity;
- compact dimensions when folded;
- wide range of applications;
- maneuverability.
Their advantages also include autonomy - they can operate on batteries. In addition, cranes can be equipped with different types of drives:
- electrohydraulic;
- diesel;
- electrical;
- hydraulic.
Most often, models with electric drives are used in construction. They are affordable, environmentally friendly and easy to use.
There are a large number of variations of devices of this type, but almost all of them consist of:
- lifting device,
- mobile platform;
- equal-speed drive wheels.
To build a scissor crane yourself, you will need to make the base and platform of the apparatus from a channel. To make scissors you will need:
- two-section distributor;
- bushings;
- pump;
- hydraulic cylinder;
- I-beams.
A DIY scissor crane is capable of lifting loads weighing up to half a ton. This device is installed on the UAZ, and after operation it is removed. The basis of the structure will be a thick square bolted to the frame, and the retractable pores will be held on the car bumper.
Crane “Pioneer”
The Pioneer type lift has excellent technical characteristics. It is light in weight and distinguished by maneuverability and mobility. The advantages of this device include the ability to quickly and easily assemble and disassemble.
To deliver the device to the construction site, it can be disassembled and folded into a simple gazelle. After work, it can also be easily disassembled and transported back. The crane can be installed anywhere: on the ground, in a pit, on a roof, on building floors.
This special equipment is produced by different companies in three main modifications of cranes, lifting capacity, and booms.
If necessary, you can make a Pioneer crane on your own, having with you the necessary consumables, tools, a well-drawn drawing and free time.
As for the scope of application of the Pioneer, it can be used to move various objects in any weather conditions. It is capable of delivering cargo to any floor or building structure. With its help you can deliver: tools, equipment, building materials and the like.
Quite often this device is used when installing roofs. With it you can quickly lift various loads, machines, metal structures, and materials.
Advantages of the Pioneer crane
The main advantages of the Pioneer crane include:
- ease of use - thanks to a simple and reliable design;
- the ability to assemble and disassemble the device within half an hour;
- mobility, allowing the unit to be used even at distant sites;
- low energy consumption.
Important: The Pioneer crane is capable of rotating the boom 360 degrees.
But this unit also has its drawbacks:
- it is capable of lifting a weight of no more than 1 ton;
- if you hang a flexible load on it, it is not always convenient and safe.
Do-it-yourself Pioneer crane
The Pioneer crane has a simple design. It consists of the following elements:
- Main support frame. It can be dismountable, bolted or standing on wheels. The second rotating frame is attached to it;
- Safety guy ropes, cargo ropes, electric drive;
- Swivel boom. It can be dismountable or bolted;
- End stop mechanism. It is located at the end of the boom;
- A limit switch located on the mechanism responsible for lifting the load.
So, if you have started construction on a personal plot, but there is no desire or financial opportunity to hire special equipment, try assembling a crane with your own hands. With it, you don't have to lift heavy loads yourself.
Attention: The Pioneer construction crane is a collapsible structure designed to lift loads. It can be used when digging a foundation pit for a house, installing a roof, or constructing walls at high altitudes.
The basis of the mechanism is a supporting running frame, which is installed either permanently or on a chassis. The part of the crane that rotates is installed on the frame. The boom can be rotated manually or electrically.
The load of this device is lifted using a winch, and stability is achieved thanks to a counterweight and turnbuckles (steel cable stays).
Materials and tools
To make the device, we will need the following materials, which can be found in the garage or in a specialized store:
- rectangular pipe;
- I-beam;
- telescopic unit for I-beam;
- small diameter cables;
- channel;
- electric motor;
- winch.
Tools you will need:
- keys;
- hammer;
- Screwdriver Set.
Design diagram
To make a Pioneer faucet with your own hands, you need to make a competent diagram. It should strictly indicate: materials of manufacture, dimensions of each individual element, methods of fastening parts.
When creating a diagram of a future design, it is worth carefully calculating everything. If you don’t quite understand this, it’s better to invite a specialist. Having a well-designed diagram in your hands, you can independently manufacture and assemble the device in the shortest possible time.
Assembly Features
As for the assembly of the product:
- The crane frame is assembled from a corner 63x63x5 mm.
- For a 5-meter boom, a pipe with a diameter of 5–8 cm is required.
- To strengthen the structure, you will need 2 corners, measuring 30x30x3 mm.
The carrying capacity of such a device will be 150 kg. If the ropes are strengthened, it will be possible to lift heavier loads.
Attention: Making an electric faucet at home is quite difficult. It will be more expensive and take longer.
When choosing an I-beam, you should make sure that it fits freely into the pipe. It will be installed on sliding guides, resulting in a telescopic unit.
In order for a homemade crane to function well, you will need to equip it with small diameter cables. They are best purchased at a specialty store. To weld the supporting structure and the rotating frame, it is necessary to use a channel.
Thanks to it, the crane will be well fixed to the surface. For safe operation of the device, it is recommended to weld the platform into a rectangle.
To start the lifting process, you will need to purchase an electric motor and connect it to a winch from the UAZ.
Attention: If you want the electric motor to start electrically, invite a specialized technician. Despite the fact that this procedure is not particularly complicated, for safety reasons it is better to use the services of a professional.
That's the whole process of assembling a Pioneer crane with your own hands.
Specifications
The manufacture and assembly of the Pioneer construction crane has a lot of positive aspects. Installing it on a construction site will help you save on the number of construction workers. With it you can lift roofing materials, timber, working tools and equipment to the required height.
