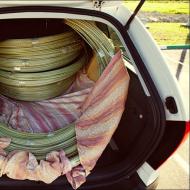
Is it possible to use fiberglass reinforcement for the foundation? Use of composite fiberglass reinforcement for the foundation Reinforcement of strip foundations with composite reinforcement
The construction market does not stand still, which leads to the emergence of new materials that have improved characteristics compared to analogues of the previous generation. Relatively recently, fiberglass reinforcement has appeared in the construction field, which has become a serious competitor to metal rods.
Until recently, steel reinforcement was the only material that was used in the production of reinforced concrete products to increase the strength of foundations and other elements of building structures. However, the new material is characterized by more advanced properties, which attracts the attention of the consumer.
Description of the material and its types
Fiberglass reinforcement is a non-metallic rod wound with fibers of a composite material or sprayed with fine abrasive powder. The diameter of reinforced rods can range from 4 to 18 mm.
Depending on the material used as the basis for the manufacture of the rod, there are several types of composite reinforcement:
- Basalt products (denoted by the letters ABP) are produced on the basis of basalt fibers, bound with resin of organic origin. Such fittings are characterized by high resistance to aggressive environments, including gases, alkalis and salts.
- Fiberglass reinforcement (abbreviation ASP) is made from fiberglass fibers connected using thermosetting resins. The advantage of such rods is their low weight and high strength characteristics.
- Carbon fiber reinforcement (designation AUP) is produced on the basis of hydrocarbons. The material is characterized by increased strength, but has a very high cost, which significantly reduces its popularity.
- The combined products (abbreviation ACC) are based on basalt and fiberglass. This material is wear-resistant and has a wide range of applications.
Among the listed types of composite reinforcement, fiberglass products are the most popular, so you should study this material in more detail.
Advantages and scope of use of fiberglass reinforcement
Unlike steel rods, fiberglass reinforcement has a number of significant advantages:
- Light weight, making it more convenient to transport the material and perform various actions with it.
- High resistance to aggressive environments, including gases, alkalis and salts.
- Resistance to the formation of foci of corrosion.
- High tensile strength.
All of the listed characteristics significantly expand the scope of use of composite fiberglass reinforcement:
- With its help, walls and partitions made of bricks and various blocks are strengthened.
- Using fiberglass reinforcement, load-bearing walls are connected to facing partitions. By the way, we have an interesting article on the topic "".
- Fiberglass reinforcement is excellent for strengthening and, the sole of which lies significantly below the freezing level of the soil. In addition, it is recommended to use composite reinforcement to strengthen foundations operating in aggressive environments.
Fiberglass composite reinforcement can be used to strengthen any type of foundation for low-rise buildings. However, in the case of strip and column foundations for buildings of no more than three floors, composite rods have received many positive recommendations. In other words, fiberglass reinforcement can be used to strengthen a monolithic concrete strip for a private house or cottage with one or two floors, a bathhouse, a garage or outbuildings. Our website has information about that, and, and much more. You can use the site search to find the information you are interested in.
It is worth recalling that fiberglass reinforcement is a new material, the properties of which have not been fully studied. Therefore, it is better to use the material for structural reinforcement, avoiding moments where increased bending and torsional strength is required.
Calculation of fiberglass reinforcement
Building a foundation with your own hands requires calculating the amount of building materials, including composite reinforcement.
Taking into account various factors, materials should be calculated using the following algorithm:
- Determination of the total length of the foundation, taking into account the length of the internal load-bearing partition.
- Calculation of the length of the reinforcement bars, taking into account that the reinforcement will be laid in two tiers (4 bars).
- Determining the number of connections. It should be taken into account that the connection of fiberglass reinforcement bars is carried out not by welding, but by overlap. Therefore, you need to add 1 meter to each corner.
- Perform cross connection calculations.
For a complete understanding, you can take an example of calculations of reinforcement for the foundation of a house measuring 6 * 8 meters, the internal load-bearing wall of which is 6 meters.
