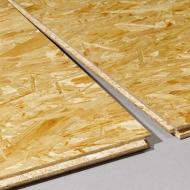
osb is used. Technical characteristics of the OSB board and harmfulness - for novice builders
Oriented strand board has recently appeared on the construction market - it replaced the previously popular chipboard. The material has outstanding technical data due to the multi-layer structure and special manufacturing technology. Information with specific numbers will help to understand the features of the material and the level of its safety.
An accurate knowledge of the technical characteristics of the OSB board and the level of its harmfulness will help to understand how expedient its use in construction is. The raw material used in the manufacture of oriented strand board is large-sized wood shavings. It is bonded with waterproof phenol or formaldehyde resin under pressure and high temperature.
OSB boards are made from large-sized wood shavings
The predecessor of this material is chipboard. Their main difference is the location of the chips in the layers. OSB is characterized by a transverse direction in the inner part and a longitudinal direction outside. In total, three or four layers are made with alternating particle directions. This allows you to achieve special strength parameters. As a result, chipboard is gradually replacing a more progressive analogue.
The chips underlying the oriented slab have a length of 7.5 to 15 cm. The norm of the width and thickness of the internal particles is 1-1.2 cm, 0.5-0.8 mm, respectively. Smaller chips are screened out and used to produce less durable chipboard. Pine or aspen is used as raw material. Modern equipment and the latest technologies make it possible to achieve maximum uniformity of the composition of the slab in all directions. Qualitatively made material has no cracks, voids and chips.
Depending on the strength, manufacturers divide products into main classes:
- OSB 1 - belong to the low class. The area of their use is dry rooms and structures that are not given a special load, for example, sheathing or furniture.
- OSB 2 is the middle strength class. They can be used both as sheathing and for load-bearing structures, but in dry rooms. For example, it can be partitions inside the room.
- OSB 3 - high class. Operation under good loading and at the increased humidity is possible. Exterior cladding of the building.
- OSB 4 - the plate has special strength characteristics: it is designed for a humid environment and constant intense mechanical stress. Sheathing of houses without additional cladding.
In addition to the alphanumeric classification, there are separate types of oriented strand boards:
- Laminated - additionally processed with laminate components. The characteristics of OSB boards make it possible to successfully use it for flooring and furniture manufacturing. Of these, you can make interior partitions, use for formwork several times.
- Grooved - notches and protrusions are applied to the ends of such plates. By driving them into each other, they get a tight connection without gaps.
- Lacquered - used in the furniture industry.
Tongue-and-groove plates have recesses and protrusions at the ends for tight connection with each other
The material can be produced both coated and uncoated. As a facial treatment, paint, compositions against moisture and fire, bioprotection are used.
Production technology and scope of OSB boards
Knowing how oriented strand board is made will help you better understand how and where it can be used and what the benefits of this material are. Production stages:
- 1. Selection of raw materials. At this stage, the trunks of a small-sized non-business tree are sorted.
- 2. Sawing. Selected trees are cut into small pieces, which then serve as blanks.
- 3. Grinding. The blanks are placed in a special machine, which crumbles the wood into chips. It falls apart on a conveyor belt. The size of the chips can be adjusted depending on which slab you need to get.
- 4. Drying.
- 5. Sorting of wood chips. Small chips are separated from large ones.
- 6. Bonding. A binding element is added to the selected chips of the required size - phenol or isocyanate. It gives the future building material moisture resistance and strength. Paraffin is added to the mixture, all this is mixed in a special drum.
- 7. Formation of the plate. The shavings are laid in layers. This is done by the machine with the help of scales and magnets.
- 8. Pressing. The resulting tape is subjected to a pressure of 5N/mm2 at high temperature. The elements are firmly bonded to each other, a single plate is obtained. After cooling, pieces of the desired size are cut from it.
The range of application of OSB is wide:
- OSB-4, due to its strength and moisture resistance, are used for the construction of frame houses and outbuildings. From the material, inexpensive temporary housing is obtained.