After assembling the homemade device, you can familiarize yourself with its technical characteristics:
- The load capacity of the device can vary between 0.5–1 ton. It all depends on the materials used during assembly.
- The height of the crane will be 4 meters.
- The platform can rotate 360 degrees.
In conclusion, it is worth noting that when starting construction on a personal plot, in order to save money, try to assemble special equipment with your own hands. Of course, you will spend your free time on such manipulations, but you can save a lot. Even large construction companies do not always buy special equipment. They usually resort to renting units.
89942
We need a crane to build a private house, but renting one is expensive, so we make it ourselves!
Any user of forumhouse.ru will agree with the statement that one of the most necessary equipment during construction is a crane. The steel hero becomes an indispensable assistant when the need arises to lift a large load.
A lifting mechanism is usually associated with a huge structure tens of meters high. However, in private house-building, when compact mechanisms for construction come to the fore, one needs an option with a boom length not exceeding 5-7 meters.
But renting it is not a cheap pleasure, especially if the construction lasts for more than one month.
In this case, there is only one way out - roll up your sleeves and build a homemade mini-crane with your own hands. And our forum members will help you with this!
How to make a homemade faucet
Saving on your own health and trying to manually lift an unbearable load, especially if the construction of a house is carried out independently and without the involvement of hired labor, does not lead to good things. We have already told our readers how to build a vibrating table and vibrating plate on their own. Now we are making a crane with our own hands to build a house called “ mini-pioneer."
“Pioneer” is a mobile collapsible structure, with the help of which the load is lifted to a given height. So homemade The crane can be used when digging foundations and construction and installation work on building houses.
The basis of the mechanism is a supporting running frame, installed permanently or on a mobile chassis. The rotating part of the crane is mounted on the frame. The boom can be rotated manually or electrically. The crane design itself is made on a modular basis and can be disassembled into several parts for the convenience of moving the mechanism from one construction site to another.
The stability of the structure is ensured thanks to a counterweight and steel cable guys (turnbuckles), and the load is lifted using a winch and a block.
The experience of our forum member, who decided to build a mini “Pioneer” on his own, is interesting. He needed this construction mechanism to build a private house from timber.
Voldemort:
“I am almost single-handedly building a house from six-meter timber. It is impossible to lift and carry it alone. That is why I decided to assemble a mechanism in order to take the timber from the stack, place it at the sawing site and lift it to the plinth.
As the height of the building increases, our forum member plans to place a crane on the floor beams of the house.
A forum member assembled the frame from a corner 63x63x5 mm. The 5-meter-long boom was made from a pipe with a diameter of 50 mm. To strengthen the structure, two corners 30x30x3 mm were used. Also included in the plans Voldemora includes further extension of the boom by another 2 meters.
Voldemort:
– The lifting capacity of the mechanism is approximately 150 kg, but the design can lift more weight, and in order to achieve this, it is necessary to increase the multiplicity of pulleys.
Translated from Greek, Polyspaston means “tensioned by several ropes.” A chain hoist is a construction device for lifting loads. It consists of several blocks connected to each other by a rope or cable that goes around the blocks in a circle. A pulley block allows you to lift a load with less effort than the weight of the load.
The simplest pulley allows you to get a three-fourfold gain in strength; we should not forget that friction losses are inevitable in this system. Even in the best block models they reach 10%. And the more you gain in strength, the more the distance over which the equipment can move the load decreases.
Voldemort:
– It took me a week to make all the components and mechanisms. I spent another two days assembling and fine-tuning the mechanism. The swing drive and the boom lift drive are a six-fold manual pulley. The lifting drive is also a manual double chain hoist.
Voldemort notes that it would be much more convenient to control a mechanism with electric drives - to lift the load from a remote control on a long cord, as is done in industrial models. But in this case, the complexity of manufacturing all the mechanisms increases significantly, which will lead to an increase in the cost of the design and an increase in the time for manufacturing the crane.
The details of the device's manufacture are interesting.
Voldemort:
– As a turntable, I took two faceplates that I found at work. Basically, I assembled the mechanism from what was at hand. Instead of an axle, I welded a 30 mm bolt. I did not take a bolt made of high-strength steel, because such ones weld worse, do not stretch or bend, and immediately burst if their strength limit is exceeded.
All components of the device are lubricated with lithol.
To reduce the weight of the counterweight, the length of the support legs is 2 meters. When independently manufacturing and calculating the components of such a device, one point should be taken into account. The fact is that with a radius of the rotating faceplate of 200 mm and a distance of 2 meters to a counterweight weighing 100 kg, a tensile load of 1 ton acts on the central bolt. And this does not take into account the weight of the boom and the load being lifted!
It is also important to check the device for stability.
Voldemort:
– To begin with, let’s imagine that our crane is a single beam that rests on one support, and this support should be the shortest distance from the axis of rotation. Three forces act on the beam: the weight of the load, the weight of the counterweight and the mass of the mechanism. In order not to take into account the mass of the boom, I underestimated the weight of the crane by 50 kg. The calculation is approximate and simple, but it is better with it than without it at all.
Boom lift drum Voldemort Made from a tube with a diameter of 100 mm.
Voldemort:
– There is a nuance here - the drum cannot be placed close to the blocks. It needs to be shifted slightly along the axis towards the first block so that the second layer of cable is wound evenly.