The total length of the foundation is determined as follows:
(6+8)*2+6=34 meters.
The total length of the rods, taking into account that the two-level structure consists of 4 parallel rods, is:
34*4=136 meters.
The number of connections and, accordingly, the length of the reinforcement for this purpose is determined as follows: the number of main walls is multiplied by 1 meter of overlap and by the number of rods. It turns out the following:
(4+1)*1*4=20 meters.
Therefore, for a foundation of the specified dimensions, taking into account additional material for joining, the following number of longitudinal rods will be required:
136+20=156 meters.
The number of transverse ring joints should also be calculated. According to the technology for laying the reinforcing frame, the connecting rings should be located at a distance of 50 cm from each other. To determine the number of transverse connecting rings, it is necessary to divide the total length of the reinforcement by 0.5 meters. It turns out the following:
To calculate the length of reinforcement required for this number of cross members, the dimensions of the frame are taken into account. For example, if the frame lattice has a size of 60*30 cm, then the length of the rod for one ring will be equal to the following:
(0.6 + 0.3) * 2 * 68 \u003d 122.4 meters.
In addition, it is imperative to add a certain amount of material for reserve. That is, you should take not 122, but 130 meters of reinforcement.
Summarizing the results of calculations of the longitudinal and transverse elements of the frame, we obtain the result:
When choosing a material for foundation reinforcement, all significant factors should be taken into account. Despite the large number of positive characteristics, fiberglass reinforcement is a new material, and metal rods are time-tested.
Thanks to the use of the latest technologies, a composite polymer material has appeared on the construction market, successfully replacing traditional metal analogues. So, when creating a frame base for the foundation, instead of steel analogues, fiberglass reinforcement is used. The material has gained popularity due to its many advantages. But reinforcing the foundation with fiberglass reinforcement requires strict adherence to technology and the correct choice of rod diameter.
Fiberglass reinforcement is non-metallic rods of round cross-section, which can be smooth or corrugated with transverse protrusions. The diameter varies from 4 to 20 mm, the length of the rods is 12 m, in coils - from 100 to 150 m. Fiberglass reinforcement is mainly used for strip-type foundations, as well as when laying road surfaces and creating various concrete structures.
Peculiarities
The production of fiberglass reinforcement is carried out in accordance with GOST 31938. For the manufacture of rods, glass, basalt, aramid or carbon (graphite) fibers are used, which create an elastic core. The threads are impregnated with a special polymer binder of thermosetting or thermoplastic action (epoxy resins) and hardening compounds, resulting in high-strength reinforcement.
Composite material, depending on the composition of the fibers, is divided into:
- Fiberglass reinforcement - ASP (ASK);
- Basalt composite - ABK;
- Carbon composite - AUK;
- Aramidocomposite - AAK;
- Combined with composite components - ACC.
To increase the adhesive properties, the surface of the fiberglass reinforcement is covered with sand, resulting in good adhesion to the concrete surface. The projections also improve the connection to the concrete.
Advantages and disadvantages
Fiberglass reinforcement has many positive properties, of which we can highlight:
- High specific strength.
- Light weight (a 100 meter bay weighs about 10 kg). But at the same time, the reduction in the weight of the concrete structure itself is not so significant that this indicator can be taken into account during the construction of both small and large objects, because the bulk of the weight is concrete.
- Low thermal conductivity, due to which there are no cold bridges.
- Longer length (sold in coils/skeins). When creating a frame, you have to use less material, due to the fact that the areas where the rods overlap are reduced.
- Compactness. The reinforcement is easy to transport and there is no need to use a special vehicle to deliver it to the site, since the material rolled into a coil fits freely into the trunk of a car. In addition, one worker can move several bays at once.
- Dielectric impenetrability and radio transparency - no current is carried out, there is no radio interference inside the building or structure.
- Resistance to aggressive environments and chemical influences.