- Arrangement is the best option for an oriented slab. It holds shelves with heavy objects, shelving, heating radiators well.
- Walls, ceilings and floors are sheathed with building materials during the interior decoration of buildings. Ideally even, smooth surface is convenient for plastering, painting, wallpapering.
- A large scope of application is the furniture industry, the production of packaging. Strength, low price and low weight make oriented strand boards suitable for the manufacture of upholstered and cabinet furniture, shipping containers.
The material is used in combination with both wooden and metal structures.
This material is widespread in construction due to its attractive properties from the point of view of the builder.
Thanks to the large chips in the composition, OSB boards perfectly hold any fasteners
- OSBs are easy to process - in order to work with them, it is enough to have a standard set of carpenter's tools at hand. The plate can be sanded, cut, planed, sawn. It will not crumble or break if holes are punched or drilled in it.
- Large chips give a high holding capacity. Thanks to its content, nails can be driven into the slab at a distance of six millimeters from the edge. The plate holds any fasteners well without chipping. Carpenter's glue can be used as its fastening.
- The average density of the board is 640 kg/m3. This also includes the strength of the material, which depends on the elasticity:
- Moisture resistance is the level of swelling in thickness after the board has been in water for 24 hours. The table shows the percentage of the total volume:
- Fire safety. Since boards are made of wood shavings, they are highly flammable and burn well. For this reason, it is recommended to use OSB in combination with non-combustible insulation or facing materials. For example, mineral wool or metal siding.
During construction, it is better to use non-combustible insulation or facing materials.
OSB is convenient to use in construction, but together with strong supporting structures and fire protection. The high level of elasticity of the plates allows them to tolerate tremors well. Compared to stone, they win in this indicator. The disadvantages include the need to use a respirator during installation and processing to protect against small chips and fumes from the resin.
Hazard level of OSB boards for human health
Sellers boldly call this material environmentally friendly. At the same time, you can find a lot of information that NDEs are terribly harmful to health. It is not difficult to understand the essence of the matter. The composition of oriented slabs includes types of resins:
- phenol-formaldehyde;
- melamine-formaldehyde;
- urea-formaldehyde.
They are obtained synthetically and give the boards high-tech properties. Hazardous to health during further operation as a building material, OSB will be if the rules of manufacturing technology are not followed. To avoid purchasing low-quality products, check the certificates when buying.
In Russia, the European standard DIN EN120 is recognized, which classifies boards with chips according to the level of formaldehyde content in them, a substance that produces harmful fumes. The classification looks like this (calculation per 100g of dry matter): E0 - up to 6.5 mg, E1 - up to 10 mg, E2 - 10-20 mg and E3 - up to 30 mg.
When using OSB for exterior decoration, there is nothing to be afraid of, because. the concentration of released vapors in the air will be negligible. The second and third types are strictly forbidden to be used for interior cladding of residential premises, because. the level of vapors released into the room will exceed the permissible norm. E2 and E3 are suitable for attics, sheds and cabins.
According to the rules of production, all products such as chipboard must be tested for the level of synthetic resin content. According to its results, a corresponding certificate is issued. Pay attention to the smell of building materials: if it is sharp, like formalin or plastic, the product is toxic and cannot be used indoors.
OSB is a material with good performance, in all respects suitable for construction. By comparing it with other options and weighing all the pros and cons, you can easily make the right decision.
The material was prepared with the participation of Soppka specialists
- What is OSB made of?
- European and American OSB classification.
- Why OSB in a frame pie.
- How to protect OSB from destruction.
- OSB on the facade - finishing methods.
What are OSBs made of?
