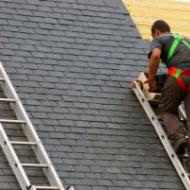
Making spiked joints with a milling cutter. A tricky way to cut the perfect round spike
Quite a lot has already been written about such tenon cutters, so I do not pretend to originality. But the thing in the workshop is definitely useful. Therefore, having assembled a tenon cutter for a straight box tenon, I decided to talk about it in my blog.
Such tenon cutters are usually made on the basis of a milling table or a circular saw. But, of course, options are also possible - depending on the invention of the master - on a band saw, a jigsaw machine, or even on a chainsaw!
I did not become original and made a device for cutting a straight box tenon for my router table (more about it here:).
Sometimes they use bearings and different guides to facilitate sliding, but I decided to do without them. The only condition is that the opposite edges of the table must be parallel. To do this, you can walk on them with a router with an emphasis on the other edge.
The first step is to cut out the base of the future tenon cutter from plywood. The dimensions of this base depend on the table itself - it must be wider than the table by the width of the side stops. I took stops of about 4 cm. The length of the stops should be the same or slightly less than the width of the table - then they will not wedge. I glued all the details of the tenon cutter with carpentry glue and fixed it with self-tapping screws - perhaps redundantly, but I wanted to.
All screw heads are recessed.
To select the correct position of the second stop, we put the workpiece with the first stop installed on the table, resting it (the first stop) against the edge of the table, apply glue to the second stop ...
And having laid a sheet of paper between the second stop and the edge, we fix it (the second stop) in this position with clamps. The gap left by the paper will be ideal for the tenon cutter to move freely along the edges of the table without dangling.
For purely aesthetic reasons, we cut the edge so that the stops are flush with the main part.
The carriage for our tenon cutter is ready
Next, a stop will be installed on this carriage, which can be adjusted and which must always be perpendicular to the direction of movement of the carriage. In order not to check this perpendicularity every time, I made a ledge with the right angles on the edge of the carriage.
On the same ledge, using the M8 bolt, I installed the handle from the adjusting mechanism of the office chair.
The handle is located exactly in the middle between the stops - this is another degree of protection against carriage jamming. The handle is quite grippy and secure. It also sets a safe position for the right hand. It is convenient to use it.
The stop is fixed with two M10 bolts with recessed heads and wing nuts. The stop can move along the ledge with the handle in both directions.
It is important that the plane of the stop is perpendicular to the plane of the carriage.
The carriage is made of 18 mm FSF plywood. I'm sure many are now choking - where such a thickness, it's some kind of monster! Well, yes, it could be made thinner, but I like things with excess strength where possible. Here is my feature.
Therefore, the cutter had to buy a special one. All characteristics and articles are visible in the photo.
We insert the pin into the resulting groove. I made it from textolite 6 mm thick.
The device is ready. The design is quite simple, it took longer to tell than to do))
The first run showed that in general the device works, but requires configuration
Careful adjustment requires the height of the cutter and the width of the tenon. After a while it started working.
It is more convenient to process parts in packages - at least two. At the same time, the outer parts have a hard time - a straight cutter mercilessly pulls out of them not just individual fibers, but entire layers. Therefore, the details must be processed, wrapping them on both sides with unnecessary bars.
See what happened to the parts that were external in the package. I don’t know how in magazines and videos they manage to process the details one by one. You can use spiral cutters - maybe this will solve the problem, but they are usually several times more expensive than straight ones.
Therefore, we simply wrap the workpieces on both sides and get an excellent result. Here it is also necessary not to lose sight of which side and in what sequence to process the parts so that they then form into a product.
In general, the result is not bad. These were test bars, but since it turned out well, I decided to finish the job and make a box.
Cut out the bottom of the box on a circular saw
And then another nuance came out - for grinding protruding spikes, a device for cutting a straight box spike should be equipped with a belt grinder or a disc grinder or something like that. An eccentric sander does not cope, filling up the edges. Otherwise, I'm happy with the purchase - it works as it should.
For a long time in joinery and carpentry, a tongue-and-groove connection has been used. Ancient architects, using this method, managed to create unique wooden buildings without a single nail or screw. And although a wide variety of hardware is now quite accessible, the articulation of individual parts of various structures by this method has not only not lost its relevance, but is also widely used in modern products and materials.