- Non-corrosive. The rods are used in humid environments, and even with prolonged contact with water, destructive rust does not appear.
- High tensile strength.
- Good resistance to temperature changes.
- No cracks, due to the fact that the thermal expansion indicators of the polymer composition and concrete are as close as possible.
- Significant savings on quantity and transportation.
- Durability.
Despite the large list of positive factors, fiberglass reinforcement has disadvantages:
- High price. But this negative point is compensated by the possibility of using a composite of a smaller diameter, which costs less.
- Low heat resistance.
- Poor flexibility. The rod can only be bent 90° in a factory setting.
- Low elasticity to fracture.
- The frame made of composite rods does not have high rigidity, as a result of which it does not have good resistance to vibrations and loads that are created during pouring concrete using a mixer.
Knowing all the positive and negative aspects, you can choose the right fiberglass reinforcement and use it only in those concrete structures and structures where it is practical and financially justifiable.
Properties and characteristics
The main properties of composite reinforcement, which are taken into account when reinforcing strip foundations and other structures, are:
- Tensile strength - from 800 MPa (fiberglass) and from 1400 MPa (carbon composite).
- The maximum temperature during operation is from 60°.
- Elasticity when stretched. This indicator in AUC is 2.5 times higher than in TSA.
- Maximum compressive strength is over 300 MPa.
- Strength during cross-section - in ASP - no less than 150 MPa, in AUK - no less than 350 MPa.
- The relative elongation of ASP and AUK is 2.2%, in metal analogs - 0.195%.
GOST 31938-2012 regulates the technical conditions that apply to periodic profile reinforcement. GOSTs 32486-2013, 32487-2013 and 32492-2013 establish the procedure for determining and testing the structural and thermomechanical characteristics of a composite according to the following indicators:
- Thermal expansion.
- Coefficient of linear thermal expansion, including differential and average.
- Glass transition.
- Glass transition temperatures.
- Longitudinal capillary porosity.
- Resistance to aggressive environments;
- Strength limits in several parameters.
The regulatory documents indicate the general test provisions and the recommended nominal diameter of fiberglass reinforcement, which, in accordance with SNiP 52-01-2003, can be used in the design of concrete structures. Taking into account the technical conditions stipulated by state standards, the cross-section of the rods can be of other sizes. The composite with a diameter of 4 to 8 mm is supplied in coils of standard or stated meter, as well as in sections from 50 to 1200 cm. Manufacturers are guided by their own and industry specifications with test reports. In addition, certificates are provided for manufactured products.
Calculation for different foundations
Before starting to build a strip foundation with a frame base made of composite material, the footage of rods required for reinforcement is calculated. When making calculations, technical documentation with standards and technical conditions is used. According to the recommendations of SNiP, the minimum permissible amount of fiberglass reinforcement in concrete structures should be at least 0.1% of the total cross-sectional area of the foundation or structure under construction. The actual dimensions of the base relative to the total cross-section of the rods are taken into account. Calculations are carried out individually for each object.
Scope of application
Composite reinforcement has received a wide range of applications - these are:
- Industrial, civil, commercial and residential buildings.
- Road construction sector - reinforcement of road surfaces.
- Strengthening slopes on highways.
- Bridges and coastal fortifications.
- Strip and other types of foundations.
- Concrete structures and structures.
- Masonry made of bricks and foam blocks, where flexible connections are provided.
The use of composite polymer reinforcement is very popular in cottage construction. The new material is actively used in the field of capital construction.
Comparison of fiberglass reinforcement with steel
By comparing composite reinforcement with metal analogues, you can understand how profitable it is to use it in construction:
- The specific gravity is 8-10 times less (indicators vary depending on the diameter of the rods).
- The tensile strength is 2-3 times greater (for steel analogues it is 400 MPa).
- The length is much longer - up to 150 m.
- Thanks to the dielectric, no current is passed through and radio interference is not created.
- There are no cold bridges.