A forum member made the blocks from three washers: two large and one small. All blocks are without bearings. It is important to ensure that the blocks bend well with the rope. That is, either the rope must be flexible, or the blocks must be of large diameter. Otherwise, when the boom is raised without load, the cables may fly out of the blocks.
Voldemort:
– My rope has a diameter of 12 mm, but it is very thick - there was simply no other way. If I extend the boom, I will install a more flexible cable with a diameter of 5 mm, because its working load is 150 kg, and its breaking load is 850 kg.
When designing block systems, it is important to understand how the chain hoist works and is calculated. Let's look at this using the example of a mini-pioneer.
Voldemort:
– The principle of operation of a pulley block is similar to the operation of a gearbox - you gain in strength, but lose in the length of the rope and, consequently, the speed of lifting the load.
In a gearbox, the main characteristic is the gear ratio, and in a chain hoist it is the multiplicity, i.e. the ratio of all rope branches to those running off the drum. If we have 6 sections of rope, it means the chain hoist is six-fold.
This means that the pulling load on the drum will be 6 times less than the weight of the load, and the rope itself, if it is designed for 100 kg, then rolled 6 times, will lift 600 kg.
Do-it-yourself construction mini-cranes
The design turned out to be so successful that many of our users decided to repeat it and even give the crane mobility by placing it on a Gazelle.
Forum member with nickname plumag proposes using a similar mechanism with a higher load capacity and equipped with electric drives to install concrete pillars. And in order to be able to transport such an individual crane on public roads, make the structure collapsible and partially and completely install it in the body at the site of the intended work. This will allow you to quickly recoup all costs associated with the manufacture of the device.
At FORUMHOUSE you can learn everything about building cranes yourself, and also get acquainted with the drawings of the mini-pioneer. The portal discusses everything you need to know to make a faucet from scrap metal. From concrete mixer to pipe bender. Forum members threads about making useful homemade crafts that will help you build.
Our video will tell you what tools you need to set up a carpentry workshop. See how to make A yourself in this tool, which will simplify work on your site near the country house.
A homemade crane for dismantling an engine, a photo of making a dismountable crane, and a video of testing a homemade product.
google_ad_client = "ca-pub-1974473278197966"; google_ad_slot = "3501064932"; google_ad_width = 580; google_ad_height = 400; ">
One day the idea arose to build engine removal crane car, since there is not much space in the garage, which means you need to make a collapsible one!
To build the crane I needed the following materials:
- Profile pipe 80 x 80 mm (wall 3 mm) - 7 meters.
- Pipe 89 mm - two pieces 0.7 meters long.
- Pipe 76 mm - two pieces 0.9 meters long.
- Jack - 5 t (Soviet production).
- Metal plates 8 mm thick - 4 pcs.
- Hook from towing strap.
- Wheels 2 straight, 2 swivel + 2 swivel with brake.
- Studs M 14 - 1000 mm.
Crane drawings.
Vertical stand.
Jack installation.
Lifting mechanism.
Tested my crane. I suspended a moped of 120 kg, then decided to climb onto the moped myself with another +120 kg - and again it seemed too little! But it is enough to dismantle the engine. I tried and lifted the Gazelle and took a video of the crane in action.
Hook lifting height:
From the ground with a short boom, the lower point is 90 cm, the upper 170 cm.
With a long boom - the bottom point is 80 cm, the top is 180 cm.
Long boom and unscrewed jack rod - bottom 140 cm and top 225 cm.
House and construction /
Users of the portal share their experience in building homemade lifts from simple to complex structures
When building a house from aerated concrete, timber, brick, etc. There is often a need to lift a load. For example, you need to “throw” blocks or wooden beams onto the second floor, lift bags of cement, or pour an armored belt. Doing this manually, even with the help of assistants, is not so easy - health is more expensive. Hiring a truck crane or manipulator for a small amount of work is expensive. The solution is to use a mini-crane, which, to reduce the cost of construction, is made by hand.
- How to make a lift for laying aerated concrete.
- What parts and tools are needed to build a mini crane.
- How to reduce the costs of building a universal lift.
Lift for laying aerated concrete blocks
Abroad, during the construction of private houses, cranes and various lifts are often used. This way construction goes faster, which means the “box” is cheaper, because It is more profitable to use small-scale mechanization tools than to hire laborers. Our developer relies on himself and often builds a house “with one helmet.” Therefore, the urgent question is how not to physically overstrain yourself when laying a wall from aerated concrete blocks weighing 35-40 kg.
An interesting variant of an unusual homemade “assistant” of the FORUMHOUSE user with the nickname Cross. First, let's show what he took as a basis.
German mini crane with retractable central post
A special feature of the lift is the original folding “arm-boom”, with the help of which the crane, moving on wheels, can reach two opposite walls.
I am building a house myself and, in order to be able to lay aerated concrete blocks, I built a lift according to the above model. The crane was made completely collapsible, except for the base. I didn’t measure the maximum load on the hook, but it easily lifts me (weighing 95 kg).
Technical characteristics of the lift:
- width – 2200 mm;
- height – 4200 mm;
- boom radius – 4200 mm;
- load capacity of electric hoist – up to 800 kg;
- total weight of the crane with ballast is approximately 650 kg;
- lift weight without ballast – about 300 kg;
- The maximum lifting height of the masonry block is 3500 mm.
The working height of lifting blocks is adjustable in two ranges. The first is 1750 mm. The second is 3.5 m, for which the structure is raised, sliding upward along the supporting “legs” using a hydraulic jack lined with spacers made of GB blocks.