The principle of connection and its varieties
According to the design, all thorn-groove joints are made according to the same principle: a protrusion is made on one part, and a recess on the second. In terms of configuration and size, they are exactly the same. With a tight articulation of these two parts, a strong technological unit is obtained. During the construction of houses, such a connection prevents the shift of one part of the structure relative to the other; in the manufacture of furniture, it significantly increases the area on which the adhesive is applied, thereby providing additional strength to the product.
According to the geometric shape of the protrusion and recess, such joints are divided into two main types:
- rectangular section (sometimes with rounded edges of spikes and grooves);
- in the form of a trapezoid (also called "dovetail").
According to the number of spikes and recesses that need to be made for one articulation of parts, these connections are divided into:
- single-thorn;
- multi-thorn.
Important! Regardless of the number and geometric shape of the protrusions and recesses, they must be made only parallel to the wood fibers.
Application area
The thorn-groove connection has found application in many areas of our daily life. For example, when arranging the floors of rooms according to this principle, such familiar coatings as laminate, ordinary floorboard, chipboard, fiberboard or MDF boards are joined.
Wood, as one of the most environmentally friendly materials, is used to make a wide variety of furniture (from a simple kitchen stool to a designer set for a living room or dining room), roller blinds, blinds and much more. And all these products are mainly made using a spike-groove connection.
During the construction of wooden frame buildings, houses made of timber, when arranging the beam-rafter structure of the ceiling and roof, it is also impossible to do without arranging ledges and recesses.
Beam connection
A thorn - a groove in the connection of a beam is used both for arranging corner structures made of wood, and for longitudinal alignment of individual pieces. Depending on the dimensions of the section and the expected loads, the geometry and the number of protrusions and lugs are selected. For example, in the construction of wooden houses, one-stud connection is mainly used. And to increase the length of the bars of a small section using glue, a multi-thorn method is used.
Joining boards
Almost all owners of suburban real estate have long been fond of such material as lining, as a result of which they get an absolutely flat vertical surface. A spike-groove connection of boards is used for arranging floors, interior decoration of a house, as well as for external cladding of a building (naturally with an antiseptic coating).
The protrusions are tightly fixed in the recesses of adjacent boards, which prevents their displacement relative to each other. When arranging the floors, the tight connection of the tongue-and-groove boards between themselves prevents their displacement in the vertical plane (the floor turns out to be even) and significantly increases the heat-saving properties of the coating (there are simply no gaps between the boards).
Using a manual electric router
Arrangement of spike joints - minimizes labor costs and significantly reduces the time for carpentry work. Of course, this useful tool will not help when building a house, for example, from a bar with a section of 150 x 150 mm, since there are no cutters of this size for a manual router, and the power of this unit will not be enough to install them. But if you want to build furniture, small or door frames yourself, then such a tool is a must. Depending on the size of the parts to be joined and the geometric configuration of the connection, you get the desired cutter, or maybe two (one for cutting a groove, the other for making a spike). Milling tool adjusters, as well as guide bearings (usually included with these milling cutters), will help create projections and recesses that exactly match in size and shape.
DIY tools and fixtures
If you need to make some piece of wood product, then it is not economically viable to purchase an expensive electric milling cutter. Most likely, everyone in the household will have the necessary set of tools, and if they have to buy in addition, then quite a bit. In addition, additionally purchased devices may later be useful for minor repairs (for example, repairing wooden furniture). In order to make a thorn-groove connection with your own hands using only ordinary hand tools, you will need:
- wood saw (with fine teeth);
- joiner's thickness gauge (special device for marking) or a regular construction square;
- Ruler and pencil;
- wood chisel.
Self-made corner connection
As an example, consider how to make a spike-groove connection of two bars of the same section at a right angle using improvised tools. Let's say you need to connect 60 x 60 mm (they may well be suitable for making window frames for a summer house).
The thickness of the protrusion for a single-tenon connection (in accordance with the recommendations of carpentry handbooks) should be ⅓ ÷ ⅜ of the thickness of the bar (in your case it will be 20 mm). The length of the spike will be equal to the thickness of the bar (60 mm). The dimensions of the recess must correspond to the dimensions of the spike, so that it fits into the eye with force.
Attention! The spikes must be equipped on the vertical parts of the wooden structure, and the grooves on the horizontal ones.
The algorithm for performing work is quite simple:
- First, we mark out future protrusions and eyes. If you treat this process without due attention, then the spikes and grooves made may not match each other in size or relative position. There is also a danger that they will not fit tightly into each other. All this will significantly reduce the strength and reliability of the connection.
