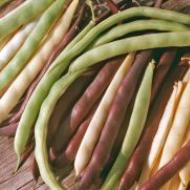
How wizards make metal spoons. How to make wooden spoons (37 photos)
The process of making a spoon is simple and unchanged for many centuries.
Information about lobster enough that in textbooks on thread that is on the Internet.
However, we cannot help but highlight how we make our spoons.
The description of this process will be a kind of "master class" for those who have never made a spoon himself, but want to try to learn it.
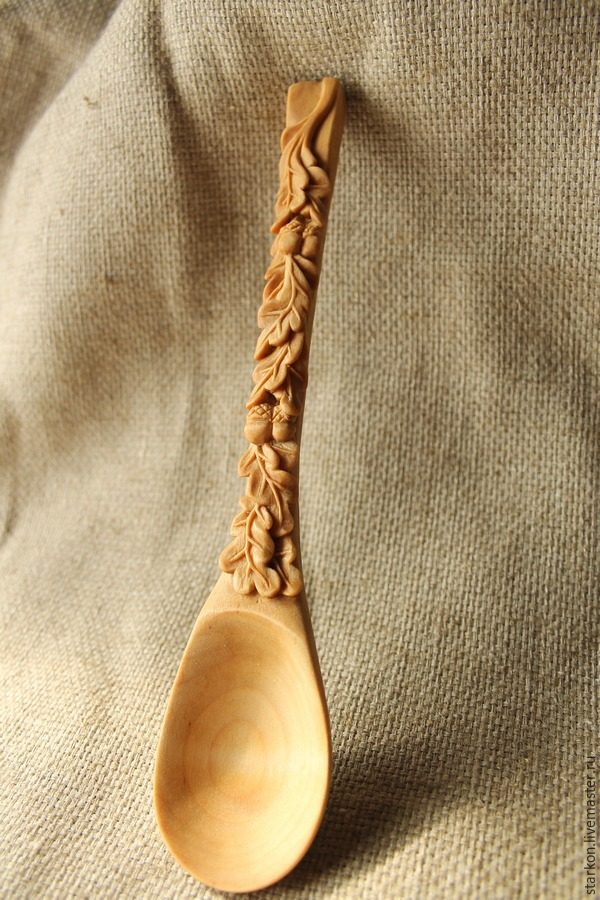
So, choose the material. In our choice of material for spoons, we stopped on linden (a very soft and pleasant wood for carving) and birch (harder, cut heavier, but very beautiful glossy cut and expressive texture). Spoons can be made from different wood species, be it oak, alder, cedar, beech, juniper, bird cherry, apple tree, etc. Each breed is good in its own way. Some spoons are very light, some stronger, some fragrant. The choice is yours.
Our blanks are dried lime or birch sticks 5 cm by 2.5 cm and 24 cm long (this is for a large spoon) and 17 cm (for a nursery). Apply a pencil-shape of the future spoon on them with a pencil.
After the ax we steal everything superfluous, first in one plane and then in another. Here is a nuance. You can do it immediately with a knife, but the process will be more time consuming physically. The ax is faster and more efficient. The more we handle with an ax, the less effort there is to work out with a knife.
Use a knife to bring the future spoon to a practically full-fledged look (the same rule - the better we bring the knife, the less it is to grind).
The next step is to choose "scoop". It is important not to overdo it. If you choose too deep (the error of beginners), then after sanding the wall “scooped” you will get too thin, and this will reduce the durability of the spoon.
Well, that turned out to be a spoon, just unpolished. If you wish, you can eat even this, but we go further. Grind in several stages. First, a large sandpaper, then medium, then small and at the end of super fine. The hardest thing is scooping, so the cleaner it is, the easier it is. Here it is, beautiful, quite ready-to-use, white little spoon. No wonder spoons in this stage are called "linen".
When we started cutting the spoons. we immediately planned for this work not to become routine, but to be as creative as possible, so we began to make our spoons like some kind of carved miniatures. To do this, a drawing is applied on the finished polished spoon (here the fantasy is limitless to the level of skill) and cut out. There is no sense in describing the threading process, as this is a separate topic.