To make the lift, the user needed:
- swivel wheels;
- profile pipes for the mast, “legs” and boom with a section of 12x12 cm, 12x6 cm, wall 6 mm;
- pipe-jibs – 63x3 mm;
- powerful gate hinges;
- The boom rotating mechanism is made of ST45 steel and “205” bearings.
During operation, the design was modified. For example, the user laid the cable for the winch in a corrugated pipe and extended the cable for the control panel.
The design has a number of shortcomings that I would like to correct. For example, I’m thinking about making wireless control, replacing the gate hinges with bearings. Increase the number of “joints” in the boom at the same reach. Instead of a temporary counterweight - bags of sand concrete, pour concrete ballast.
Important nuance: in order for the lift to move around the construction site or, for example, over the concrete slab of the second floor, it is necessary to keep the workplace clean, because GB fragments and debris interfere with the relocation of the tap.
The design of the unusual lift attracted the interest of portal users.
With such a lift, I think, as they do in Germany, you need to make masonry from blocks larger than standard ones. The length and height are 2-3 times greater than a regular GB. The crane has enough lifting capacity, and the laying speed will increase significantly.
According to Cross, he heard that someone on the portal had already tried to order blocks of 1x0.4x0.6 m format from a gas silicate manufacturer. But it turned out that this was not profitable for the plant, because it is necessary to reconfigure the line for the production of GB, but for the sake of a small volume (for an ordinary private house) they will not do this.
I'm wondering: is the work on site easier when using a crane? What work can be done with it and what cannot?
There is no need to install scaffolding when laying GB walls. The lift can be assembled and disassembled. I poured the concrete lintels over the windows the old fashioned way, from buckets, because... The volume is small, and it’s easier to do it with one assistant.
Grand total: The mini-crane turned out to be successful, and with some modifications to its design, the lift can be put into small-scale production.
Mini crane made from scrap metal
Another version of a lifting mechanism made of metal “lying under your feet” was made by a portal participant with the nickname Peter 1.
According to Peter 1, The reason for building a crane is that the house is getting higher and higher, and the blocks and concrete are getting heavier. Therefore, after revising the “unnecessary things”, the user manufactured a completely dismountable crane with a lifting capacity of 200 kg.
I think my crane can lift more, but I didn’t overload it. The crane can be disassembled into parts weighing 30-60 kg and can be easily transported in a car trailer. I carry an arrow on the trunk. Statically tested a structure weighing 400 kg. I usually lift up to 150 kg. This is quite enough for my construction needs.
At one time, the crane, with a boom reach of 5 m, lifts 10 blocks weighing 15 kg each, or four 15-liter buckets of solution.
The design of the crane is a hodgepodge of what was at hand. Let's list the main details:
- swivel unit - truck hub;
Hubs from cars, trucks, and farm equipment are often used to make the swivel assembly in homemade cranes. The main thing is to calculate the loads acting on it and the fasteners.
- the boom is made of a pipe with a diameter of 75 mm;
- outriggers and base - a rectangular pipe with a section of 8x5 and 8.5x5.5 cm;
- the base of the tower is the “200th” channel;
- worm gearboxes for boom and cargo winches.
- three-phase electric motor with reverse, power 0.9 kW, converted to power from a 220 V network;
The crane turned out to be mobile, and by lowering the boom, it can be moved from place to place, rolling on wheels along compacted soil. Level adjustment is carried out using screw supports.
Metal, gearboxes and rollers were purchased at a recycled metal shop. Only the cable and bearings are new.
The weight of the crane without counterweight is about 250 kg. The cost of the structure, taking into account the purchase of consumables - cutting discs for angle grinders, electrodes for a welding inverter and paint, is 4 thousand rubles.
Crane, + time for turning, + selection of components and fitting of components, I completed it in 3 working days. In the future, after finishing the work, I will completely disassemble it.
Inexpensive mini lift
Practice shows that when building a private house, a real crane is not always needed. Often, a developer can get by with “little expense” and make a small lift based on an electrically driven hoist.
My design is simpler than the authors above, but it suits me quite well. I bought a hoist with a load capacity of 300 kg without a block and 600 kg with a block. Tests have shown that the device can lift a load weighing 250-270 kg, then the engine protection is triggered. During the construction season, I used it to lift about 40 pallets with building blocks, a 6-meter beam for the mauerlat, rafters, mortar for masonry and concrete for the reinforced belt.
The lift, again to save money, is made from used pipes, angles and channels.
All rust was cleaned off with a grinder, and the pipes were sprayed and then painted with paint with a rust reducer.
In order to be able to assemble the lift on the ceiling of the second floor, all components (where welding is not needed) are made collapsible - with bolted connections.
A hoist is installed on the stand using clamps.
In case of rain, a plastic bottle with the bottom cut off is placed on the control panel.
The telpher covers a canopy made of used roofing iron.
When lifting a pallet, two boards are placed under it, and the pallet is lowered onto them.
The entire structure is fixed to the floor with clamps.
Drawing with dimensions of the lift.
As a result, the user has a universal, self-manufacturing and budget “helper” that greatly simplifies the work of building a house.
These are topics that describe in detail how to make a lift for aerated concrete, and provide dozens of options for mini-cranes, from simple to the most complex designs.
Also useful articles: a homemade mini-crane “Pioneer”, features of manual arc welding and the choice of a welding inverter, as well as a homemade mini-tractor with a hydraulic drive.