- Using a thickness gauge (or square) at a distance of 60 mm from the end, we draw a line on all four sides of both bars.
- Then, on two opposite sides and on the end, we draw two parallel lines at a distance of 20 mm from each other.
- Along the marking lines with a hacksaw, we cut the end to the transverse line, that is, to a depth of 60 mm.
On a note! So that the thickness of the cut (approximately equal to the setting of the teeth of the cutting blade of the hacksaw) does not affect the accuracy of manufacturing the connection, we install the saw blade from the outside (when arranging a spike) or from the inside (when making a groove).
- At the end of the bar with a ledge, we saw off the outer pieces of wood.
- With a chisel, carefully hollow out the inside of the recess.
- We insert the spike into the groove and check the connection made. If necessary, remove protruding defects with a chisel.
Finally
If you need to equip the spike-groove yourself, then it is best to practice on scraps of bars.
If the made protrusions and recesses exactly matched, and the articulation of the individual parts turned out to be strong, then you can start working on the prepared building material. Well, if the spike enters the groove too freely, or vice versa, then it is necessary to check the correctness of the markup again, conduct another training session, and only after that proceed with the implementation of the planned project.
In this article, we will introduce you to the process of cutting various joints with a hand router, consider the process of manufacturing such additional devices to increase labor productivity as tenoning templates and a dovetail wood cutter.
How to make a tenon groove with a manual router
To make this spiked connection, we need the router itself and the desktop itself. To facilitate the process, you can make such an additional device as a conductor.
The procedure is as follows:
- We install two rack limiters on the plywood sheet, cut out holes to fit the groove size for the drawstring and proleg. Rack stops must be fixed across the width of the router. They fix it across the working plane. To fix the longitudinal displacement, two other limiters are set at the ends of the intended location of the installation site of the carpentry machine.
- To move the workpiece along the length, we mount a pair of bars to the tabletop that correspond to the dimensions of the workpiece.
- We mark the axis and dimensions of the grooves. We install an additional device so that the markings on the workpiece and the conductor completely coincide.
- It is necessary to expose and fix the emphasis.
- Fix the conductor with self-tapping screws to the bars.
- It is necessary to take a straight cutter and set the depth of milling, taking into account the thickness of the manufactured jig. After that, it is necessary to fix the workpiece with a clamp and perform groove processing.
Getting Started to cutting spikes.
- With small volumes of production, it is best to do this on a circular.
- First you need to measure the depth of the groove, which will correspond to the length of the spike.
- We measure the resulting value on our workpiece. The length of the spike will be determined by the difference in values - the width of the workpiece and the length of the groove, the height of the workpiece and the width of the groove, divided in half. The resulting material residues should be removed to obtain a spike.
- After that, you should set the size on the machine equal to the length of the groove, taking into account its width. The circular saw should be fixed at a level equal to ½ of the difference in the width of the workpiece and the length of the groove from the tabletop line. Make a couple of cuts along the length of the spike.
- We fix the saw blade at a height equal to ½ of the difference in the heights of the workpiece and the width of the groove from the tabletop line. Two cuts are made from the end face of the workpiece.
- We start cutting. To do this, it is necessary to fix the circular saw by the value of the tenon length, while the distance from the disk to the stop must correspond to a value equal to ½ of the difference in the width of the workpiece and the length of the groove. We make two cuts along the width of the product on both sides.
- Adjust the distance from the cutting disc to the stop. It should be equal to ½ of the difference between the heights of the workpiece and the width of the groove. We make two cuts. We round the edges of the resulting spike with a carpenter's knife and clean it with sandpaper.
Tenon cutter for milling cutter
Tenoning templates come in a wide variety of configurations. They serve to facilitate the work of cutting out joints such as tongue and groove, as well as to speed up the work. With their help, you can make frames, drawer connections, cutting out various connections for furniture. The size of the groove, as well as the evenness of its edges, will depend on the shape of the tooth of the template. To make a do-it-yourself stud cutter, you will need guides with which the studs will be milled. They should be mounted on two opposite sides of the case in a checkerboard pattern, placed equidistantly. Under these conditions, they are ideally suited to each other.
Cutter for wood "dovetail"
They are most often used in combination with milling machines and machines for making grooves in hard and soft wood products. Manufactured from solid hard alloys.