Each spoon is its own style, its own image. And accordingly, various types of carving: relief, planar, from it geometric, ornaments, mini sculptures, etc. The type of thread, respectively, depends on the image of the spoon itself, whether to grind carved elements or not. Sometimes you need a gloss, and sometimes you want to see, on the thread, traces, as the master's knife wielded.
Well, now "Starodubovskaya spoon" is ready. Now she began her own, it was given to her, life. It remains to process the oil.
We take linseed oil, slightly heat it up and put a spoon in it. Shortly soaked, dried. Some villi on it are swelling up. All this grind. The last stage, in its effectiveness, is rather relative. Spoons that are not treated with oil serve just as reliably (if the material is dry), with the only difference being that at the first uses they are more rough, but this is eventually ground by the process of use. So if someone likes pure white spoons, he can safely use them (having previously ordered raw oil).
The process of making a spoon is simple and unchanged for many centuries. Information about lobster enough that in textbooks on carving that on the Internet.
However, we cannot help but highlight how we make our spoons. The description of this process will be a kind of "master class" for those who have never made a spoon himself, but want to try to learn it.
So, choose the material. In our choice of material for spoons, we stopped on linden (a very soft and pleasant wood for carving) and birch (harder, cut heavier, but very beautiful glossy cut and expressive texture). Spoons can be made from different wood species, be it oak, alder, cedar, beech, juniper, bird cherry, apple tree, etc. Each breed is good in its own way. Some spoons are very light, some stronger, some fragrant. The choice is yours.
Our blanks are dried lime or birch sticks 5 cm by 2.5 cm and 24 cm long (this is for a large spoon) and 17 cm (for a nursery). Apply a pencil-shape of the future spoon on them with a pencil.
After an ax we stew everything extra, first in one plane and then in another. Here is a nuance. You can do it immediately with a knife, but the process will be more time consuming physically. The ax is faster and more efficient. The more we handle with an ax, the less effort there is to work out with a knife.
Use a knife to bring the future spoon to a practically full-fledged look (the same rule - the better we bring the knife, the less it is to grind).
The next step is to choose "scoop". It is important not to overdo it. If you choose too deep (the error of beginners), then after sanding the wall “scooped” you will get too thin, and this will reduce the durability of the spoon.
Well, that turned out to be a spoon, but not polished. If you wish, you can eat even this, but we go further. Grind in several stages. First, a large sandpaper, then medium, then small and at the end of super fine. The hardest thing is scooping, so the cleaner it is, the easier it is. Here it is, beautiful, quite ready-to-use, white little spoon. No wonder spoons in this stage are called "linen".
When we started cutting the spoons. we immediately planned for this work not to become routine, but to be as creative as possible, so we began to make our spoons like some kind of carved miniatures. To do this, a drawing is applied on the finished polished spoon (here the fantasy is limitless to the level of skill) and cut out. There is no sense in describing the threading process, as this is a separate topic.
Each spoon is its own style, its own image. And accordingly, various types of carving: relief, planar, from it geometric, ornaments, mini sculptures, etc. The type of thread, respectively, depends on the image of the spoon itself, whether to grind carved elements or not. Sometimes you need a gloss, and sometimes you want to see, on the thread, traces, as the master's knife wielded.
Well, now "Starodubovskaya spoon" is ready. Now she began her own, it was given to her, life. It remains to process the oil.
We take linseed oil, slightly heat it up and put a spoon in it. Shortly soaked, dried. Some villi on it are swelling up. All this grind. The last stage, in its effectiveness, is rather relative. Spoons that are not treated with oil serve just as reliably (if the material is dry), with the only difference being that at the first uses they are more rough, but this is eventually ground by the process of use. So if someone likes pure white spoons, he can safely use them (having previously ordered raw oil).
Painting wooden spoons for children 5-7 years on the topic: Khokhloma
Khokhloma painting of wooden spoons and scoops of gouache, using cotton buds.
Polukarova Svetlana Sergeevna, MKDOU Anninsky d / s ODS "Rostok", Voronezh region, p. Anna.
Purpose: Masster - class is designed for children 6-7 years. Painting on wood gives you an opportunity to get acquainted with the secrets of artistic crafts and develop fine motor skills of hands, their sensitivity. This item can be used as an interior decoration, as a gift for March 8, as well as for the exhibition.