In the video - how to build a house from aerated concrete without hired workers.
Source of material
A do-it-yourself crane will always come in handy on the farm for anyone who has a summer house or those who live in a private house. It will be especially needed by those owners who are not afraid of various independent construction and repair work. Renting such equipment, let alone purchasing it, will cost a considerable amount. And making a crane with your own hands is actually quite simple - you will learn about this in this article. Try to understand the proposed instructions step by step, performing all the work, and you will get an excellent tool for household use.
Manufacturing
For further work you will need the following materials:
- Worm gearbox (electric drive must be 600 W).
- Construction supports.
- Secondary materials and tools for construction and repair.
Progress
Most of the necessary and useful tools can be made independently, thereby saving the family budget. In general, such a structure is assembled very simply and as quickly as possible. The algorithm described below will help even an inexperienced master. The main thing is to select all the necessary parts and working tools for the future structure.
Important! Ultimately, the resulting structure will weigh approximately 250-300 kg. At the same time, it will be quite compact. A self-built crane will not have a very high lifting capacity (approximately 200 kg), however, it will be more than enough for most home construction or renovation work.
Let's move on to the algorithm for making a mini-faucet with your own hands:
- Our mechanism will have 2 bearings. There will be a support bearing in the upper part between the housing and the base. Below is a simple radial bearing. The inner diameter of the housing, as well as the outer diameter of the base, is calculated for the lower bearing.
Important! Both parts must fit tightly into the bearing. Thus, both parts are connected.
- In order to more reliably fix the radial bearing, a nut is screwed onto the housing from below, the thickness of the threaded and supporting parts of which must be at least 3 mm.
- Next, this unit is attached to the platform with a bolt, which will attract the base to the platform. So you will get the following design: the platform with the base will be stationary, and the body with the nut will rotate.
Important! To tighten the bolt that will be attached to the base of the platform, you will need a spanner wrench with an extension, as well as two washers - a Grover and a flat one.
- It's time to move on to making a mini-crane stand with your own hands. Its height should be up to your waist. In order to make it, you need a piece of pipe and 4 pieces of channel. You can trim the end of the pipe evenly by using a car clamp and tightening it on it, then cut an even circle with a grinder.
- Next, a rotating mechanism platform is welded to the cut end, which must be ordered based on the dimensions of the pipe you have chosen.
- Next we move on to making the legs. They are welded in such a way that the stand itself does not collapse.
- Now you can move on to hanging the pipe with the already welded platform. The rope is passed through the hole in the center of the rotating mechanism platform, and the legs are placed diagonally towards the pipe. Thus, the pipe should hang evenly, and the legs should rest on it on all four sides.
- After finding the balance of the crane with your own hands, the corners of the channels abutting the pipe are outlined by eye and trimmed with a grinder.
- Next, they move on to making a support cross and attaching it to the legs using nuts. It is usually made from various rigid profiles.
- After this, they move to the crane platform, where there will be a counterweight, as well as a boom and a winch. The platform is attached to the rotating mechanism body using four bolts.
Important! As a platform, you can use a 1.5-meter I-beam, the width of which will be approximately 18 cm.
- Let's move on to the block of counterweights - it is usually made from pieces of channel material, but other options are also acceptable. Ultimately, the most important thing is the quality of the resulting cargo container.
- The winch is usually installed with a capacity of 0.5 tons, with a brake.
- All that remains is to make a boom for the crane with your own hands. It is always made of timber, a mount with a shaft and a tip with a pulley.
- The mounting body is made from a piece of channel material, and for the shaft, for example, a piece of the rotor shaft from some old engine is suitable. After this, it is bent in a vice, and two brackets are attached around it, after which it is fixed to the fastening body, which will later be inserted into the prepared beam.
- Purchase ordinary bearings that will fit tightly onto the shaft. A seat is cut out in the mounting body.
- The bearings are secured in the housing.
- The beam is attached to the channel with ties made from a metal strip, the thickness of which is approximately 3 millimeters.
- A pulley for the cable is attached to the end of the boom.
- Next, the arrow is assembled, having previously strengthened it.
- After this, they proceed to assembling the entire crane platform with their own hands. A winch is installed on it, a block of counterweights is installed under the winch, and on the other side there is a boom lift housing with a boom.
Important! The entire assembly must be carried out in a lying position, and when completed the structure must be raised so that it is in an upright position on some support.
- The rotating mechanism is attached to the rack, after which a platform is installed on it so that the boom and counterweight are in balance.
- The assembled crane platform is suspended and raised so that it is possible to place a stand under it.
- Raise the platform using a winch. To do this, its cable is passed through a block and hooked to the boom lifting body located at the other end of the platform.
- The platform is raised using a winch.
- Having hung it in this way and placed a stand under it, they find a position where the counterweight balances the arrow.
- In this position, four through holes are drilled and the platform is bolted to the rack.
Throughout the long history of its existence, man has more than once been faced with the task of lifting and moving heavy objects in space. For example, the familiar Egyptian pyramids consist of massive stone blocks that no one can lift. Therefore, one of the greatest achievements of mankind is the invention of the lifting crane, which made it possible to significantly simplify the task of moving heavy loads and speed up the construction of houses and other objects.
Machine structure
The operating principle of a crane is based on the physics of simple mechanisms. The simplest version of the crane is a stick placed on a fulcrum in such a way that the free ends have different lengths. Now if you hang a load on a short lever, it will take less effort to lift it. The most common design is one that uses, in addition to levers, a system of blocks.