Designed to work in tandem with cylindrical cutters.
How to choose a groove with a router
When doing this work, you need to know that its technique will directly depend on the location and size of the groove. If it is open, then your tool is attached to the tabletop, the workpiece is carried along the cutter. The accuracy will depend on the position of the bar and the height of the cutter. So that you don't have any flaws in the sampling process, always make a trial run on scrap wood. Sampling should be done in stages, you need to do this in several passes. After each pass of the cutting part of the router, in order to prevent its overheating, it is necessary to remove waste from the working surface of the countertop. This can be done using a template cut out of plywood, which should be walked over with a cutter with an upper bearing.
We hope that the information obtained while reading this article will be useful to you and useful for use in the household.
For full-fledged work with a manual router, in addition to the tool itself, the material and the corresponding set of cutters, it is necessary to have one more component - fixtures. In order for the cutter to form the workpiece in accordance with the master's intent - cutting the material exactly where it is required - it must be in a strictly defined position relative to the workpiece at any given time. To ensure this, numerous devices for a manual milling cutter serve. Some of them - the most necessary ones - are included in the instrument delivery set. Other milling devices are purchased or made by hand. At the same time, home-made devices are so simple that for their manufacture you can do without drawings, using only their drawings.
Parallel stop
The most used device, which comes with the kit for almost every router, is a parallel stop, which ensures the rectilinear movement of the cutter relative to the base surface. The latter can be a straight edge of a workpiece, a table or a guide rail. The parallel stop can be used both for milling various grooves located on the face of the workpiece, and for processing edges.Parallel stop for a manual router: 1 - stop, 2 - rod, 3 - router base, 4 - rod stop screw, 5 - fine adjustment screw, 6 - movable carriage, 7 - movable carriage stop screw, 8 - pads, 9 - screw stop stop.
To set the device in working position, it is necessary to push the rods 2 into the holes of the frame 3, providing the necessary distance between the support surface of the stop and the axis of the cutter, and fix them with the locking screw 4. For precise positioning of the cutter, you need to release the locking screw 9 and turn the fine adjustment screw 5 set the cutter to the desired position. For some models of the stop, the dimensions of the supporting surface can be changed by shifting or expanding the support pads 8.
If one simple part is added to the parallel stop, then with its help it is possible to mill not only straight, but also curved grooves, for example, to process a round workpiece. Moreover, the inner surface of the bar located between the stop and the workpiece does not have to have a rounded shape, repeating the edge of the workpiece. It can also be given a simpler form (Figure "a"). In this case, the trajectory of the cutter will not change.
Of course, the usual parallel stop, thanks to the recess in the center, will allow you to orient the router along the rounded edge, however, the position of the router may not be stable enough.
The guide bar is similar in function to the rip fence. Like the latter, it provides a strictly rectilinear movement of the router. The main difference between them is that the bar can be set at any angle to the edge of the workpiece or table, thus providing any direction of movement of the router in the horizontal plane. In addition, the tire may have elements that simplify the performance of certain operations, for example, milling holes located at the same distance from each other (with a certain step), etc.The guide rail is attached to the table or workpiece with clamps or special clamps. The tire can be equipped with an adapter (shoe), which is connected to the base of the router with two rods. Sliding along the profile of the tire, the adapter sets the rectilinear movement of the cutter.
Sometimes (if the distance of the tire from the router is too close), the bearing surfaces of the tire and the router may be in different planes in height. To align them, some routers are equipped with retractable support legs that change the position of the router in height.
Such a device is easy to do with your own hands. The simplest option is a long bar fixed to the workpiece with clamps. The design can be supplemented with side stops.
By placing a bar on two or more aligned blanks at once, they can be grooved in one pass.
When using a bar as a stop, it is inconvenient to place the bar at a certain distance from the line of the future groove. This inconvenience is devoid of the following two devices. The first is made from boards and plywood fastened together. In this case, the distance from the edge of the stop (board) to the edge of the base (plywood) is equal to the distance from the cutter to the edge of the router base. But this condition is met only for a cutter of the same diameter.. Thanks to this, the device quickly aligns with the edge of the future groove.
The following fixture can be used with cutters of different diameters, plus when milling, the router rests with its entire sole, and not half, as in the previous fixture.
The stop is aligned along the edge of the hinged board and the center line of the groove. After fixing the stop, the folding board leans back, making room for the router. The width of the folding board, together with the gap between it and the stop (if any), must be equal to the distance from the center of the cutter to the edge of the router base. If you focus on the edge of the cutter and the edge of the future groove, then the device will work with only one cutter diameter.