Purpose: expand the idea of the types of decorative arts and crafts, continue to acquaint children with Khokhloma painting on various items of dishes.
Tasks:
See the peculiarities of the Khokhloma painting, get acquainted with the new composition of the pattern: depicting a rounded branch with berries; draw pattern on yellow background.
Exercise in the corners of the hand when drawing curls in different directions, to consolidate the ability to use cotton buds to draw small circles.
Learn to draw neatly, beautifully placing the drawing on a wooden form.
Develop creativity and imagination in the manufacture of decorative spoons
To foster respect and respect for the products of people.
Materials and tools: wooden blanks - spoon and spatula; an album, a simple pencil, an eraser, gouache paints (red, yellow, green, black, white), a jar of water; brush protein number 2, 4, 6; cotton buds.
Wooden spoons - This is a reflection of the identity of our Russian culture and its cultural traditions. Wooden spoons came to us from time immemorial, enchanting everyone with its originality and color. What a wonderful souvenir gift to your friends and relatives!
Wooden crafts Not only beautiful - it is an environmentally friendly material. Using wood products is not only safe, but also healthy. No wonder in Russia from time immemorial, they ate wooden dishes with wooden cutlery and were healthy until old age.
1. Draw on paper a sketch of a spoon and spatula.
2. According to the drawn sketch we cut out objects from a tree.
3. Further we continue to work with paper sketches. We will paint the painted products with yellow gouache.
4. We think in advance of drawing paintings on paper. Draw a simple pencil, then decorate with gouache.
5. Next when the sketch is ready we do the same work with wooden products. Cover with yellow on both sides.
6.Tortsy paint with red gouache.
7. We put an ornament - berries, red gouache. On the spatula, draw 3 circles with the brush number 2. On the spoon - cotton buds of the currant cluster, using the spear method.
8. On a spoon with cotton buds do flowers in blue
9 . On the shoulder blade, the leaves are the grip of the brush №6. On a spoon, paint with brush number 2 currant leaves.
10. We draw curls with black paint, brush number 2.
11. Make out the antennae on the shoulder. Put a cotton swab in black paint.
12. Decorate with white paint leaves and currants on a spoon.
13. We draw on pens a red border.
14. The product is ready. At will it is possible to varnish.
15. Useful tips:
- dry the spoon after painting for at least eight hours.
- if you plan to varnish a product, dry it at room temperature in that place of the room where there are no drafts and dust, the usual first varnishing time is 15-16 hours, the second 24-25 hours.
It is difficult to find a more indispensable cutlery than a spoon. She can eat, cut, use as a measuring dish and for educational purposes, it can be cooked and simply put up as an ornament. And yet this is a musical instrument!
In Russia and in the Scandinavian countries, historically spoons were made of wood. In our country, the capital of the spoon craft became the town of Semenov, Nizhny Novgorod region. At the end of the century before last in the Semenovskiy district, about 7 thousand people worked on the manufacture of spoons and they produced more than three million spoons a year. In fact, it is only at first glance huge numbers. Simple math shows that productivity is one spoon per person per day.
The population of the Russian Empire at that time was 129 million people. Thus, it would have taken 43 years for the Semenov artisans to cover consumer demand. Therefore, in every village in almost every house, during long winter evenings, men not only prepared carts and rakes for the summer, but also cut spoons for family needs.
I had a choice: go to Semenov and stop producing souvenir Khokhloma spoons, or find a craftsman and look at modern spoons for everyday use. The craftsman, of course, was found, all in the same Nizhny Novgorod region.
SPOON - OK. instrument for baking, for eating liquids; bread, chevyrka, edalka. pouring spoon, ladle. the wooden spoon (the main line of the lower lips of the family of the county) is cut off from baklusha with a hatchet; spoon happens: mezheumok, simple Russian, wide; Butyrka, burlatskaya, the same, but thicker and rougher; barefoot, long, stupid; semi-bare, more roundly than that; nosed, sharp-nosed; fine, generally fine, clean finish. white ie, unpainted, first comes 9-18 rubles. assignation thousand, aspen and birch; maple colored up to 75 rubles. thousand assignments.
This is a small excerpt from the article about the spoon in the Dal dictionary. The article is so self-sufficient that if I bring it in full, then there will be nothing more to tell. So let's watch the pictures and listen to our narrator today.