- Low thermal conductivity.
Interchangeability in diameter with metal analogues:
How to reinforce a foundation with composite reinforcement
In the construction of cottages, new technologies have increasingly begun to be used, which involve the use of modern materials, so it is necessary to know the technology. Reinforcing the foundation with fiberglass reinforcement involves creating a frame base. Using non-metallic rods, welding work is completely eliminated, so it is very important to perform the wire binding correctly.
The assembly of a small frame should be done on a level area, after which the finished product should be installed in a trench or other desired location. Reinforcement with fiberglass reinforcement involves the creation of two belts - upper and lower. The connecting elements are transverse, longitudinal and vertical rods, which are attached at intervals of 20-23 cm (made of metal - 10-20 cm). The diameter of the reinforcement is provided at least 12 mm, but for foundations that do not bear large loads, 6-8 mm will be sufficient.
If the structure for reinforcing the foundation has large parameters, then the work is performed directly at the installation site and in the following sequence:
- the calculated number of transverse rods are laid in the trench;
- the main longitudinal reinforcement is placed on top;
- a bunch is performed, as a result of which cells of a certain size are formed (the greater the distance between the rods, the larger the cells are obtained);
- when the lower elements are connected to each other, vertical rods are installed to which the upper load-bearing sheathing is attached.
Ribbed reinforcement, whose characteristics meet the requirements of GOST and SNiP, is better suited for reinforcement. Laying of fiberglass reinforcement is carried out in compliance with the same technologies as for metal analogues. The lower belt should be slightly raised above the ground. To do this, the rods of the lower row are fastened on a vertical riser or stones of the same size serve as support. The thickness of the protective layer of concrete to the upper belt should be at least 2.5 cm. When making bends at the edges and corners, uniformity is maintained - the length of the bent rod should not be less than 25-30 cm.
The use of fiberglass reinforcement for foundation reinforcement is a new technology that has not yet been tested by time. Therefore, it is necessary to make preliminary calculations and strictly follow the rules for assembling and laying fiberglass rods. During pouring, it is necessary to ensure that the geometry of the frame base remains unchanged.
Competent builders understand how important it is to introduce new technologies and materials into their practice. The world has known about composite reinforcement for a long time, but its mass production and use began only a few years ago. We will talk about the features of working with fiberglass reinforcement using the example of a foundation.
Strengths and weaknesses of composite reinforcement
You should not expect that any building material will be a unique and unified proposal. However, proper application in accordance with operating conditions allows you to achieve truly outstanding results. It’s the same with composite reinforcement: using its positive qualities and leveling out the negative ones, you can ensure long-term operation at lower material costs.
The main advantage of glass-polymer reinforcement is its inherent high limit of destructive impact - almost 2.5 times higher than that of steel. Composite reinforcement is much better at compensating for tensile forces in a concrete mass than steel. Especially when you consider that during production, plastic rods can be provided with a surface texture that promotes maximum effective adhesion to the concrete mass.
Another obvious advantage is the extremely high resistance to aggressive environments. Concrete structures that are permanently exposed to high humidity or exposed to saline solutions have a much longer service life when reinforced with composite materials. We must not forget about the manifestations of electrolysis: the dielectric properties of plastic can be both a plus and a minus.
There is also a fly in the ointment: fiberglass reinforcement irreversibly loses its properties when heated. This forces us to reconsider the feasibility of its use from a fire safety point of view. When heated to 150-200 °C, the reinforcement loses its strength properties, but if thermosetting polymers were used as a binder, the reinforcement loses its strength irreversibly.
Another disadvantage of composite reinforcement is its low modulus of elasticity, that is, low bending resistance. Because of this, in structures with concentrated impacts, the laying of fiberglass reinforcement is required in quantities up to 4 times higher than the content norm for the cross section in comparison with steel reinforcement.