A do-it-yourself crane is an indisputable assistant in small-scale construction. When constructing a private house, the use of bulky industrial cranes is not required. The height of the houses rarely exceeds 2 floors, and the weight of the lifted load is 200 kilograms.
Although there are many variations of lifting mechanisms, a classic crane consists of the following parts:
- An arrow with a block attached to its end. Depending on its length, the height to which the load can be lifted is determined.
- Platform. The boom and counterweight are attached to it. It is the main part of the crane and is subject to significant loads. Therefore, when manufacturing a platform, it is important to pay special attention to its strength.
- Counterweight. Serves for crane stability. Defines the maximum load weight that the crane can lift. Stackable counterweight options are available to provide maximum stability.
- A guy wire connecting the boom and the counterweight. Allows you to adjust the tilt of the boom and move the load in both vertical and horizontal planes.
- Winch with cable. It is the lifting mechanism itself. The power of the winch determines how much weight the crane can lift.
- Stand with a rotating mechanism. It is necessary to turn the crane to the sides.
- The support cross, which is the base of the crane. Sets the stability of the entire structure. When manufacturing it, you should also pay attention to its strength.
terms of Use
To operate lifting mechanisms safely, certain rules must be followed.
These rules apply to any lifting device:
- The load capacity must not be exceeded. A load that is too heavy may damage the device.
- The base must be stable. Homemade lifting devices should be located on a previously prepared hard horizontal surface.
- In bad weather conditions, you should also refrain from working with the crane. Strong winds will throw the crane off balance, and poor visibility may make it difficult to see people under the boom.
- Before operating a crane or lifting device, it is necessary to conduct an external inspection to identify any malfunctions. If malfunctions are detected, operation of the crane is prohibited.
- It should be remembered that when working with the lift, you should not make sudden movements. The load must be lifted smoothly. And most importantly, do not stand under any lifted load.
What characteristics should a garage lift have?
In garage conditions, two types of lifting mechanisms are used. The first type includes a lift that can lift the entire car, and the second type includes a goose-type lift that allows you to move loads around the garage.
Lifts of the first type are stationary devices and the main requirement for them is stability. The car weighs more than a ton and should not have the slightest chance of falling. In order to prevent any accidents, the garage lift must have a reliable stopper.
The goose type lifts are most often used in auto repair shops. It is quite simple to make it from a profile pipe or channel. First, the base is welded on which the rotating mechanism needs to be installed. It is best to make an arrow with an adjustable reach. This will make it possible to move weights in any direction.
How a simple block design works
The pulley system or pulley system has been known to mankind since ancient times. The classic system design consists of pulleys and cable. One pulley is called a block. Depending on the method of fastening, the pulley can be movable or fixed:
- Fixed block. It is attached to the support and plays the role of changing the direction of movement of the rope. Does not provide any gain in strength.
- Movable block. It is located on the side of the load and gives a gain in strength.
The principle of operation of a pulley block is similar to the principle of operation of a lever in the physics of simple mechanisms. The role of the lever in this case is played by the cable itself. In the case of a simple block of two pulleys, the movable pulley divides the rope into 2 parts and in order to lift the load the same distance, a rope twice as long will be required. The work of lifting the load is performed in the same volume. And the effort, due to the fact that the length of the rope has become twice as long, becomes half as much.
If there are more than 2 pulleys in the system, the gain in strength is approximately equal to the number of blocks. In the case of 3 blocks, the effort will be 3 times less, and 4 blocks will require only a quarter of the original effort.
Complex block system how to calculate power gain
If the system is designed in such a way that one simple pulley pulls another simple pulley, then this is already a complex system of blocks. To theoretically calculate the gain in strength, it is necessary to conditionally divide a complex chain hoist into simple ones and multiply the values of the gain from simple chain hoists.
For example, if the system consists of 4 blocks, and the first conditional simple pulley has a gain of 3. It pulls the second simple two-block pulley, also with a gain of 3. The total force that will need to be applied will be 9 times less. It is the 4-block complex chain hoist that is most often used by rescuers.
Methods for attaching a rope to a lifting mechanism
When creating complex pulley blocks, there are often situations when a cable of the required length for attaching the moving block is not at hand.
Methods for attaching a cable using general-purpose rigging:
- Using a cord. Using a self-tightening knot, the cord is tied to the main cable. As the load is lifted, the grappling knot moves along the main rope, thereby allowing the height of the load to be increased.
- Using clamps. In the case of using a steel cable, it is not possible to use a cord, so it is necessary to use special clamps.
We create a simple lifting mechanism with our own hands
Construction of a crane is not a quick task and is justified if it is required frequently or the volume of work is large enough. In cases where the load needs to be lifted urgently or this is a one-time operation, you can use improvised means.
To create a simple lifting device you will need a cord and two blocks. One block and the end of the rope are fixed motionless on the support. This will be the highest point to which the load can be lifted. We attach the second block to the load using slings or a hook. We first pull the rope along the block attached to the load, then pass it through the upper block. The gain in power will be 2 times. Using your own weight, you can easily lift a load weighing 100 kilograms to the required height.
If you add the ability to move the upper block along a guide, for example along a rail, you can get a do-it-yourself jib crane. It is useful in garage conditions for moving heavy machine parts.
It should be remembered that when working with the lift, you should not make sudden movements. The load must be lifted smoothly. And most importantly, do not stand under any lifted load. The same rule applies to a crane - standing under the arrow is prohibited.