Here he is - having mastered many professions, but Leonid Khazov, who has settled on the spoon craft. He really earns his living by making spoons and wooden utensils, so making the material about him was doubly informative. And in between times, I learned a lot of new and interesting things about this old craft.
It all starts prosaically. Leonid takes a deck of logs and chips it in half, and then for a few more poles. The amount depends on the diameter of the deck and the estimated number of spoons. One pole - one spoon.
As the master says, anyone can make a spoon with a knife and desire. Yes, the first spoon can be ugly and look more like a curved spatula, but it will be able to perform its functions. Even when making handicraft spoons for sale, a rather simple set of tools is used, which can be found in any house, probably.
I am distracted by the story, and in the picture with an ax, the descent to the future scoop is selected. Everyone knows the structure of the spoon? Scooped, held and jumper.
Practically any deciduous tree will be suitable as a raw material. Most often, the dishes are made from birch, aspen, maple or fruit trees. Conifers are not suitable because of their resinous and characteristic odor. In Russia, they made spoons even from imported palm trees and they cost ten times more than usual.
Now the photo shows a spoon in the stage called “baclusha”. This work was done by apprentices, and the masters brought these blanks to the mind.
With the help of a pattern, the contour of the future spoon is applied to the buckle. Depending on the destination, they are round, oval, flat, voluminous. And decorative spoons form is limited only by the imagination of the master.
Each master has his own well-known brand product, which he does en masse on stream. Nozhevikov have certain types of knives, blacksmiths souvenir flowers and horseshoes, no exception, and spoons. Twenty years ago, Leonid copied a Soviet tablespoon, and with minor changes and improvements this form remained the main one.
Clutching the workpiece in a vice, Leonid chooses wood from a future spoon. By the way, unlike other types of woodcarving, spoons are cut from raw wood and dried already in finished form. Some craftsmen specially store the ridges in the tall grass, so the tree does not dry out.
The ax is shaped like the back of a spoon.
You can continue to work with a hatchet and scrape the baclum on the sides until the shape is conceived, you can take a hacksaw, and you can take an electric jigsaw, which is fastest. This stage can also be done with a knife or chisel, the only question is the amount of time spent.
Birch is practically not inferior in strength to oak, and lives as a spoon for much longer - oak cracks. As you can see, even with such a rather delicate operation, the master is not in a hurry to take up the knife, but is wielding an ax.
Last waving an ax. Traditional Russian souvenir spoon is more like a hemisphere: deep, voluminous and not very comfortable to use, like a ladle or ladle. Here the forms are more close to the modern classic oval spoons.
Up to this stage, a not very well-trained apprentice could have done all the work. In principle, another ten minutes of work with a knife and in your hand will be quite a usable spoon. This is where the work of the master begins. The spoon should be not only functional, but also beautiful.
At the beginning of the post I mentioned the performance of the Semenov masters. In fact, there was confusion somewhere in the figures, either people worked less or they cut not only spoons. According to the data for 1905 in the Balakhna district of the Nizhny Novgorod district there were about 1,400 spoons and they produced 13 million spoons, i.e. 25 spoons per person per day. These numbers are already similar to the truth.
Leonid says that one can make fifty spoons in two or three days, and in the artels the whole process was divided into stages and divided among the workers, which reduced the time for production.
However, Leonid prefers to do the party in stages: first he grunts baklushi, then cuts off all the excess on them, and then he takes up the knife and sandpaper. It is believed that from the state of the log to the finished spoon, it should be in the hands of the master at least 13 times. Not tested, you can find yourself.
The handle is ready, it remains to scrape the scoop. The thickness of the walls of 3-4 millimeters, if done thinner, the spoon will be lighter and may be prettier, but will last less. The more accurate the excess is removed, the easier it will be to polish later.
As in any craft, there is little time left for creativity. If business feeds you, then it is necessary to make sample products, with the realization of which there will definitely not be any problems. Leonid has a well-established sales, his products can be found in Moscow and some major Russian cities. But, of course, he wants to do something new, try some tricks, cut out something unusual. Sometimes lucky and such orders arrive, and sometimes you have to sell yourself.
This is how the next spoon was born.