Benefits in the context of the foundation
The flexibility of polymer reinforcement allows it to be transported in reels, so the length of a single element is practically unlimited. Together with the low weight of the material (3-4 times less than steel), all other properties ensure cheap delivery without the use of long vehicles, as well as high ease of use.
Foundations are not exposed to open flames and high temperatures during a fire, which is why low heat resistance is not a significant drawback. High flexibility of reinforcement can only be important when working in structures that have nodes of concentrated influences, for example, when installing grillages. However, the resistance of concrete to bending loads can be restored by laying a relatively small amount of steel reinforcement, or simply by increasing the number of piles.
The corrosion resistance of fiberglass is much more important for foundations. It is not so important for subsequent waterproofing and waterproofing of concrete; however, the susceptibility of strip foundations to rupture due to an increase in corroding metal in volume can be ignored in the case of using polymer reinforcement. Fiberglass is optimally suited for constructing floating foundations in areas without drainage and with a high content of chemically active compounds in the perched water. Even under normal conditions, the use of fiberglass reinforcement makes it possible to reduce the protective layer of concrete to a minimum of 15-20 mm, thereby making it possible to move the reinforcement to the zone of maximum effective load absorption.
Calculation of composite reinforcement
While the methods for calculating steel reinforcement are well mastered by most builders, the design of foundations with fiberglass reinforcement is still considered an insufficiently covered topic. The reason for this is the different physical and mechanical properties of the reinforcement, which have not yet been taken into account in most current building regulations. The simplest way to calculate composite reinforcement is the equal-strength replacement method, in which steel rods are replaced with fiberglass rods with a standard size reduction of two values (that is, 8 mm instead of 12 mm or 14 mm instead of 18 mm). However, it is recommended to carry out the calculation of complex foundations according to the general scheme from scratch, so as not to lose sight of the significant difference in the value of the elastic modulus.
The first part of the foundation calculation contains the determination of the impacts on the foundation of the building and is performed in the same way as for reinforced concrete structures. The second part begins with determining sufficient cross-sectional dimensions of concrete structural elements and here the first differences can be observed. Since the tensile strength of fiberglass reinforcement is higher and the protective layer is minimal, the sufficient cross-sectional area is 25-30% lower than the standard minimum for a reinforced concrete product with an equal cross-section of the reinforcing elements. This does not apply to determining the width of the lower plane of the foundation, which is always determined by the current loads and the supporting capacity of the soil. Therefore, when reinforcing with composite reinforcement, it is beneficial to pay attention to foundations with complex sections.
The next stage is the choice of an equivalent replacement for steel reinforcement, which consists of preserving not only strength, but also all other physical and mechanical properties. The main nuance is that fiberglass reinforcement experiences 3-4 times greater linear elongation before it ceases to resist destructive effects. This means that the total cross-section of the reinforcing elements in the zone of bearing tensile loads must be correspondingly higher than when using steel reinforcement. The benefit from using fiberglass reinforcement in this case is expressed only by high tolerances for crack opening - for polymer reinforcement, contact with air or moisture is not critical, but one should not lose sight of the effect of frost forces on concrete. The general trend is this: the results of saving on the volume of concrete mixture should be directed to strengthening composite reinforcement in designated areas.
Rules for working with material
The differences in working with polymer reinforcement lie not only in the calculation method, but also in the methods of processing the material. In particular:
- Cutting fiberglass rebar should be done with either a hot cutter or a bolt cutter. Sawing polymer reinforcement by any means leads to the formation of harmful microscopic chips.
- Bending of reinforcement is allowed only in the manufacture of structural reinforcement elements. It is performed by heating the bent section to 100-120 °C using an electric hair dryer, followed by natural cooling after the product takes the required shape.
- When storing composite reinforcement, it should be protected from direct sunlight and high temperatures.
- When unwinding the reinforcement, its high elasticity should be taken into account. To relieve tension in the coils, the end of the reinforcement should be temporarily secured to the coil body with a meter-long piece of chain. If the coil is supplied without a coil, before cutting the clamps, it is necessary to secure 2-3 wire rings on the coil that do not prevent the rods from slipping.