When milling grooves across the fibers, at the exit from the workpiece, when milling an open groove, cases of wood scuffing are not uncommon. The following devices will help minimize scuffing, which press the fibers at the exit of the cutter, preventing them from chipping off the workpiece.
Two boards, strictly perpendicular, are connected with screws. Different cutters are used on different sides of the stop so that the width of the groove in the fixture matches the width of the groove of the part to be milled.
Another open slot milling fixture can be pressed tighter against the workpiece to further minimize burrs, but it only fits a single diameter cutter. It consists of two L-shaped parts connected on the workpiece with clamps.
Copy rings and templates
A copy ring is a round plate with a protruding collar that slides along the template and provides the necessary trajectory for the cutter. The copy ring is attached to the sole of the router in various ways: it is screwed into a threaded hole (such rings are in the photo below), the antennae of the ring are inserted into special holes on the sole or screwed.The diameter of the copy ring should be as close to the diameter of the cutter as possible, but the ring should not touch the cutting parts of the cutter. If the ring diameter is larger than the cutter diameter, then the template must be smaller than the finished parts to compensate for the difference between the cutter diameter and the copy ring diameter.
The template is fixed on the workpiece with double-sided tape, then both parts are pressed with clamps to the workbench. When you have finished milling, check that the ring is pressed against the edge of the template during the entire operation.
You can make a template for processing not the entire edge, but only for rounding the corners. In this case, using the template shown below, it is possible to make roundings of four different radii.
In the figure above, a cutter with a bearing is used, but the template can also be used with a ring, only either the ring must exactly match the diameter of the cutter, or the stops should make it possible to move the template away from the edge by the difference in the radius of the cutter and the ring. This also applies to the simpler version shown below.
Templates are used not only for milling edges, but also for grooves on the plate.
The pattern can be adjustable.
Template milling is a great method for cutting grooves for hinges.
Devices for milling round and elliptical slots
Compasses are intended for the movement of a milling cutter on a circle. The simplest device of this type is a compass, consisting of one rod, one end of which is connected to the base of the router, and the other has a screw with a pin at the end, which is inserted into the hole that serves as the center of the circle along which the cutter moves. The radius of the circle is set by the displacement of the rod relative to the base of the router.It is better, of course, that the compass was made of two rods.
In general, compasses are a very common device. There are a large number of branded and home-made devices for circumferential milling, differing in size and ease of use. As a rule, compasses have a mechanism that provides a change in the radius of the circle. Usually it is made in the form of a screw with a pin at the end, moving along the groove of the device. The pin is inserted into the center hole of the part.
When it is necessary to mill a circle of small diameter, the pin must be located under the base of the router, and for such cases other devices are used that are attached to the bottom of the base of the router.
Ensuring the movement of the cutter in a circle using a compass is quite simple. However, one often has to face the need to perform elliptical contours - when inserting mirrors or oval-shaped glasses, arranging arched-type windows or doors, etc. Device PE60 WEGOMA (Germany) is designed for milling ellipses and circles.
It is a base in the form of a plate, attached to the surface using vacuum suction cups 1 or screws, if the nature of the surface does not allow fixing with suction cups. Two shoes 2, moving along intersecting guides, ensure the movement of the router along an elliptical path. When milling a circle, only one shoe is used. The fixture kit includes two mounting rods and a bracket 3, with the help of which the router is connected to the plate. The grooves on the bracket allow you to install the router in such a way that its supporting surface and the base of the plate are in the same plane.
As you can see from the photos above, the milling cutter was used instead of a jigsaw or band saw, while, due to the high speed of the cutter, the quality of the machined surface is much higher. Also, in the absence of a manual circular saw, the router can replace it.
Devices for milling grooves on narrow surfaces
Grooves for locks and door hinges, in the absence of a milling cutter, are performed using a chisel and an electric drill. This operation - especially when making a groove for an internal lock - takes a lot of time. Having a milling cutter and a special device, it can be done several times faster. It is convenient to have such a fixture that allows milling slots of a wide range of sizes.To make grooves in the end, you can make a simple fixture in the form of a flat base attached to the sole of the router. Its shape can be not only round (according to the shape of the base of the router), but also rectangular. On both sides of it, you need to fix the guide pins, which will ensure the rectilinear movement of the router. The main condition for their device is that their axes are in line with the center of the cutter. If this condition is provided, the groove will be located exactly in the center of the workpiece, regardless of its thickness. If it is necessary to move the groove to one side or another from the center, a bushing with a certain wall thickness must be put on one of the pins, as a result of which the groove will shift in the direction from which the pin with the bushing is located. When using a router with such a device, it must be driven in such a way that the pins are pressed on both sides to the side surfaces of the part.