In the old days with the sale was about the same situation. The last thing they did was get spoons, which were cut under the owner, then those who handed over spoons to merchants wholesale went, and those who sold their spoons themselves had the highest income.
Our spoons are drying. This is a couple of days on the air in the summer or on the stove in the winter. Just while the batch of spoons is being made, the previous one has time to dry.
We finish the historical excursion. Few people realize, but the demand for wooden spoons fell only after World War II. Then it was supplanted by tin and metal spoons, and instead of Lozhkosoyuz, the association “Khokhloma painting” was organized.
While the spoons dry, we look at the tools. It has long been noticed that the straighter a person's hands, the more inconspicuous the instrument. More precisely, no, not so. The straighter the arms, the less people chase after brands and appearance, and the more they value functionality.
And Leonid has some self-made tools. Knives are made of saw blade, the so-called quick-cutting steel. A lot of them, not because they break often, just Leonid is preparing to conduct workshops on carving and knives will be distributed to students.
But the cranberry from the bearing race. Steel there is also well suited for such a tool, so it remains only to find a bearing with a suitable diameter, cut it and weld the shank. Well, do not forget to sharpen of course.
At my request, Leonid showed the sharpening process using the example of a semicircular chisel. First, the angle is displayed and the notches on a large stone are hewn. Here the main trick is not to overheat the metal, hardening can be released and the tool will be damaged.
Next, a chisel or knife sharpened on a small stone with a constant flow of water. The edge is sharpened until a uniform burr appears on the opposite side. This is if the chisel, with a knife a little smarter, you need to sharpen it from both sides. And then it is all polished on a leather circle with GOI paste. Before removing this very burr.
The working tool rarely requires the first two procedures, usually there are enough straightening on the skin.
The burr on the inside gets better with fine sandpaper wound on a piece of wood of a suitable diameter. If necessary, again polished on the skin. In general, the same as when sharpening ordinary knives.
Let's go back to our spoons. It used to be that spoons had three varieties of treatment: facial, very good and good. We will make a facial spoon, we're not some hacks!
It is possible to sand a sandpaper manually, it is possible to use the machine. I do not know what our ancestors polished with, but in the Scandinavian countries for this purpose they used a special variety of horsetail.
Very quickly, the spoon takes on a well-groomed appearance and downright asks for it to be finished and placed next to the plate.
But do not hurry. Besides the fact that the spoon is sanded in several stages, reducing the grit of the sandpaper, there is one more nuance.
When using the spoon to its intended purpose, it begins to be poured from water. This is not critical in the hands, but very unpleasant in the mouth. Therefore, after grinding it is wetted and dried, and then polished again. And so several times.
Now the spoon is almost ready. Her pen can be decorated with carvings, and you can some kind of inscription. For example, a name or a saying.
Here, too, there is a little trick: in order for the inscription to turn out to be even, it is necessary to write backwards from the last letter to the first.
And the final touch - a spoon is soaked in ordinary linseed oil. More massive products are immersed in oil and are in it for some time, but the spoons just enough to anoint with a brush, they are so thin that they are soaked through.
About a day the spoons dry and absorb the oil, then they are wiped with a napkin and that's it, they are ready to please their new owner.
From wooden utensils, as well as from all wooden things made by hands, some kind of heat comes out. Now I have two spoons, I think to make a bowl or a plate, or even a whole set
It is difficult to find a more indispensable cutlery than a spoon. She can eat, cut, use as a measuring dish and for educational purposes, it can be cooked and simply put up as an ornament. And yet this is a musical instrument!
In Russia and in the Scandinavian countries, historically spoons were made of wood. In our country, the capital of the spoon craft became the town of Semenov, Nizhny Novgorod region. At the end of the century before last in the Semenovskiy district, about 7 thousand people worked on the manufacture of spoons and they produced more than three million spoons a year. In fact, it is only at first glance huge numbers. Simple math shows that productivity is one spoon per person per day.
The population of the Russian Empire at that time was 129 million people. Thus, it would have taken 43 years for the Semenov artisans to cover consumer demand. Therefore, in every village in almost every house, during long winter evenings, men not only prepared carts and rakes for the summer, but also cut spoons for family needs.