Materials and tools
The most important thing when making a crane is to use high-quality tools and materials. This will guarantee that the structure will be strong and safe.
The cable should have minimal stretch; this will give a greater gain in strength when using a pulley system. The fittings used for tying must be taken only from metal. Plastic fittings cannot withstand heavy loads and break at the wrong time. To fasten individual parts of a homemade crane, you should choose high-strength hardware products.
If a winch is intended to be used, its lifting capacity should not be less than 500 kilograms. The best choice would be winches that can lift a load weighing 1 ton or more.
In conclusion, I would like to once again remind you of the need to observe safety precautions when working with lifting mechanisms. Also, regardless of whether the crane is purchased or made by yourself, you should inspect it before starting work.
When building a house from aerated concrete, timber, brick, etc. There is often a need to lift a load. For example, you need to “throw” blocks or wooden beams onto the second floor, lift bags of cement, or pour an armored belt. Doing this manually, even with the help of assistants, is not so easy - health is more expensive. Hiring a truck crane or manipulator for a small amount of work is expensive. The solution is to use a mini-crane, which, to reduce the cost of construction, is made by hand.
- How to make a lift for laying aerated concrete.
- What parts and tools are needed to build a mini crane.
- How to reduce the costs of building a universal lift.
Lift for laying aerated concrete blocks
Abroad, during the construction of private houses, cranes and various lifts are often used. This way construction goes faster, which means the “box” is cheaper, because It is more profitable to use small-scale mechanization tools than to hire laborers. Our developer relies on himself and often builds a house “with one helmet.” Therefore, the urgent question is how not to physically overstrain yourself when laying a wall from aerated concrete blocks weighing 35-40 kg.
An interesting variant of an unusual homemade “assistant” of the FORUMHOUSE user with the nickname Cross. First, let's show what he took as a basis.
German mini crane with retractable central post
A special feature of the lift is the original folding “arm-boom”, with the help of which the crane, moving on wheels, can reach two opposite walls.
Cross
I am building a house myself and, in order to be able to lay aerated concrete blocks, I built a lift according to the above model. The crane was made completely collapsible, except for the base. I didn’t measure the maximum load on the hook, but it easily lifts me (weighing 95 kg).
Technical characteristics of the lift:
- width – 2200 mm;
- height – 4200 mm;
- boom radius – 4200 mm;
- load capacity of electric hoist – up to 800 kg;
- total weight of the crane with ballast is approximately 650 kg;
- lift weight without ballast – about 300 kg;
- The maximum lifting height of the masonry block is 3500 mm.
The working height of lifting blocks is adjustable in two ranges. The first is 1750 mm. The second is 3.5 m, for which the structure is raised, sliding upward along the supporting “legs” using a hydraulic jack lined with spacers made of GB blocks.
To make the lift, the user needed:
- swivel wheels;
- profile pipes for the mast, “legs” and boom with a section of 12x12 cm, 12x6 cm, wall 6 mm;
- pipe-jibs – 63x3 mm;
- powerful gate hinges;
- The boom rotating mechanism is made of ST45 steel and “205” bearings.
During operation, the design was modified. For example, the user laid the cable for the winch in a corrugated pipe and extended the cable for the control panel.
Cross
The design has a number of shortcomings that I would like to correct. For example, I’m thinking about making wireless control, replacing the gate hinges with bearings. Increase the number of “joints” in the boom at the same reach. Instead of a temporary counterweight - bags of sand concrete, pour concrete ballast.
Important nuance: in order for the lift to move around the construction site or, for example, over the concrete slab of the second floor, it is necessary to keep the workplace clean, because GB fragments and debris interfere with the relocation of the tap.
The design of the unusual lift attracted the interest of portal users.
Konstantin Y. Member of FORUMHOUSE
With such a lift, I think, as they do in Germany, you need to make masonry from blocks larger than standard ones. The length and height are 2-3 times greater than a regular GB. The crane has enough lifting capacity, and the laying speed will increase significantly.
According to Cross, he heard that someone on the portal had already tried to order blocks of 1x0.4x0.6 m format from a gas silicate manufacturer. But it turned out that this was not profitable for the plant, because it is necessary to reconfigure the line for the production of GB, but for the sake of a small volume (for an ordinary private house) they will not do this.
Vegaroma FORUMHOUSE Member
I'm wondering: is the work on site easier when using a crane? What work can be done with it and what cannot?
Cross
There is no need to install scaffolding when laying GB walls. The lift can be assembled and disassembled. I poured the concrete lintels over the windows the old fashioned way, from buckets, because... The volume is small, and it’s easier to do it with one assistant.
Grand total: The mini-crane turned out to be successful, and with some modifications to its design, the lift can be put into small-scale production.
Mini crane made from scrap metal
Another version of a lifting mechanism made of metal “lying under your feet” was made by a portal participant with the nickname Peter 1.
According to Peter 1, The reason for building a crane is that the house is getting higher and higher, and the blocks and concrete are getting heavier. Therefore, after revising the “unnecessary things”, the user manufactured a completely dismountable crane with a lifting capacity of 200 kg.
Peter 1
I think my crane can lift more, but I didn’t overload it. The crane can be disassembled into parts weighing 30-60 kg and can be easily transported in a car trailer. I carry an arrow on the trunk. Statically tested a structure weighing 400 kg. I usually lift up to 150 kg. This is quite enough for my construction needs.