Knitting spatial reinforcing structures
The process of assembling a frame from glass-polymer reinforcement is decidedly different from knitting metal. The root of most of the differences is the almost unlimited length of the rods: parallel bundles of rods are used extremely rarely. Because of this, it is much more convenient to knit the frame for the entire product in place and then load it into the formwork. This is also facilitated by low weight and resistance to corrosion: to preserve the fiberglass reinforcement, it is enough to just cover it from sunlight.
The preparation of frame parts, as in the case of steel rods, should be done before assembly begins, that is, all work is carried out primarily using the manufacturing method. The joining of rows at corners and junctions should be done by knitting crosses, and if necessary, increasing the moldings should be done by parallel tying with an overlap of at least 20 diameters. The crosshairs are knitted by braiding each of the perpendicular rods into a ring that tightens the reinforcement together. For parallel binding, 3-5 encircling clamps are installed in 2 turns. You can use both nylon ties and PET tape with its subsequent heat shrink for these purposes.
If it is necessary to include anchors of complex shape in the reinforcement, they are bent from metal, or factory-bent products are used in those joints of the structure where fiberglass reinforcement can do its job. In this case, it is necessary to increase the thickness of the protective layer at the installation site of the steel elements, and to bind dissimilar materials using polymer wire.
The foundation is the foundation of a structure that supports the main load. For this reason, it needs to be built from durable materials with good wear and tear. Particular attention should be paid to the fastening elements that will hold the structure and also protect it from premature destruction. The most suitable option is fiberglass reinforcement for the foundation. This is a new material that has recently become very popular. But first, it’s worth considering its advantages and important features.
Fiberglass reinforcement is a whole system of glued glass fibers. A polymer composition is used as a binder.
Typically, the reinforcement has the form of a rod, which has several constituent elements:
- main trunk It has a core that consists of parallel fibers. They are glued together using polymer resin. This ensures high structural strength;
- outer shell. The sheath fibers are wound around the AKS barrel in a spiral sequence. Sometimes sand spraying is used.
Advantages and disadvantages
Fiberglass reinforcement is an excellent option for strengthening the foundation. This material increases its strength, increases service life and allows it to withstand high loads.
If you are thinking which reinforcement is better - fiberglass or metal, it is worth considering important positive features of composite reinforcement over steel:

Do not forget about the disadvantages of composite products:
- Fiberglass reinforcement has a low modulus of elasticity and can be easily bent. During the construction of the foundation and paths, this drawback is not noticeable. But if the products are used in the construction of floors, then this nuance should not be missed; it is important to carry out all the necessary calculations;
- The products have an insufficient level of heat resistance. You should not combine fiberglass reinforcement with concrete mortar under strong temperature changes, otherwise it may completely lose its binding properties;
- fragility. Over time, composite products wear out and begin to deteriorate; exposure to an alkaline environment also has a huge impact on rapid wear. But manufacturers, in order to increase the service life of fiberglass reinforcement, began to add rare earth metals to its composition;
- not intended for welding.
Reinforcement calculation
When building a foundation with your own hands, it is important to correctly calculate the necessary materials, including fiberglass reinforcement. The calculation must be carried out in accordance with the following important nuances:
- The correct determination of the base length parameters must be carried out. When taking measurements, it is necessary to take into account the length of the internal load-bearing partition;
- it is required to calculate the length of the reinforcing rods. It should be taken into account that the reinforcing elements will be placed in several tiers;
- you need to determine the number of places with connections. Composite products are connected not by welding, but by overlapping. For this reason, 100 cm are added to the area of \u200b\u200beach corner;
- calculations must be made for cross connections.
To understand exactly how the calculation of fiberglass reinforcement bars is performed, it is worth considering an example using the parameters of a house with a base size of 12x12 meters, which was made using tape technology.