I had a choice: go to Semenov and stop producing souvenir Khokhloma spoons, or find a craftsman and look at modern spoons for everyday use. The craftsman, of course, was found, all in the same Nizhny Novgorod region.
SPOON - OK. instrument for baking, for eating liquids; bread, chevyrka, edalka. pouring spoon, ladle. the wooden spoon (the main line of the lower lips of the family of the county) is cut off from baklusha with a hatchet; spoon happens: mezheumok, simple Russian, wide; Butyrka, burlatskaya, the same, but thicker and rougher; barefoot, long, stupid; semi-bare, more roundly than that; nosed, sharp-nosed; fine, generally fine, clean finish. white ie, unpainted, first comes 9-18 rubles. assignation thousand, aspen and birch; maple colored up to 75 rubles. thousand assignments.
This is a small excerpt from the article about the spoon in the Dal dictionary. The article is so self-sufficient that if I bring it in full, then there will be nothing more to tell. So let's watch the pictures and listen to our narrator today.
Here he is - having mastered many professions, but Leonid Khazov, who has settled on the spoon craft. He really earns his living by making spoons and wooden utensils, so making the material about him was doubly informative. And in between times, I learned a lot of new and interesting things about this old craft.
It all starts prosaically. Leonid takes a deck of logs and chips it in half, and then for a few more poles. The amount depends on the diameter of the deck and the estimated number of spoons. One pole - one spoon.
As the master says, anyone can make a spoon with a knife and desire. Yes, the first spoon can be ugly and look more like a curved spatula, but it will be able to perform its functions. Even when making handicraft spoons for sale, a rather simple set of tools is used, which can be found in any house, probably.
I am distracted by the story, and in the picture with an ax, the descent to the future scoop is selected. Everyone knows the structure of the spoon? Scooped, held and jumper.
Practically any deciduous tree will be suitable as a raw material. Most often, the dishes are made from birch, aspen, maple or fruit trees. Conifers are not suitable because of their resinous and characteristic odor. In Russia, they made spoons even from imported palm trees and they cost ten times more than usual.
Now the photo shows a spoon in the stage called “baclusha”. This work was done by apprentices, and the masters brought these blanks to the mind.
With the help of a pattern, the contour of the future spoon is applied to the buckle. Depending on the destination, they are round, oval, flat, voluminous. And decorative spoons form is limited only by the imagination of the master.
Each master has his own well-known brand product, which he does en masse on stream. Nozhevikov have certain types of knives, blacksmiths souvenir flowers and horseshoes, no exception, and spoons. Twenty years ago, Leonid copied a Soviet tablespoon, and with minor changes and improvements this form remained the main one.
Clutching the workpiece in a vice, Leonid chooses wood from a future spoon. By the way, unlike other types of woodcarving, spoons are cut from raw wood and dried already in finished form. Some craftsmen specially store the ridges in the tall grass, so the tree does not dry out.
The ax is shaped like the back of a spoon.
You can continue to work with a hatchet and scrape the baclum on the sides until the shape is conceived, you can take a hacksaw, and you can take an electric jigsaw, which is fastest. This stage can also be done with a knife or chisel, the only question is the amount of time spent.
Birch is practically not inferior in strength to oak, and lives as a spoon for much longer - oak cracks. As you can see, even with such a rather delicate operation, the master is not in a hurry to take up the knife, but is wielding an ax.
Last waving an ax. Traditional Russian souvenir spoon is more like a hemisphere: deep, voluminous and not very comfortable to use, like a ladle or ladle. Here the forms are more close to the modern classic oval spoons.
Up to this stage, a not very well-trained apprentice could have done all the work. In principle, another ten minutes of work with a knife and in your hand will be quite a usable spoon. This is where the work of the master begins. The spoon should be not only functional, but also beautiful.
At the beginning of the post I mentioned the performance of the Semenov masters. In fact, there was confusion somewhere in the figures, either people worked less or they cut not only spoons. According to the data for 1905 in the Balakhna district of the Nizhny Novgorod district there were about 1,400 spoons and they produced 13 million spoons, i.e. 25 spoons per person per day. These numbers are already similar to the truth.
Leonid says that one can make fifty spoons in two or three days, and in the artels the whole process was divided into stages and divided among the workers, which reduced the time for production.