OSB boards appeared in our country only ten years ago, but they have been known in the world for more than three decades, since the frame technology for building houses was invented. A completely new material was needed to cover the frame: durable and at the same time light, reliable and easy to install - neither natural wood nor chipboard fit these parameters. This is how OSB, or OSB (Oriented Strand Board), was invented. It is made up of layers of wood shavings. The main binders are phenolic resins combined with paraffin; in Europe, melamine binders are used for boards used in furniture production. In the outer layers, the chips are laid along the plate, and in the inner - across. The mutually perpendicular arrangement of the chips makes them more resistant to external influences. It can be said that with a minimum thickness and low weight, OSB achieves maximum strength indicators, and it is this material that gives rigidity to the entire structure of the frame pie. At the same time, just OSB may turn out to be the most vulnerable link in the entire structure - the participants of our portal were convinced of this from their own experience. We will analyze the most common OSB problems and try to solve them with the help of experts.
European and American OSB standards
There are two classifications of OSB boards. According to the European standard EN 300, they are divided into four classes.
- OSB1 - boards that are used in dry conditions; they make furniture, upholstery. This is a non-structural material.
- OSB2 - used indoors in dry conditions as a structural board.
- OSB3 - used as a structural board in a humid environment, including outside structures. Due to the optimal ratio of cost, moisture resistance and strength, this material is most in demand by builders of frame houses at FORUMHOUSE, including for facade cladding.
Urgenz Member of FORUMHOUSE
I see no reason not to use OSB on the facade. It looks great (there is a texture, not a smooth sheet), light (ease of installation), it lasts much longer than wood.
- OSB4 is already a building board for load-bearing structures with increased mechanical loads and high humidity.
OSB made in the USA and Canada are divided into three classes. Criterion - the level of water resistance of the binder chip substance:
- Interior - for internal structural work in dry conditions.
- Exposure 1 is a structural board that withstands short periods of exposure to damp conditions, so it can be used indoors in wet areas and outdoors (provided it is finished with a different material).
- Exterior - withstand alternating cycles of wetting and drying, contact with the ground, prolonged exposure to adverse weather conditions.
The following American standards roughly correspond to European standards:
- OSB2-Interior;
- OSB3 - Exposure 1;
- OSB4 - Exterior.
OSB in frame construction
Due to the popularity of frame houses, OSB boards are one of the most discussed materials in FORUMHOUSE. The debate continues about how the “correct pie” should look like, how to reduce its cost without compromising the strength of the structure, what is the role of OSB in the frame structure, whether OSB can be used for facade decoration.
On the scheme proposed for discussion by a FORUMHOUSE participant BulKonst, two options for a frame pie are shown: in Figure A - a classic pie, in Figure B - a budget version of the classic version (saving 1.5 times).
The idea to reduce the price of the pie by removing from it such an element as sheathing the frame on the outside with OSB boards did not meet with understanding at FORUMHOUSE, because "in construction, the miser pays three times." Namely, OSB gives the reliability of the entire structure.
Svidig Member of FORUMHOUSE
Without OSB, the house can develop.
OSB-plates showed their best side during the earthquake in Japan: frame houses survived, although wooden and stone houses collapsed in the neighborhood.
Solovyov Artem Project Manager Soppka OSB Protektor
The main purpose of OSB boards is to stiffen the structure.
It is OSB that gives the house the opportunity to stand for several decades. But this is if the pie is mounted correctly. The technology of frame housing construction, taking into account local conditions, is only being created in Russia, it is a little more than ten years old. Therefore, there are no exact, scientifically verified technologies of frame housing construction in Russia yet. In essence, for now, each construction company has more or less its own technologies - therefore, there is always the possibility that the ventilation will be done incorrectly, and unprotected OSB boards will be in an environment with high humidity and become infected with mold or fungus, which will spread further to the insulation. and frame.
View of the wall of the frame house after the dismantling of the siding. Minnesota, USA.
How to protect OSB
FORUMHOUSE member with nickname fast and furious found that the street side of his house "went a lot" when he lived in it for 4.5 years. It turned out that there was a complete destruction of the OSB.