The calculation will do the following:
- the perimeter of the house is calculated. P = 2*(12+12) = 48 m;
- the total length of the reinforcement elements, which are stretched into two tiers of 4 edge bars, will be calculated as follows - D = 48 * 4 = 192 m.
- the number of jumpers must be calculated taking into account the minimum permissible run-up of 0.5 meters. For example, it looks like this, P \u003d 48 / 0.5 \u003d 96 pieces;
- calculations of the perimeter of the frame (500x500 mm) are required. Pk = (0.5+0.5)*2 = 2 m;
- calculations are made of the length of the reinforcing rings - Dk = 96 pcs * 2m = 192 m. In this case, trimming must be taken into account - 192 + 5% = 202 m;
- as a result, it will be required - 192 + 202 = 394 meters of a product with the same profile;
- it is worth calculating the required number of clamps for knitting - X \u003d 96 pieces * 4 \u003d 384 pieces.
In order for the composite material to protect and strengthen the foundation, it is recommended to follow important recommendations when working with it:
- Rebar cutting is done using a hot torch or bolt cutter. Sawing polymer reinforcement products with any other devices causes the formation of harmful microscopic chips;
- bending of reinforcement is allowed only in the manufacture of structural reinforcement products. This process is performed using an electric hair dryer; this tool heats the bent area to 100-120 0 C, and then, after taking the required shape, everything is cooled;
- the fittings should be stored in a cool, dark place, protected from sunlight;
- When unwinding coils with rods, it is recommended to take into account the degree of elasticity of the composite material. To relieve its strong tension, one end of the reinforcement must be secured for some time to the coil body using a meter-long piece of chain.
How to reinforce a foundation with fiberglass reinforcement
Fiberglass reinforcement is often used for strip foundations. It strengthens it, enhances its strength. But in order for the reinforcement process to proceed correctly, it should be approached with all responsibility.
Preparation
When using composite products for the base, it is worth preparing the necessary tools for the job:
- to take the required measurements you will need a tape measure;
- Bulgarian. This tool is needed for fitting and cutting fiberglass rods;
- personal protective equipment;
- water level;
- plastic clamps. They are necessary to connect the rods.
At the preparatory stage, you need to dig a trench. It is carried out according to the data specified in the project of the future structure. Important features of earthworks include:
- After digging the trench, it is recommended to level and compact the bottom well;
- then sand is poured in the form of a layer, its thickness should be 10-15 cm;
- the layer is watered and thoroughly compacted;
- crushed stone is poured on top of the sand with the same thickness as sand and thoroughly compacted;
- As a result, a kind of cushion of sand and crushed stone is formed at the bottom.
It is important to do everything correctly. The bottom of the trench should be perfectly flat so that after laying the fiberglass reinforcement there are no distortions. This will require the use of a water level.
Construction of formwork
For a strip foundation, formwork is required; it gives it the required shape and protects it from distortions. It is made from boards that are connected in the form of shields. It is recommended to use nails and screws for fastening. The caps of fasteners should be located on the inside. Additionally, the structure should be strengthened with special spacers.
The surface of the formwork walls is covered with polyethylene film, which is attached using a construction stapler. The use of film is desirable; it will keep the boards clean and also prevent liquid from leaking out of the concrete mixture.
On the walls of the formwork it is necessary to mark the level to which the concrete solution will be poured. It will also serve as a guide when installing a frame made of fiberglass reinforcement. To get everything right, you should use a water level.
Features of the construction of a frame made of reinforcement
After installing the formwork, reinforcement must be carried out. When constructing a frame, the following important conditions should be observed:

After constructing the frame, the concrete mixture can be poured. It is recommended to pour the solution carefully; it should completely fill the space between the frame elements. Be sure to periodically pierce the concrete with a metal rod, this will eliminate air voids.