If you attach a second parallel stop to the router, you will also get a device for milling grooves in the edge.
But you can do without special devices. For the stability of the milling cutter on a narrow surface, boards are fixed on both sides of the part, the surface of which should form a single plane with the surface to be machined. When milling, the router is positioned using the parallel stop.
You can make an improved version that increases the area of \u200b\u200bsupport for the router.
Device for processing balusters, pillars and other bodies of revolution
The variety of work that is performed by a manual milling cutter sometimes dictates the need for independent manufacture of devices that facilitate the performance of certain operations. Branded devices are not able to cover the entire range of work, and they are quite expensive. Therefore, home-made fixtures for a router are very common among users who are fond of working with wood, and sometimes do-it-yourself fixtures either outperform branded counterparts or have no branded counterparts at all.Sometimes there is a need to mill various grooves in the bodies of revolution. In this case, the device shown below may be useful.
The device is used for milling longitudinal grooves (flutes) on balusters, poles, etc. It consists of a body 2, a movable carriage with a milling cutter 1, a disk for setting the angle of rotation 3. The device works as follows. The baluster is placed in the body and fixed there with screws 4. Turning to the desired angle and fixing the workpiece in a strictly defined position is provided by disk 3 and locking screw 5. After fixing the part, the carriage with the router is set in motion (along the guide rails of the body), and milling a groove along the length of the workpiece. Then the product is unlocked, rotated to the required angle, locked and the next groove is made.
A similar fixture can be used instead of a lathe. The workpiece must be slowly rotated by an assistant or a simple drive, for example, from a drill or a screwdriver, and excess material is removed by a milling cutter moving along the guides.
Stud milling fixtures
Tenon cutters are used for milling the profile of tenon joints. In the manufacture of the latter, greater precision is required, which is almost impossible to provide manually. Tenoning devices allow you to quickly and easily profile even complex joints such as dovetails.The figure below shows an industrial sample of a tenoning device for the manufacture of three types of connections - "dovetail" (deaf and through version) and through connection with a straight tenon. Two mating parts are installed in the fixture with a certain shift relative to each other, controlled by pins 1 and 2, then they are processed. The exact trajectory of the cutter is set by the shape of the groove in the template and the copying ring of the router, which slides along the edge of the template, repeating its shape.
When using the content of this site, you need to put active links to this site, visible to users and search robots.
The recommendations of experts on how to make a tenon with a manual milling cutter ensure the convenient use of this tool in the production of furniture, load-bearing structures from lumber. Elements of tables and chairs are assembled on spikes of a simple configuration. Spikes of complex configurations of increased reliability are used for the manufacture of frames of cottages using half-timbered technology.
Figure 1. Scheme of the root tenon.
To create a spike with a milling cutter, it is enough to fix the workpiece relative to the guide surface for the sole of the power tool, set the required height of the working body - the cutter. Home-made devices from improvised materials significantly improve the quality of the spike, the safety of work, and are convenient for mass production of the same elements or interlocks on workpieces of various sizes and configurations (Fig. 1).
The choice of power tools, cutters
A standard tenon is a two-sided selection of wood from one edge of the workpiece. For this, any hand router with a collet of 12 mm or 8 mm is suitable. Rectangular slot cutter is perfect for machining two parts used in this joint:
- side surface, lower end are necessary to create a groove;
- the spike is made by the end edge of the tool with a manual milling cutter.
Figure 2. Scheme of a device for milling spikes.
Thus, having filled the cutter once, the master gets rid of the need to reinstall the tooling, which is very convenient during construction, serial production of furniture.
The dovetail spike is more reliable, durable, and for its manufacture you will need a similar cutter with the same name. However, the adaptation in this case will be completely different. The hand router for the tenon is a universal tool, so it does not need to be replaced. This type of power tool has comfortable side handles, a wide sole, and a spindle lock from turning when changing equipment. The overhang of the cutter at the moment of cutting cannot be changed due to the side stop.