Fast and Furious FORUMHOUSE member
I read from SIP builders how wonderful they are, SIP panels. And they don’t burn in fire, and they don’t drown in water, and a pood weight hangs on one self-tapping screw. Only the fungus eats it calmly and makes fun of me.
For a long time it was believed that only the frame should be covered with bioprotection, and OSB-plates and other structural elements do not need it. This is wrong - OSB boards were not covered with bioprotection simply because until recently there was no composition that would have good adhesion with OSB boards.
The house is treated with a specialized fire-retardant compound
Artem Solovyov
In a frame house, everything is interconnected. The frame holds the house, and OSB makes the frame stronger. Even the counter-lattice on which the OSB boards are attached must be treated with a bioprotective composition. To protect each element of the structure, there are products.
OSB for facade finishing
birdofprey
If there is a desire to throw money away, then you can use the OSB as a finish, and a complete one.
For facade decoration of the house on OSB boards, you can use clinker tiles, ceramic tiles imitating brick, siding or imitation timber. Also, the plates can be plastered.
If the choice of finishing for OSB boards fell on plaster, then there may also be problems with the choice of additional material. Such work cannot be carried out directly on OSB, the plates must be protected.
Nadegniy Member of FORUMHOUSE
According to the OSB, the plaster will hold for some time, cracks at the joints of the OSB will appear in the first winter, the edges of the OSB sheets will gradually swell, and the finish will darken with them.
Here are the variants of the "plaster pie" that have been successfully used at FORUMHOUSE.
If overlays were made:
- OSB + primer + elastic plaster + overlays.
- OSB + concrete-contact + elastic plaster + overlays.
- OSB + primer + reinforcement. mesh + plaster + overlays.
If pads were not used:
- Wet facade: OSB + PPS (expanded polystyrene; PSB-S 25F) + base reinforcing layer + decorative plaster.
- OSB + reinforced mesh + primer + putty + elastic plaster.
- OSB + 2 layers of glassine + mesh + plaster.
OSB boards can be easily painted. It is to paint - a simple varnish coating is not good, the varnish does not protect against ultraviolet radiation, it is necessary to give the tree color. Now, by the way, paints have appeared that are several times cheaper than European ones.
Artem Solovyov
The sun will eventually burn out the resins from the surface of the OSB board, the chips will move away, cracks will appear, into which moisture will get. Naturally, with the change of seasons and from constant freezing and freezing, the wood chips will move away even more.
An example of finishing a house with facade paint
Microorganisms form in these cracks. The gray color of the OSB board indicates that the board is ALREADY infected.
Should boards be puttied before painting? Perhaps, the structure of the OSB, untouched by putty, looks better than a smooth sheet and more resembles the original half-timbered.
Members of our portal, who have extensive experience working with OSB, recommend choosing a slab for facade decoration responsibly. Regardless of which grade of OSB you choose, make sure that their top layer does not contain bark. If there is still bark on the leaf, it is carefully separated with a sharp tool and torn off.
OSB plate are made from large wood chips (chips can reach 18 cm in length, and their width ranges from 6 mm to 4 cm). A special resin is used as a binder (which contains urea, formaldehydes and phenol). Water resistance OSB board achieves through impurities during the production of synthetic wax. In addition, a salt of boric acid is added to the composition.
OSB panels for building houses
Particular resistance and rigidity is provided by the production technology, which is based on the multidirectionality of the stacked layers of raw materials. It is understood that the outer layers are laid so that the chips lie along the finished sheet. And the inner layers are stacked in such a way that the chips lie across the canvas.
All elements are interconnected by means of hot pressing. Thanks to all these nuances of production, this material receives a number of advantages over other types of similar plates.
OSB plate - dimensions, specifications
Sheet thickness can vary from 8 mm to 25 mm. Conditionally plates can be divided into three groups.