However, Leonid prefers to do the party in stages: first he grunts baklushi, then cuts off all the excess on them, and then he takes up the knife and sandpaper. It is believed that from the state of the log to the finished spoon, it should be in the hands of the master at least 13 times. Not tested, you can find yourself.
The handle is ready, it remains to scrape the scoop. The thickness of the walls of 3-4 millimeters, if done thinner, the spoon will be lighter and may be prettier, but will last less. The more accurate the excess is removed, the easier it will be to polish later.
As in any craft, there is little time left for creativity. If business feeds you, then it is necessary to make sample products, with the realization of which there will definitely not be any problems. Leonid has a well-established sales, his products can be found in Moscow and some major Russian cities. But, of course, he wants to do something new, try some tricks, cut out something unusual. Sometimes lucky and such orders arrive, and sometimes you have to sell yourself.
This is how the next spoon was born.
In the old days with the sale was about the same situation. The last thing they did was get spoons, which were cut under the owner, then those who handed over spoons to merchants wholesale went, and those who sold their spoons themselves had the highest income.
Our spoons are drying. This is a couple of days on the air in the summer or on the stove in the winter. Just while the batch of spoons is being made, the previous one has time to dry.
We finish the historical excursion. Few people realize, but the demand for wooden spoons fell only after World War II. Then it was supplanted by tin and metal spoons, and instead of Lozhkosoyuz, the association “Khokhloma painting” was organized.
While the spoons dry, we look at the tools. It has long been noticed that the straighter a person's hands, the more inconspicuous the instrument. More precisely, no, not so. The straighter the arms, the less people chase after brands and appearance, and the more they value functionality.
And Leonid has some self-made tools. Knives are made of saw blade, the so-called quick-cutting steel. A lot of them, not because they break often, just Leonid is preparing to conduct workshops on carving and knives will be distributed to students.
But the cranberry from the bearing race. Steel there is also well suited for such a tool, so it remains only to find a bearing with a suitable diameter, cut it and weld the shank. Well, do not forget to sharpen of course.
At my request, Leonid showed the sharpening process using the example of a semicircular chisel. First, the angle is displayed and the notches on a large stone are hewn. Here the main trick is not to overheat the metal, hardening can be released and the tool will be damaged.
Next, a chisel or knife sharpened on a small stone with a constant flow of water. The edge is sharpened until a uniform burr appears on the opposite side. This is if the chisel, with a knife a little smarter, you need to sharpen it from both sides. And then it is all polished on a leather circle with GOI paste. Before removing this very burr.
The working tool rarely requires the first two procedures, usually there are enough straightening on the skin.
The burr on the inside gets better with fine sandpaper wound on a piece of wood of a suitable diameter. If necessary, again polished on the skin. In general, the same as when sharpening ordinary knives.
Let's go back to our spoons. It used to be that spoons had three varieties of treatment: facial, very good and good. We will make a facial spoon, we're not some hacks!
It is possible to sand a sandpaper manually, it is possible to use the machine. I do not know what our ancestors polished with, but in the Scandinavian countries for this purpose they used a special variety of horsetail.
Very quickly, the spoon takes on a well-groomed appearance and downright asks for it to be finished and placed next to the plate.
But do not hurry. Besides the fact that the spoon is sanded in several stages, reducing the grit of the sandpaper, there is one more nuance.
When using the spoon to its intended purpose, it begins to be poured from water. This is not critical in the hands, but very unpleasant in the mouth. Therefore, after grinding it is wetted and dried, and then polished again. And so several times.
Now the spoon is almost ready. Her pen can be decorated with carvings, and you can some kind of inscription. For example, a name or a saying.
Here, too, there is a little trick: in order for the inscription to turn out to be even, it is necessary to write backwards from the last letter to the first.
And the final touch - a spoon is soaked in ordinary linseed oil. More massive products are immersed in oil and are in it for some time, but the spoons just enough to anoint with a brush, they are so thin that they are soaked through.
About a day the spoons dry and absorb the oil, then they are wiped with a napkin and that's it, they are ready to please their new owner.
From wooden utensils, as well as from all wooden things made by hands, some kind of heat comes out. Now I have two spoons, I think to make a bowl or a plate, or even a whole set