Back to index
Making a stud picker
Unlike a professional machine, the working tool does not have a fixation in space. It is fed onto a fixed workpiece with both hands. Therefore, the manufacture of a device for clamping a part at the first stage is a reasonable necessity. The simplest device for this is the design (Fig. 2) of fixed guides (upper, lower, side), a movable bar, which regulates the length of the sample. To assemble it, you must perform the following steps:
- fix on a piece of plywood (along its edges) side vertical elements of the same height with central cutouts;
- cover them with guides along which the sole of the router will move;
- put side bars, limiting the course of the power tool along the upper guides;
- install a movable element on the bottom plywood, which regulates the departure of the edge of the workpiece, which is subjected to milling.
Figure 3. Spike sampling scheme.
To fix the movable bar, a standard thumb screw or special fasteners are used. The dimensions of all structural elements are selected individually:
- the height of the upper guides is equal to the thickness of the workpiece in which the spike is made, taking into account a small gap for installing a fixing wedge;
- the width of the notch in the vertical elements depends on the length of the tenon created by the hand router.
To work on this device, a manual milling cutter of any modification, manufacturer, is suitable, since most models provide for the adjustment of cutting speed, feed, departure of the working body.
For the dovetail spike, a device with the opposite principle is used:
- in a sheet of plywood, located horizontally, a power tool is motionlessly fixed;
- its body is located below, the cutter comes out from the back of the sheet into a through hole;
- a bar of hardwood (beech, birch, oak) is attached to the desktop;
- a piece of board 2.5 cm is fixed on the bar, which is a consumable (used once with a certain diameter of the cutter).
Structurally, the fixation of a manual router in a sheet of plywood is solved by several options - clamps, self-tapping screws. It is important that the fasteners do not protrude onto the working side of the plywood. The sheet itself can be attached to a workbench, lean on a couple of chairs, fixed on several rows of timber, goats, scaffolding.
Back to index
Stud selection: straight version, dovetail modification
Video 1 shows in detail how to make a spike at home, making the simplest fixture for one-time or mass production. The technology of work on the created device for a straight spike is as follows:
- the part is placed on the lower support plane on the opposite side from the movable bar;
- the edge of the workpiece, on which the spike is milled, is extended into the cutout of the upper guides until it stops in the movable element at the desired distance (the length of the spike);
- the movable bar is fixed with a lamb or a clamp;
- the workpiece is wedged with a special element between its upper plane, the upper guides;
- a hand mill is placed on the upper guides;
- the lower end of the tooling removes wood from one side of the spike;
- the workpiece is turned over, the operation is repeated for the other side of the tenon.
Dovetail wiring diagram.
The technology provides high performance for the same parts. Thanks to the device created once, you can make a spike on parts of any configuration, size. The router is set up after it is installed on the upper rails:
- the cutter is lowered to the stop on the lower plane of the plywood;
- the thickness of the part is measured;
- the tooling rises to the desired height (usually the thickness of the workpiece divided by 4).
Straight spikes for high-quality fixation in reciprocal grooves are usually connected with glue.
This ensures a high connection resource, prevents loosening of the load-bearing frame of buildings and structures during the operation of furniture (Fig. 3).
The choice of cutters for the dovetail connection is arbitrary, experts recommend a groove about half the thickness of the part. A simple way to make a structure with this connection is shown in video 2. The sequence of operations is as follows:
- horizontal placement of a plywood sheet with a manual milling cutter fixed on the underside;
- fixing one side of the guide bar with a screw (a consumable piece of the board is attached to the bar from the side of the cutting tool);
- installation of a guide bar at the required distance from the center of the cutter with fixation of its second edge to the plywood with a clamp (the width of the workpiece minus the diameter of the dovetail cutter in the wide part, divided in half);
- selection of a groove to the desired length (the width of the workpiece with a spike);
- setting the guide bar to the required distance for selecting the tenon (the clamp is removed, the cutter cuts into the consumable piece of the board in such a way that the distance from its vertical plane to the center of the cutter is: the width of the part minus the width of the groove, divided in half);
- fastening the second side of the guide bar with a clamp;
- selection of the side surfaces of the workpiece.
After fitting the spike into the groove, the thickness of the spike is adjusted. It should enter the reciprocal groove without effort, with a small gap necessary to accommodate the adhesive composition. If necessary, the guide bar is moved, milling is repeated until this condition is met.