- The first group (thin canvases) - 8, 9 and 10 mm, OSB plate weight - 16.6 kg, 18.4 kg and 20.6 kg, respectively.
- The second group (medium web thickness) - 12 and 15 mm, OSB plate weight - 24.1 kg and 30 kg.
- Third group (thick canvases) - 18, 22 and 25 mm, OSB board weight - 35.3 kg, 43.1 kg and 48.8 kg.
OSB board size:
- 2440x1220 mm. one of the most popular size of osb slab, most often used in construction;
- 2500x1250 mm. this size of OSB boards, as a rule, have cheaper European counterparts;
- 2440 x 590 mm. a rather rare size of osb slab with grooved edges, usually used when creating the base of the floors.
When purchasing material not by the piece, but by pallets, it should be noted that the thinner the canvas, the more pieces will be on it. So 8 mm canvases will fit 120 pieces, and 25 mm - only 38 pieces.
OSB plate - types of material:
The division of this material into types is carried out according to such parameters as strength and moisture resistance. Based on them, the following options are distinguished:
OSB-1
This type has the lowest rates of resistance to moisture, as well as mechanical stress. It is most suitable for the production of furniture elements, as well as for use as a material for packaging and transportation.
OSB-2
This type has all the same low resistance to moisture, but it has a higher mechanical strength. Most often used in the process of manufacturing load-bearing structures (floor beams).
OSB-3
This type is endowed not only with sufficient strength, but also with good indicators of moisture resistance. Therefore, it is used in exactly the same way as the previous type, only with the possibility of installation in places with high levels of humidity.
OSB-4
This type of material is endowed with the highest rates of all the above properties. That is why there are many options for its use. Can be used in situations with the most stringent conditions and requirements.
OSB plate: advantages
- Doesn't flake or crumble.
- It has a homogeneous structure.
- Price availability.
- Absolute harmlessness in the ecological plan.
- Finished elements have higher rates of elasticity and flexibility (compared to brick or masonry).
- Do not collapse under the influence of sudden changes in temperature.
- Easy to handle and finish.
- The peculiar structure allows much more rigid fixation of metal elements in the canvas (nails, self-tapping screws, etc.).
- It is possible to use the tongue-and-groove connection option.
Flaws
- When using canvases indoors, a moment with an external finish of the canvases is required (to ensure an aesthetic appearance).
- When cutting, the use of respirators is mandatory. This is due to the presence of resins harmful to the respiratory tract.
Scope of OSB boards (OSB)
As such, there are a myriad of areas and use cases. We list the most common.
- Lathing at the device of a roof.
- OSB is used for the floor, namely for its quick alignment for laying parquet or laminate.
- Installation .
- Sheathing of facades of buildings.
- It is used as structural elements during the construction of buildings in one or two floors.
- For production .
- Construction of counters, stands and other things.
- Covering floors inside motor vehicles intended for the carriage of goods.
- It is used for the construction of seasonal housing or non-residential premises (summer cottages, garages, working outbuildings).
Sheet building materials are used in frame housing construction, with dry leveling of planes. One of these materials is OSB board (OSB, OSB). She pressed, GKL. And all because with good technical characteristics, it has a low price.
What is OSB board and OSB
One of the sheet building materials is OSB (also called OSB). The name is an abbreviation of the full name of the material - "oriented strand board". That is, it is correct to call this material OSB. The second name - OSB - comes from the transliteration of the English version of the name - OSB ( oriented strand board). English letters were simply replaced with similar ones in Cyrillic.
OSB is a multilayer material (3 or more layers). Each layer consists of wood, ground into chips, mixed with resins. Wood chips are used long and thin (several millimeters thick, up to 7 cm long). The chips in the layers are located in different directions: the outer layers have a longitudinal orientation, the inner ones have a transverse orientation. This results in high elasticity and dimensional stability. Various resins are used as a binder. They give the material water resistance, but contain formaldehyde. It is the content of this substance that stops many from using OSB. But, if the material is produced in accordance with GOST, the formaldehyde emission does not exceed the performance of wood. But this can only be verified in laboratory conditions. So the ordinary buyer can only rely on the inspection authorities. Or choose another material.