At one time, the crane, with a boom reach of 5 m, lifts 10 blocks weighing 15 kg each, or four 15-liter buckets of solution.
The design of the crane is a hodgepodge of what was at hand. Let's list the main details:
- swivel unit - truck hub;
Hubs from cars, trucks, and farm equipment are often used to make the swivel assembly in homemade cranes. The main thing is to calculate the loads acting on it and the fasteners.
- the boom is made of a pipe with a diameter of 75 mm;
- outriggers and base - a rectangular pipe with a section of 8x5 and 8.5x5.5 cm;
- the base of the tower is the “200th” channel;
- worm gearboxes for boom and cargo winches.
- three-phase electric motor with reverse, power 0.9 kW, converted to power from a 220 V network;
The crane turned out to be mobile, and by lowering the boom, it can be moved from place to place, rolling on wheels along compacted soil. Level adjustment is carried out using screw supports.
Metal, gearboxes and rollers were purchased at a recycled metal shop. Only the cable and bearings are new.
The weight of the crane without counterweight is about 250 kg. The cost of the structure, taking into account the purchase of consumables - cutting discs for angle grinders, electrodes for a welding inverter and paint, is 4 thousand rubles.
Peter 1
Crane, + time for turning, + selection of components and fitting of components, I completed it in 3 working days. In the future, after finishing the work, I will completely disassemble it.
Inexpensive mini lift
Practice shows that when building a private house, a real crane is not always needed. Often, a developer can get by with “little expense” and make a small lift based on an electrically driven hoist.
Gexx FORUMHOUSE Member
My design is simpler than the authors above, but it suits me quite well. I bought a hoist with a load capacity of 300 kg without a block and 600 kg with a block. Tests have shown that the device can lift a load weighing 250-270 kg, then the engine protection is triggered. During the construction season, I used it to lift about 40 pallets with building blocks, a 6-meter beam for the mauerlat, rafters, mortar for masonry and concrete for the reinforced belt.
The lift, again to save money, is made from used pipes, angles and channels.
Many people are interested in how to make a crane structure with their own hands. Such a device can help in building a house, utility rooms needed on the farm, a granary and a feed warehouse.
Drafting
To build a house you need a crane. Let's look at how to independently make a miniature crane design for lifting construction loads to a height. It is necessary to manufacture a mobile dismountable device.
First, a design for the manufacture of the apparatus is drawn up and calculated:
- The main part of the structure is the supporting frame. It is installed on wheels or permanently.
- The rotation unit of the unit is fixed to the running frame.
- The boom can be rotated thanks to the creation of electric or manual control.
- The unit can be disassembled into parts for ease of transportation.
- The crane will be stable thanks to the creation of a block of counterweights and steel cable stays.
- The load will be lifted using a block and a winch.
- You need to assemble a crane with your own hands.
Blueprints
To make a crane, first of all, draw up a project diagram and drawings of the main components. Consider the manufacture of a manually operated crane structure. It would be possible to make a device powered by electricity, making it possible to move a load using a device on a long cable, as happens in factory designs. But then the complexity of manufacturing units increases, this will entail an increase in the cost of the finished product and an increase in the time for its creation. Therefore, we will focus on making a manual model.
Welding
All connections of components and parts are made by welding. For this you need a welding machine. You can rent it while working on the crane or buy it at a specialized salon.
Assembly of the structure
Prepare:
- rope;
- washers;
- corners and channels;
- pipe;
- grinder;
- welding machine.
The frame should be made of steel angle 63x63x5 mm. A 5 m long boom is made from a pipe having a diameter of 55 mm. To strengthen the unit, use corners measuring 30x30x3 mm.
See » Technical characteristics of the KDE-163 railway crane and other modifications
The lifting capacity of such a homemade crane will be about 150 kg. If it is necessary to lift panels with a larger mass, then it is necessary to increase the multiplicity of pulleys, which are a device for lifting loads. The chain hoist is made from blocks, connected to each other with a cable. This cable should wrap the blocks in a circle. The pulley allows you to lift the panels using less force than the weight of the load.
The pulley system is 3-4 times stronger. In this case, friction losses are taken into account, which amount to 10%. The greater the gain in strength, the shorter the distance the tool can move the panels.
You can prepare and make all the details in 7-10 days.
Another 2 days are needed to assemble the mechanism. The lifting scheme is made in the form of a 2-fold pulley. The boom rotation unit is a 6-fold chain hoist. The turntable is made by attaching 2 washers. The axle replaces the 30mm bolt.
To reduce the size of the counterweights, the support legs are made 2 m long. With a turning radius of the washer of 200 mm and a distance of 2 m to the counterweight of 100 kg, a load of 1 ton will be applied to the bolt. This is taken into account when calculating the design of the tool. Perform stability calculations.
The structure is taken as a single system on one support. It is the smallest distance from the axis of rotation. The system is affected by: the weight of the load, the counterweight and the crane. The lifting drum is made from a pipe with a cross-section of 100 mm. It should not be installed close to blocks. It is fixed closer to the washers.
Blocks are made of 3 washers. They must be wrapped around the cord, the diameter of the blocks must be large so that the ropes do not fly out of the washers. The blocks are fixed without bearings.
You need a flexible cable with a cross section of 5 mm. Its working load is 150 kg, and its breaking load is 850 kg. The pulley operates on the principle of a lever. For a chain hoist, the main indicator is its multiplicity (the ratio of all cable branches to those extending from the drum).