In the press and numerous articles on Internet sites, they write a lot about composite reinforcement as the latest technology for the production of building materials. Although already in 1941 the idea of reinforcing concrete structures with fiberglass reinforcement was substantiated by the brilliant Soviet scientist Burkov. Western countries became interested in this technology only 40 years later.
What is composite reinforcement
These are high-strength polymer rods with corrugated or smooth outer surfaces made of non-metallic fibers bound into a bundle. Epoxy or polyester resins are used as binders. The most common polymer composite consists of inorganic glass fibers; this is fiberglass reinforcement. Basalt and carbon fibers are used less frequently; the resulting types of reinforcement are basalt-plastic and carbon-fiber reinforcement.
GOST 31938-2012 “Composite polymer reinforcement for reinforcing concrete structures” applies to the production of ASK in Russia.
Unfortunately, there are no official regulatory documents on the technology of its use, which significantly hinders its use in construction. Even among professional builders, some are not sufficiently aware of this issue.
Advantages and disadvantages of ASK

- low value of the elastic modulus, therefore the use for reinforcing structures subject to bending (high pile grillages, floor slabs, etc.) is determined by a separate calculation;
- low heat resistance. The physical and mechanical characteristics of ASA sharply decrease at temperatures ≥ 200°. But when constructing foundations, this practically cannot happen; in order to heat the ASC to such a temperature, the concrete surface must be heated to 600° for quite a long time.
When purchasing ASK, you need to pay attention to the appearance of the products: the absence of chips, cavities, dents and delaminations. A certificate is required.
Types of ASK reinforcement and areas of application in the construction of private houses
- internal, when installing frames and meshes inside structures or adding reinforcing crushed fibers to the concrete mixture;
- external, when specially produced types of ASK create a protective barrier around the structure, impenetrable to water and air;
- a combination of steel and ASK reinforcement is usually performed under heavy loads on the foundation structure.
In private housing construction it is used in the following structures:
- strip, slab and column foundations;
- buried pile grillages;
- frames of bored pillars;
- laying foam concrete and aerated concrete blocks (excluding reinforcement in the corners);
- enclosing concrete structures.
Reinforcement of foundations with fiberglass reinforcement
General rules for all types:
- ASC can be used for almost all types of foundations of low-rise buildings: houses, cottages, garages, bathhouses and other permanent structures;
- especially recommended for the construction of houses up to 3 floors on strip and columnar foundations;
- reinforcement cages are installed in accordance with the recommended technology for the adopted type of foundation;
- the frame consists of a lower and upper working periodic ASK with a diameter of ≥ 12 mm, vertical rods of ribbed or smooth cross-section with a diameter of 6...10 mm and the same transverse ones on the lower and upper meshes;
- the spacing and diameter of the rods are similar to steel reinforcement, but recalculated downwards according to the strength indicators of the ASK;
- connections of rods at intersections are made with plastic ties;
- special attention is paid to the design of the corners; the joining of the rods is carried out using L-shaped blanks, with sides ≥ 50 times the diameter of the reinforcement used. It is impossible to bend the workpieces at right angles on your own; this requires a special device. The pitch of the transverse rods is halved. It is allowed to use blanks made of steel periodic reinforcement;
- the protective layer is provided with special plastic linings;
- an important point is the maximum avoidance of bending effects; for this, it is recommended to lay a reinforced layer of class B15 concrete with a thickness of ≥ 10 cm on the underlying layer of sand and crushed stone;
- It is recommended to complete all excavation work immediately before subsequent work. Interruptions in the construction of the foundation are not permissible due to the risk of soil soaking and a decrease in its strength characteristics. If this condition cannot be met, the foundation is covered with a tarpaulin or plastic film. If moisture does seep in, the wet soil layer is removed by strengthening the cushion.
The most common reinforcement of strip foundations is fiberglass reinforcement. Selecting ASK with equal strength to frames made of steel reinforcement is guaranteed to ensure the reliability and durability of the foundation structure due to its successful resistance to negative external influences and the absence of corrosion.