Types of OSB
Depending on consumer properties, oriented strand boards are produced in several types:

If you need moisture-resistant OSB, carefully consider the choice of manufacturer. Be prepared for the fact that OSB 3 is more expensive than non-moisture resistant brands. Even more money will have to be paid for OSB 4. We do not recommend looking for cheap material. Too many complain that the purchased OSB 3 swelled by 3-8 mm from moisture, in some cases it even bloomed or overgrown with fungi. All this is due to attempts to reduce costs. To do this, use fewer disinfectants, a cheaper binder. Chinese manufacturers instead of pine chips put hardwood, which is easily affected by fungi and diseases.
Properties and specifications
OSB boards compete with other sheet materials both in the field of construction (for sheathing frames, creating formwork) and in the field of finishing (leveling walls, floors, ceilings). This is facilitated by the properties of OSB:
Once again, we draw your attention to the fact that moisture resistance and resistance to deformation are characteristic of OSB, which were made in compliance with the technology. Unfortunately, the Russian-made material is not of high quality. Less powerful presses are used, they try to save on the binder, do not apply markings. As a result, there are many examples of negative experience: plates swell from moisture, warp them, glue is washed out ... The way out is to look for plates of imported (Europe or USA) production. Due to the growth of the dollar, they now have considerable prices, there are very few of them on the market, but, if desired, you can find or order with delivery.
The situation is aggravated by the fact that in appearance it is impossible to distinguish moisture-resistant OSB3 from non-moisture-resistant OSB2 or 1. The latter cost much less. Unscrupulous sellers sell cheaper ones under the guise of moisture resistant ones. This is where trouble comes in. As a way out, you can do this: buy one sheet of OSB 3, check its behavior at high humidity. If there are no visible changes, buy a batch.
Application area
The properties of OSB make it possible to use this material as a building or finishing material. Here are the jobs it can be used for:
- Sheathing of frames and walls from the inside and outside.
- Floor and ceiling leveling.
- Flooring of a rough or finishing floor along the logs.
- Removable formwork when working with concrete.
- Solid crate under, metal tile, slate,.
- Production of SIP panels and thermal panels.
There is a constant debate among developers about how safe OSB is. In its production, resins are used that emit formaldehyde. Manufacturers claim that the release of this substance does not exceed 1%. Materials with such formaldehyde emission are considered absolutely safe. About the same amount of this substance emits wood. Therefore, such materials are allowed for the construction of children's furniture. In addition, OSB boards with an emission of 0.5% appeared. You can distinguish them by two criteria: the name contains the prefix Bio or Green and they are more expensive.
Please note that the level of formaldehyde emission must be controlled. Each batch of material must be checked, the actual parameters must be indicated in the accompanying documents. Despite all the arguments, not everyone considers this material to be safe, preferring to use natural material - boards. They are, without a doubt, an environmentally friendly material, but it takes longer to work with boards, they are more expensive. In general, everyone decides for himself whether to use OSB boards or not.
Dimensions of oriented strand boards
Since the purpose of the OSB board is different, different sizes can be convenient. The situation with the size of OSB boards is not easy. On sale there are constantly 1220 * 2440 mm and 1250 * 2500 mm. There are also formats 1250*2800 mm, 1250*3000 mm, 1200*6000 mm, but they are extremely rare on our market, although in many cases they are much more convenient to use. Having picked up the right size, you get rid of the need to “grow” the missing centimeters or saw off the extra ones. But there are not so many of them on the market, since these are imported plates, and now it is difficult to import ...
The OSB board can also be of different thickness - 9 mm, 12 mm, 15 mm, 18 mm, 22 mm, 25 mm. Each type of use has its own thickness:
- Sheathing of walls, ceiling - from 9 mm.
- Solid crate for roofing materials - from 12 mm.
- An OSB board from 15 mm thick will go to the floor.
Another of the applications of OSB boards is a removable formwork for concrete work.
OSB board is a convenient building material. It can be sawn with an ordinary wood saw, use a grinder with a cutting disc, a jigsaw. The material is well drilled, screw nails can be used without pre-drilling. But then their hats stick out, which is not always convenient.
Before finishing, the OSB board is coated with a primer. It is selected depending on the finishing materials - to equalize the absorbency and improve adhesion to other materials.
Construction companies, as well as furniture manufacturers, often list OSB boards or simply OSB as the materials used. This abbreviation usually does not mean anything to the average consumer. So, OSB - what is it, what is it used for, what are its advantages or disadvantages?
The name OSB stands for simply - these are the initial letters of the words orient strand board, which translates as oriented strand board. Also, boards can be called OSB panels, OSB sheets, or simply OSB or OSB.
Boards are made from flat wood shavings or chips. For the production of OSB boards, softwood raw materials are most suitable, but aspen, poplar, etc. are also used. Unlike other particle boards (chipboard, for example), chips are laid in OSB in a given direction. That is why such particle boards are called oriented. Since OSB boards consist of several (usually three) layers, the direction of the chips in the layers alternates, making these boards more durable.

To connect the chips to each other, resins are used, consisting of urea, melamine, waxes and other substances. The resin content in the composition is less than 10%, which makes OSB panels a conditionally natural material. Panels can be laminated or varnished for added protection.
OSB boards have found wide application in house building. In particular, they are part of the material used for.
OSB plate - these are sheets about 2.5 by 1.25 m in size. The thickness of the plates is different, it varies from 6 to 38 mm. For ease of installation, the plates can have machined ends according to the “groove-comb” principle.
Types of OSB
There are 4 types of OSB, they are all divided by strength and water resistance:
Pros and cons of OSB
The advantages of oriented strand boards include the following properties:
- price;
- strength;
- moisture resistance;
- ease of processing;
- no bundles;
- excellent holding capacity - fasteners in OSB hold an order of magnitude better than in chipboard.
What about security? There are misconceptions about human health. Someone says that it is a toxic material, that it cannot be used indoors, that OSB emits formaldehyde, etc. The vast majority of such misconceptions are complete fiction that has nothing to do with the true state of affairs. First, all panels are certified. An international standard E1 has been developed for materials used in housing construction. OSB boards with the appropriate marking are safe for humans. Secondly, conventional priming and painting completely blocks the release of any substances from the boards. Thus, they are as safe as possible for health and there are no obstacles to their use indoors.
There are completely safe OSB boards. The binders used in the production of EUROSTRAND® OSB 3 E0 boards from Egger do not contain formaldehyde at all. The binding element is not phenol-formaldehyde resin, but paraffin-wax emulsion and polyurethane resin.


Comparison of OSB and plywood
OSB boards can be compared with other materials and, above all, with plywood. They are similar in their qualities, but if there is a choice, plywood or OSB, then you should pay attention to the following facts:
- for the manufacture of OSB, shavings of fast-growing species are used; for plywood, more “noble” raw materials are needed - as a result, the cost of OSB is lower due to the price of raw materials;
- OSB boards do not delaminate;
- OSB has a more uniform structure and at the cut, the tensile strength of OSB is higher than that of plywood;
- the strength of plywood and OSB is approximately the same, but for OSB, the strength characteristics do not depend on humidity;
- OSB sheets can be produced in any size, the manufacturing process is easy to customize for specific needs;
- OSB boards are easily processed with any tools;
- in terms of weight and strength, OSB boards are more profitable than plywood.
So, OSB is a lightweight and durable building material that surpasses such eminent competitors as plywood in many respects. At the same time, the cost of OSB is lower, which makes this material the most promising on the market.